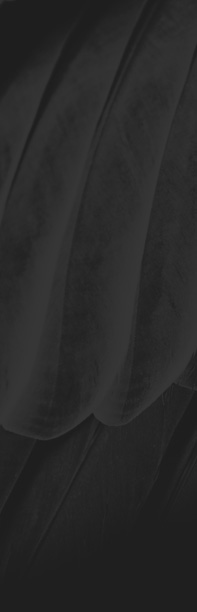
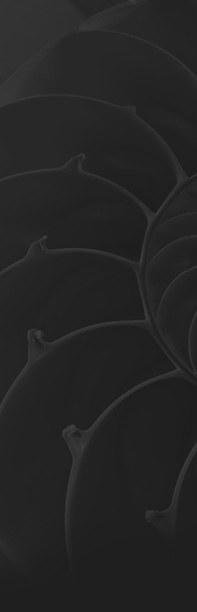
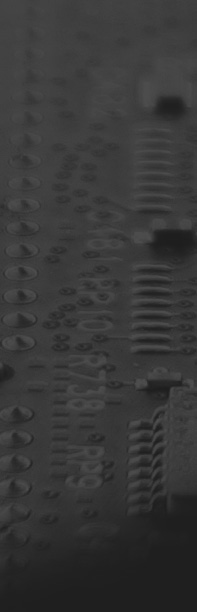
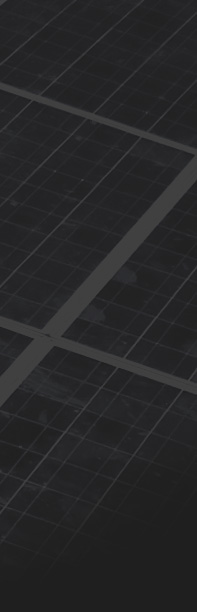
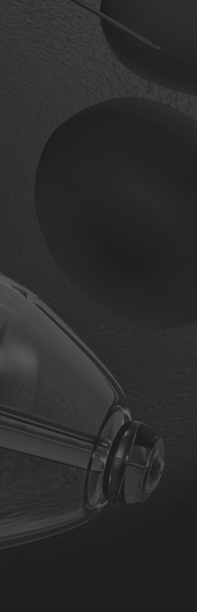
Making Stuff
David Pogue hosts a four-part special series exploring the materials that will shape our future. Airing August 21, 2013 at 9 pm on PBS Aired August 21, 2013 on PBS
- Originally aired 01.19.11
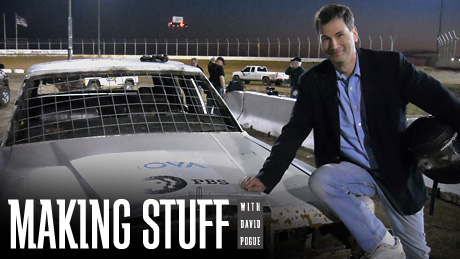
Program Description
Education and Outreach Resources
Preview | 3:19
Full Program
Full program available for streaming through
Watch Online
Full program available
Soon
Making Stuff: Stronger
David Pogue tests his mettle against the world's strongest stuff, from steel and Kevlar to bioengineered silk. Airing August 21, 2013 at 9 pm on PBS Aired August 21, 2013 on PBS
- Originally aired 01.19.11
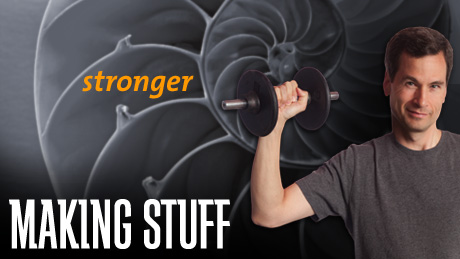
Program Description
Transcript
Making Stuff: Stronger
PBS Airdate: January 19, 2011
DAVID POGUE (Technology Reporter, New York Times) Imagine a world with smart buildings that can ride out any disaster; bacteria that make gasoline out of thin air; computers that think and place all the world's knowledge in your pocket; an end to surgery, with tiny devices that can repair cells, even D.N.A.; gossamer threads, strong enough hold up a bridge; or an elevator to the stars. These visions of the future are all based in the discoveries of today, as a new science of materials emerges from the elemental building blocks of the universe, promising a future in which we can create virtually anything we want, atom by atom.
Can I have some rock music please?
I'm David Pogue, and I am on a quest to find the world's most advanced materials.
A narrow wire that can bring a fighter jet to a dead stop in less than three seconds...
Welcome to Navy Airlines!
...super strong, but not unbreakable. What new material might replace it?
A manmade fiber that can stop a bullet?
Whoa!
Nature is our guide in this quest.
These are your lab assistants?
Inspired by the beak of a tropical bird.
Er, they were all out of parrots.
Or a lightweight thread spun by spiders, now made from goats' milk.
So this one's skim and this is two percent?
It's stronger than steel!
We're learning how to make stuff stronger than ever, and it's going to change the world.
Marc Meyers (Materials Scientist, University of California, San Diego): You should try, too.
DAVID POGUE: Right now,...
Well it would snap if I had any upper body strength.
...on NOVA.
Here I am, inside a Navy plane. I'm on a quest to find the strongest stuff in the world. We're headed for that: the U.S.S. John C. Stennis. I can't believe it's possible to land on that thing.
But down on that tiny deck, there's a lifesaving piece of equipment that's supposed to be strong enough to bring our plane to a dead stop. Man, I hope that thing holds!
We're going down.
Wow, I really felt that! Now I want to see how it works.
Welcome to Navy Airlines!
Luckily, I've arrived at the perfect time, because a dozen new pilots are practicing their landings. That means lots of attempts to catch that wire.
There are actually four cables across the deck. They're working on number three right now. So this guy's going to try to catch number four. That's the ideal one. Let's see if he does it.
The jets land under full power, briefly exerting hundreds of thousands of pounds of force on a cable that's only an inch and a half thick. How is it possible that such a thin wire can have so much strength? I head below deck to get a closer look.
So, I think I understand how these planes land, because I came in on one of these planes. The plane has a hook underneath, and then there's this big steel rubber band on the deck that stretches a little bit, then un-stretches. Am I right?
Scot Vannorman (United States Navy): No, sir. It looks like that, yes, it does, but that actual rubber band that you're talking about, the actual wire, comes down here and actually leaves from here. This is actually the cable that you're going to see going across that flight deck.
DAVID POGUE: Every time a plane hits the cable, this powerful hydraulic piston goes into action. By spooling out wire at just the right speed it counteracts the momentum to slow the aircraft. The bigger the plane, the harder it pulls. It's designed to withstand a truly massive load.
SCOT VANNORMAN: The breaking strength of the cable is 215,000 pounds.
DAVID POGUE: That's enough strength to stop four F18s at once. Amazing! And it's all thanks to a strong material that the Navy trusts above all others.
The entire ship is made of steel.
Don't believe me; tell it to the magnet.
Steel.
Steel provides the structural strength of the bulkheads, and the decks.
Steel!
And, of course, the all-important arresting cable.
In the quest to find strong materials, steel is a great place to start. Our modern civilization is built on the stuff, but where does it come from?
Thousands of years ago, ancient people used tools made of stone. That's why it's called the "Stone Age." But, eventually, they discovered how to extract metals like copper, tin and iron from rocks. Iron is the main ingredient in steel, but steel is stronger than iron, because it also contains carbon.
All these materials fill the periodic table of the elements, a master chart that that lists the basic building blocks of every material in the world, from the lightest to the heaviest, from the weakest to the strongest.
The ability withstand pulling forces is called tensile strength. And steel has it in abundance. But it's not unbreakable.
Each time a plane hits the wire, the impact takes a toll, with potentially disastrous results. In 2003, this fighter had nearly come to a complete stop when the cable suddenly snapped. The plane was lost but the pilot ejected to safety. Sudden failures like these are rare, because the crew doesn't wait for the cables to wear out.
So the doubled up cable down here on the pulleys, you, you replace that how often?
SCOT VANNORMAN: Every two thousand arrestments.
DAVID POGUE: And, they're connected to one across the deck up there that has to be replaced every...
SCOT VANNORMAN: One hundred and twenty five.
DAVID POGUE: How come so much more often?
SCOT VANNORMAN: Well, the one on the deck—we call it the cross-deck pennant or C.D.P.—the C.D.P. takes the blunt force of the tailhook: metal-to-metal contact at a hundred and thirty to a hundred and forty miles per hour, a hundred and twenty-five times.
DAVID POGUE: It's amazing that they haven't found some material in the whole world that would last more than a hundred and twenty five landings.
SCOT VANNORMAN: I don't know of any metal that can do that yet.
DAVID POGUE: Steel has incredible tensile strength, but can it be improved?
Can we make this stuff even stronger?
That's what Ellwood Steel has tried to do for the last century. They've developed and produced high-strength steel for everything from aircraft crankshafts in World War II to high-performance windmill generator shafts and other steel components. It's all based on the same basic materials, first combined thousands of years ago.
John Paules (General Manager, Ellwood Technologies): The end product, steel, is a mostly iron—99 percent or so—iron with a little bit of carbon. First we melt it, and then we refine it. We remove all the impurities we can to get the properties that we need from the steel.
DAVID POGUE: At this plant, the raw material is scrap steel, to be recycled. First it's loaded into an electric furnace for melting.
When the mix reaches 3,000 degrees Fahrenheit, the liquid metal pours out of the bottom of the furnace into a ladle. Today, they're making steel for jumbo jet landing gear, extremely strong and stiff. Besides iron and carbon, the recipe calls for several additional elements, added in precise quantities. After cooling, a simple test reveals whether the steel has the right amount of tensile strength.
John Paules: When we pull a piece of steel, we measure how much it stresses. We keep increasing the load; we watch it stretch, until it eventually breaks.
DAVID POGUE: The more force it can withstand, the greater the tensile strength.
Where does steel's remarkable strength come from? In metals like iron, atoms are packed together like sheets of marbles. But when pushed or pulled, they can slip and slide past each other.
But steel also contains carbon. The carbon atoms fit in between the iron atoms, limiting their freedom of movement, making it harder to pull them apart. Steel makers long ago learned that by adding more carbon, you can increase the steel's tensile strength, but you give up flexibility, which is something that the arresting cable needs to wind and unwind. The trick is to find just the right balance.
John Paules: Including steel, there's always been a tradeoff between very high hardness, high strength and flexibility. Steel has provided a very good combination of high strength and good flexibility for many applications. That's why it's so widely used.
DAVID POGUE: Without steel's tensile strength to resist fracture, elevator cables would snap and bridges would crack in two. That alone makes it an incredibly valuable strong material. But steel protects us in other ways too. Carmakers depend on a different kind of strength in steel, which is on display at the Outlaw Motor Speedway in Muskogee, Oklahoma.
Materials scientist Mark Eberhart is here to help me understand what makes car bodies strong. And to do that that, we first have to watch them break.
Mark, you're a prominent scientist, author, teacher. Why are we at a dirt track in Oklahoma?
Mark Eberhart (Metallurgist, Author, Why Things Break): I've been fascinated with understanding why things break since I was about six years old. You can go into a lab, and you can do real detailed experiments—they don't capture the full beauty of why things break. This is the place to come to really understand what a person means when they say strength.
DAVID POGUE: We're the Starsky and Hutch of science nerds.
Can I have some rock music please?
Frankly, I wouldn't mind watching from the stands, but Mark insists that only by becoming crash test dummies ourselves can we understand how steel makes car bodies strong.
Mark Eberhart: Most people don't think of strength as kind of a monolithic thing, but it really is a combination...
DAVID POGUE: Hey, what's your hurry pal? Sorry about that.
Mark Eberhart: It's really a combination of properties. It's not just one property, the way most people use the word.
DAVID POGUE: So, really, when we say "strong as steel," it's a little more complicated than that?
Mark Eberhart: Oh, absolutely.
DAVID POGUE: Besides tensile strength, resistance to pulling, there's also toughness. It's a measure of how much energy a material can absorb without breaking.
When a car crashes and the body dents, the steel is absorbing the energy of the crash. That's toughness.
During our 100 laps the car took some serious hits. Did the steel demonstrate toughness?
You know it's not all that much different from Manhattan at rush hour. Let's check this puppy out.
Mark Eberhart: There's some damage over here.
DAVID POGUE: The body got creamed, but, the steel didn't break. It's dented, yet still intact. Our driver, Danny, suggests an even more extreme test of steel's lifesaving toughness.
So what do you got set up for us here?
Danny Womack (Owner, Outlaw Motor Speedway): We're going to take this car, we're going to send it into the wall and see what we can tear up.
DAVID POGUE: Danny locks the steering wheel in place and opens the throttle. Now it's up to me to do the honors.
In the name of science!
We installed a small camera where the driver would normally be.
Danny Womack: Ha ha. That was great.
DAVID POGUE: The impact was far more intense than anything we experienced during the race.
Mark, talk us through what's going on here.
Mark Eberhart: What we can see here is that we've exhausted a lot of the energy and just crumpling this thing up. I think we knocked the axle all the way back. Tell me, is that the case, Danny?
Danny Womack: It looks like it.
Mark Eberhart: It knocked it all the way back into the firewall.
Danny Womack: That deal'll buff right out.
DAVID POGUE: Would you have lived, Danny?
Danny Womack: I would have had a heart attack somewhere between there and here. I don't know.
DAVID POGUE: Yeah.
Amazingly the car took everything we threw at it. If the material hadn't been tough, if it had been too brittle, the damage would have been lethal. But in this case, people would have survived, because the steel absorbed the energy of the collision. The amount of carbon in the steel is low enough to let the atoms move just a bit, allowing the steel to bend but remain intact. That's toughness.
You know, who says science can't be fun? That was pretty cool.
Steel makes the biggest structures on Earth possible. And in the future, when buildings reach a mile or more into the sky and bridges stretch across the sea, steel will be there to support humanity's dreams, because we haven't come close to exhausting the potential of this most precious metal. But no material is perfect. Even metals have their weaknesses.
Consider the suit of armor. Warriors once wore bronze, iron and steel onto the battlefield. Sure it was heavy, but it provided good protection, until around the 15th century. When the gun appeared, heavy armor became a liability.
So, for hundreds of years, infantry in the world's bloodiest wars went to battle with little to protect them, because the metal was no match for a bullet. Why?
Luckily, I have a personal connection to a place where we can see exactly how metals fail under fire.
This has got to be my favorite spot at M.I.T., Strobe Alley, dedicated to the work of my great-uncle Harold Edgerton, a pioneer in the art of high-speed photography.
I remember, when I was a kid, he was always showing us pictures of what he was doing. He was smashing light bulbs, shooting bullets through apples, stuff like that. I thought, "That's the coolest job in the world."
Our plan today is to fire small, .22 caliber bullets at several different types of metal. Using a high-speed video camera, we'll examine the exact point when the bullet hits and we'll examine the type of hole it creates.
Jim Bales, who runs Strobe Alley will be our triggerman.
Jim Bales (Edgerton Center, Massachusetts Institute of Technology): We've got two cameras. This one's running at 20,000 f.p.s. This one's down at a mere 4,000 f.p.s.
DAVID POGUE: Yeah, and, for point of comparison, normal television like this that you're seeing right now is 30 f.p.s. So these are running a good bit faster.
First up, a piece of steel. It provides about as much protection as a 15th century breastplate.
Jim Bales: Three, two, one.
DAVID POGUE: Even this small caliber bullet easily penetrates, leaving a jagged hole.
Looks like someone has ripped a hole through a piece of paper.
To provide enough protection for a soldier's torso, this steel would have to be 10 times thicker. It would weigh an unwieldy 100 pounds.
What about a lighter weight material, like aluminum?
We see it mostly as flimsy rolls of foil but some forms of aluminum are just as strong as steel and are widely used in aircraft construction. Could aluminum serve as armor?
Lo and behold, there's a hole in the metal. Metallurgist, Mark Eberhart:
Mark Eberhart: This is beautiful. The energy of the bullet or much of the energy went into folding that metal back.
DAVID POGUE: The aluminum shows even more tearing at the point of impact. Pieces of metal light enough to be worn as armor aren't tough enough to stand up to the focused energy of a gunshot. When a bullet strikes the surface, the energy of impact is transferred to the metal in the form of heat, which causes the atoms to slide past each other.
Because the energy is focused on such a small area, the movement can be severe, causing cracks to form. If the material is thin enough, the bullet tears right through, like a hot knife through butter. So wearing a full metal jacket into combat is not a wise idea.
But if guns made personal armor obsolete, what are these guys wearing? It looks like cloth, but it's stronger than steel, and it's become standard equipment for soldiers, swat teams and bomb disposal squads.
I'm talking about Kevlar. When this synthetic fiber is woven into a fabric, Kevlar is strong enough to stop a bullet, or a blade, or even, with a few chemical changes,...
Ha ha.
...a fire.
Oh, it's hot, although, not as hot as he is.
Tucker Norton (Ballistics Scientist, Dupont): David, what you're about to see here are all the examples that we've got of Kevlar.
DAVID POGUE: This is Tucker Norton, ballistics expert and my tour guide here at DuPont, the company that invented the stuff.
Tucker Norton: Over here, we have some examples of vests where Kevlar is being used.
DAVID POGUE: Can I try one of these on?
Tucker Norton: Absolutely.
DAVID POGUE: Okay, I'm not here to show off the spring collection but to understand what makes this stuff so strong.
Kevlar, so important to American soldiers today, has its roots in a time when the entire United States was in peril. In the early '30s, the Japanese empire seized control of the world's silk supply, a material used to make parachutes and flak jackets. A frantic search began for a manmade replacement. Then in 1935, Wallace Carothers, a brilliant chemist at DuPont, created nylon, the first fiber made in a test tube, not in nature.
His breakthrough ushered in the modern age of synthetics. Then, in the 1960s, Stephanie Kwolek, a chemist, also at DuPont, created Kevlar. It remains the strongest synthetic fiber ever produced.
I know Kevlar can hold up in the most extreme punishment, but I want to see it up close. Our target: a block of clay designed to simulate the human torso.
It's protected by several layers of Kevlar. On the other end: the weapon, or rather the "bullet delivery device."
This is the gun?
Tucker Norton: This is the gun.
DAVID POGUE: Oh, I was expecting a "gun."
Tucker Norton: No, none of that.
DAVID POGUE: Oh, you're kidding?
What's going to happen? Someone's going to pull the trigger and... is there a trigger?
Tucker Norton: So the trigger is located outside of here. We don't actually do anything firing here, while we're inside.
DAVID POGUE: You guys are these giant safety wusses.
Tucker Norton: Now, here's where we go to fire.
DAVID POGUE: I feel like the President, failsafe.
Okay, ready, aim, fire!
Tucker Norton: You did it.
DAVID POGUE: Geez, I am so good.
Time to inspect the damage. Even with Kevlar, the simulated chest takes a beating.
Whoa! This is...this would have been my chest?
Turns out it looks worse than it is.
Tucker Norton: Unlike the human body, this clay will hold its position. The human body will respond and go back to normal.
DAVID POGUE: So, on a human, this would just be a really nasty bruise?
Tucker Norton: Yes.
DAVID POGUE: And maybe a broken rib?
Tucker Norton: That's right.
DAVID POGUE: Gotcha.
Tucker Norton: That's right.
DAVID POGUE: Still, ouch! But where's the bullet?
In fact, it's in the bag.
Tucker Norton: The bullet's still in here.
DAVID POGUE: Oh, my gosh. Can we see it?
Tucker Norton: Absolutely. So we have many, many layers, of course. The first one, second one, and usually about the third layer is where it gets stopped. And there it is. There's the bullet.
DAVID POGUE: Oh, my gosh.
It took just four layers of Kevlar, each less than a millimeter thick, to stop the bullet. The seven other sheets kept that hole from getting any deeper.
Tucker Norton: And as deep as any type of trauma might look, it's much better than that bullet going all the way through you.
DAVID POGUE: Right, I guess I could agree with that.
Kevlar is clearly some tough stuff.
Whoa!
But how does it work?
Tucker Norton: If you were to zoom down at about 100-million times...
DAVID POGUE: Well, we have a really nice camera, can you zoom down 100-million times?
Kevlar is a polymer, a long repeating chain of atoms, in this case, carbon, hydrogen, oxygen and nitrogen. Each chain is like a stiff piece of spaghetti. Gathered into bundles, the stiff chains create a thread-like fiber that has a hard surface, extremely high tensile strength and enough toughness to absorb the impact of a bullet.
Stopping a round is impressive, but there are other threats out there. How does Kevlar stand up to a knife or an ice pick?
Don't try this at home.
I'm not going to pay a lot for this muffler!
I said, "Caesar, on the side."
Twenty cents a text message? Are you nuts?
That's amazing. How can it do that?
Tucker Norton: Well, it does it because of the tight weave and because of the strength and durability of Kevlar. The tight weave prevents the spike from getting all the way through, from working its way through. And the strength of that Kevlar actually helps blunt that tip and maybe even bend that tip if you are strong enough.
DAVID POGUE: Since it was invented, Kevlar has been used in all kinds of products, from tires to parachutes and even cables. And that gives me an idea.
Tucker, I've got this friend. Um he's got a fleet of nuclear aircraft carriers and, they have these steel cables, a lot like this, that are designed to stop aircraft that are landing, 130 or 150 miles an hour. How does the strength of one of these cables compare with a steel cable?
Tucker Norton: Well, we'd expect the strength of this, the tensile strength, to be actually equal or better than something like the steel cable.
DAVID POGUE: And, it's lighter and it's less dangerous if it snaps?
Tucker Norton: That's right.
DAVID POGUE: Tucker doesn't think that anyone has ever tested Kevlar arresting cables, but I think I may be on to something.
This, this could be a sales opportunity for you.
Tucker Norton: We appreciate that, thank you very much, David.
DAVID POGUE: I'll look for my commission.
With its tensile strength greater than steel, extreme flexibility and heat resistance, in a package that weighs one-fifth as much as steel, Kevlar could, one day, be a replacement for steel cables. But already there may be other, stronger alternatives.
Scientists like Ray Baughman, at the University of Texas, are exploring the remarkable properties of a brand new material.
I'm talking about the carbon nanotube.
Ray Baughman (Chemist, University of Texas at Dallas, NanoTech Institute): Dave, this is one type of carbon nanotube.
DAVID POGUE: This is what it's all about, right here?
Ray Baughman: This is what it's all about.
DAVID POGUE: You know, I had a hunch they'd be like this. I just thought they'd be smaller.
I'm right. They're about a billion times smaller. Nanotubes are made of carbon atoms arranged in a rolled up, chicken-wire like structure. Besides nanotubes there are other forms of pure carbon, like diamond and graphite, the stuff of pencil lead. Nanotubes get their strength from the extremely strong bonds between carbon atoms.
Ray Baughman: These carbon nanotubes can have spectacular mechanical properties, spectacular strength and very high toughness.
DAVID POGUE: And you make them here in this very lab?
Ray Baughman: Yes, we do.
DAVID POGUE: Ah, so this is where it all happens.
Ray Baughman: This is where the process begins.
DAVID POGUE: And guess what? It's not even that difficult. Here's all you need:
One, a smooth surface with a thin layer of catalyst, a chemical that helps jump-start the tubes; two, a special mix of gases, full of carbon atoms, and three, this furnace, which, by the way, is really, really hot.
How much heat is it in there?
Mírcio Dias Lima (University of Texas at Dallas, NanoTech Institute): Right now, it's around 800 Celsius.
DAVID POGUE: That's about 1,500 degrees Fahrenheit.
Wow, man, I could nuke a pizza in like five seconds in there.
Mírcio Dias Lima: Yeah.
You can open more. More. See the nanotubes?
DAVID POGUE: Oh, man, that is blasting heat. Oh, I see the little black wafer in there. That's it?
Mírcio Dias Lima: Yup.
DAVID POGUE: That's nanotubes?
Mírcio Dias Lima: Those are, yes, exactly.
DAVID POGUE: Wow. That is very cool, baking away in there. Wow, it's like a nuclear tanning bed.
After just a few hours, the wafer is covered with a thick, black fuzz.
So, it looks just like a piece of black velvet.
So, if I were to really look in close to that, what would I see? What's it really look like under the microscope?
Ray Baughman: Well, we call this array of carbon nanotubes a nanotube "forest."
DAVID POGUE: The name is apt. Each nanotube looks like a tall and thin bamboo tree: hollow inside, so thin that if you could scale one up until it was one inch wide at the base, the top of it would reach two miles into the sky. Now, picture nanotubes by the billions, all standing shoulder to shoulder and you have one of Ray's nanotube forests.
Ray Baughman: There are, in fact, there are about 200 billion of carbon nanotubes in that area.
DAVID POGUE: Hold on one second, I'm going to count them.
Actually, I shouldn't be touching these. Scientists don't yet know if they are toxic.
Even so, there is already a rapidly-growing market for nanotubes particles as strength additives for tennis rackets, bicycle frames, even high-end car bumpers. Many products already incorporate carbon fibers, which are part carbon, part plastic. But nanotubes have greater tensile strength and toughness. Ray has set his sights on making super-strong materials that are 100 percent pure nanotube, made from his nanotube forests.
Ray Baughman: These aren't just ordinary carbon nanotube forests. They are nanotube forests that have a very special type of connectivity between nanotubes.
When we pull out one nanotube, that nanotube pulls out its neighbors, who pulls out other neighbors, to self-assemble a yarn or a sheet.
DAVID POGUE: Expert nano-yarn spinner Chi Lewis Azad gives me a hands-on lesson.
Chi Lewis Azad (University of Texas at Dallas, NanoTech Institute): Would you like to try?
DAVID POGUE: This I recognize.
First, we start with a forest on a wafer.
Chi Lewis Azad: You see, you can just grab on to this little orange tab. Now, don't make it too high of an angle, and make sure it doesn't touch the edge, and just pull out.
DAVID POGUE: Fast or slow?
Chi Lewis Azad: Whichever you feel comfortable with.
DAVID POGUE: Oh, dude!
As I pull on this little tab, nanotubes are coming off of the wafer, hooking other nanotubes and pulling them off of the slide.
Chi Lewis Azad: Try faster.
DAVID POGUE: I'm so good at this.
Chi
Lewis Azad: At too high of an angle it
will—as this is now
—it will start to break off from the forest.
DAVID POGUE: It's like coming out forever. I'll see you at the Texas county line!
It's still going, it's still going.
Chi Lewis Azad: It's still...There, it broke.
And, what's even neater, I can show you right here, I can even do a little
twist.
DAVID POGUE: Oh, you're making...
Chi Lewis Azad: Make it into a yarn right here.
DAVID POGUE: Insta-yarn.
Chi Lewis Azad: Look at that.
DAVID POGUE: Wow.
Chi Lewis Azad: It's about 1/100th of a human hair.
DAVID POGUE: Oh, my gosh. It is like steel. I'm pulling really hard. You probably can't even see that. In fact, look at this. It's so fine, you can't even see it.
Oh, that helps.
Chi Lewis Azad: Uh hunh. Keep twisting, keep twisting.
DAVID POGUE: Keep twisting? Okay.
It's amazing!
Chi Lewis Azad: It's stronger than steel.
DAVID POGUE: Stronger than steel? So why then, don't you take a bunch of these, twist them together, and make this super-cable that would be like bridge suspension cables and aircraft carrier cables?
Chi Lewis Azad: Can you imagine spinning a bunch of these all day long, to make into a rope that's a foot in diameter?
DAVID POGUE: Okay, so go the other way. Make the aircraft carriers really, really small.
Chi does have a point, for now. But in the future, materials we make may be strong, light and cheap enough to build incredible structures: a bridge across an ocean, suspended by cables made of fibers like Kevlar or nanotubes; a geodesic dome over an entire city, its structure made of carbon.
And in the future, we may not merely make these materials, we may grow them. That's what Mother Nature has been doing for hundreds of millions of years, engineering strength into the bodies of animals, one atom at a time.
Meet Marc Meyers. He's been fascinated by nature's engineering tricks ever since a boyhood encounter in a Brazilian forest.
Marc Meyers: My father was hunting, and I saw this entire toucan skeleton. Then I picked up the beak and I was amazed at how light it was, and how strong it was.
DAVID POGUE: The memory stayed with him for 30 years, until he happened to stumble across, of all things, a toucan farm. There, he made a startling discovery. In the toucan's amazing beak, nature has constructed a large, lightweight and amazingly tough structure. He wanted to know how.
I'd like to know why. Conservationist Joan Embery is on hand to explain.
What is the point of this huge beak? I mean, it does look a little ridiculous.
Joan Embery (Embery Institute for Wildlife Conservation): Well, they're primarily a fruit-eater, and that extends their reach. They use it as a screwdriver. They use it to find food. Also works defensively as a dagger. The edges are serrated.
DAVID POGUE: You tell me that now, when the thing is like six inches from my eye?
Joan Embery: That's why you're holding the tame toucan.
DAVID POGUE: Oh!
When Marc analyzed the beak of the dead bird, he found that it was made out of two different materials, neither one of which is strong.
On the outside is the shell. It's like bendable plastic, it feels like a, like a fingernail.
Marc Meyers: If the beak was just like this, it would flex. It would, it couldn't grab anything.
DAVID POGUE: The inside of the shell is filled with bone, but bone that's so full of air pockets it's as weak as Styrofoam.
Marc Meyers: See how it can break easy? You see?
DAVID POGUE: Right. Nothing.
Marc Meyers: And, oh, you should try, too.
DAVID POGUE: Yeah, exactly. Well, it's, it's foam, so it snaps. Well it, it would snap if I had any upper body strength.
The thin shell and the foamy bone, neither one is tough , but when combined...
Marc Meyers: You can see that this is the foam.
DAVID POGUE: Mm-hmm.
Marc Meyers: And then we have the shell.
DAVID POGUE: Right. Each by itself...
Marc Meyers: ...is weak.
DAVID POGUE: ...is weak.
Marc Meyers: I can show...yeah. If you pull out...it can bend this, here, very easily. Here, you see?
DAVID POGUE: Yeah.
Marc Meyers: And, uh...
DAVID POGUE: And this I could snap, if it weren't an important teaching tool for you?
Marc Meyers: That's right.
DAVID POGUE: Yeah. And if you combine them...
Marc Meyers: And now, if you take and try to bend these two together, see?
DAVID POGUE: Oh, wow.
Marc Meyers: Yeah.
DAVID POGUE: It's like super-lightweight concrete. It feels...
Marc Meyers: Right.
DAVID POGUE: It feels like nothing.
Marc Meyers: It is strong, and it is, uh, it is very lightweight.
DAVID POGUE: Marc was amazed that evolution had solved such a difficult engineering problem. So he began looking for other examples of animal engineering, which soon led him from the jungle to the beach.
This is your lab? You work in a wetsuit on a table by the ocean?
Marc Meyers: For today it is. I've been, ah, studying, actually, these shells, the abalone, for some years, because they are very, very strong.
DAVID POGUE: The abalone has evolved to have a very tough shell which protects it from the pounding surf and from predators like sea otters.
What is this shell made of? It's not...you're saying it's not like other shells?
Marc Meyers: It's calcium carbonate, which is the same as chalk.
DAVID POGUE: Chalk? Huh.
Marc Meyers: But it's much, much stronger than chalk.
DAVID POGUE: Yeah, chalk is not especially strong. I notice, by pure coincidence, there's a piece of chalk right here. And I don't think of chalk as sea-otter-proof. I mean, it just crumbles.
Marc Meyers: It crumbles.
DAVID POGUE: The fact that it pulls apart so easily shows that chalk has very little tensile strength or toughness. But that's not the end of the story.
Marc tells me not to be fooled by chalk's apparent weakness, because it's actually a very strong material.
I was never any good at dominos.
Marc Meyers: Now, you said that this is weak, right?
DAVID POGUE: Yeah.
Marc Meyers: You broke it with your, uh...
DAVID POGUE: My bare hands.
Marc Meyers: Yeah. And now I'll show to you that you can put your entire weight here, if you step carefully, here.
DAVID POGUE: Use you as a ladder?
Marc Meyers: Yeah.
DAVID POGUE: Alright.
Marc Meyers: Put more in the middle.
DAVID POGUE: More in the middle?
Marc Meyers: Yeah, yeah.
DAVID POGUE: You've got to be kidding me. This is going to shatter 'em like glass.
Marc Meyers: See?
DAVID POGUE: Wow! One-hundred-eighty-five pounds of pure muscle!
Marc Meyers: Yes.
DAVID POGUE: Look at that!
What's going on here?
Chalk can withstand tremendous pressure. It's called compressive strength, and it's a property of ceramics, the stuff of pottery, bricks and the cement in concrete. But ceramics also have a weakness.
Bend them, drop them, shoot them or even take a hammer to them...
For your $25 pledge, we'll send you this handsome coffee mug.
...and they shatter.
As with other materials, the strength or weakness of ceramics is determined by how their atoms bind together. Chalk is made of calcium, carbon and oxygen atoms, which are bonded together tightly, with no wiggle room. They can't slide past each other. That lets them to stand up to tremendous pressure. But if a small crack manages to open a space between the atoms, it can quickly spread. That's why materials like chalk, even though they have high compressive strength, often seem fragile.
Take glass, another fragile material. Marc insists that it also has high compressive strength, even more than chalk. Frankly, that seems hard to believe.
Okay, here we go. I'm going to wind up with an ankle full of glass.
Oh, my gosh! The chalk is one thing, but these little skinny wineglass stems are something else entirely.
Marc Meyers: Now are you willing to try it with three or two?
DAVID POGUE: No.
Three glasses! Three glasses! Where's the Cirque de Soleil agent when you need him?
Marc Meyers: That's amazing! You did it!
DAVID POGUE: Alright, Marc, explain this in science terms, quick!
Marc Meyers: Ceramics and glasses, when we compress them, they're very, very strong, stronger than metals.
DAVID POGUE: Okay, shall we try one?
Marc Meyers: Yes go for it!
DAVID POGUE: Let's do one glass. One glass, people!
Marc Meyers: Let's do it!
DAVID POGUE: Whoa! Whoa! Oh, my god! I can't believe it! How is this possible?
Marc Meyers: You did it, Dave.
DAVID POGUE: One glass! I'm amazing!
Marc Meyers: It's the world record.
DAVID POGUE: Oh, my gosh! One glass, people! One glass! Watch quickly!
While that is impressive, the abalone shell blows glass and chalk out of the water, so to speak.
Like the toucan shell, it combines two materials to make its fortress of strength and protection. Its shell is 95 percent calcium, carbon and oxygen, just like the chalk, but it doesn't have the same brittle weakness. It's not fragile.
You're saying this is 95 percent the same as this, but this...
Marc Meyers: Yeah, but, try to break this.
DAVID POGUE: But this one...really?
Marc Meyers: Yeah, go ahead.
DAVID POGUE: This would cost a fortune at the gift shop.
Marc Meyers: No, yeah, go ahead. I dare you.
DAVID POGUE: Okay, if I were a sea otter, I would be a terrible failure. It's completely... Nope.
The shell demonstrates both compressive strength and toughness, the ability to absorb energy without breaking, thanks to the way that the abalone has engineered its protective cover on a microscopic scale.
As it constructs its shell, the abalone gathers calcium, carbon and oxygen from the environment to build rows of tiny, hexagonal plates. Each plate is brittle, but between the layers, the abalone inserts a protein, a long biological chain. That small addition acts like a shock absorber between the plates. The resulting shell is far less brittle, much tougher and more crack-resistant than simple chalk.
As we learn to apply the lessons of microscopic structure, engineers may one day build pressure-resistant ceramics and glass from the atom up, beautiful buildings of sculpted concrete that will never crack and will last 1,000 years, or a deep sea city with a spectacular view.
But when it comes to strong, light and flexible materials, built atom by atom, another natural material may hold the key.
It's not new. In fact, it's been around for hundreds of millions of years: spider silk. Spider silk has been shown to have more tensile strength than steel and Kevlar. It can stretch to 140 percent of its length without breaking and remains flexible, even in extreme cold. It's also so lightweight that a mere pound of the stuff could form a single strand long enough to stretch around the equator.
But could we harvest enough to put it to use?
I paid a visit to the American Museum of Natural History, in New York, where I met Nicholas Godley.
This is it? This is your baby?
Nicholas Godley (Fashion Designer): This is the big one.
DAVID POGUE: ...who enlisted the help of more than a million spiders to make this breathtaking piece of fabric.
Nicholas Godley: It's the largest known textile and sample of piece of spider silk in the world.
DAVID POGUE: To truly appreciate this remarkable material, you have to feel it.
The main piece is so valuable it's off-limits, even to its creator, but Nicholas has brought a smaller sample.
It feels really, really, really soft, like animal wool or something.
Nicholas Godley: I challenge you to break off this piece.
DAVID POGUE: I'm going to break before it does. Okay, it does not...it's like pulling a strand of steel. Wow!
It's beautiful and it's super-strong. Could we ever put spider silk to practical use?
Nicholas Godley: It's very difficult to do this on a commercial scale. It took a million-sixty-three-thousand spiders, roughly, to make...
DAVID POGUE: Geez!
Nicholas Godley: It takes about 20 minutes for each spider, and they produce about 400 yards of thread.
DAVID POGUE: Each thread was pulled, by hand, from a spider's spinneret.
It took four years and millions of strands to weave this 11 foot-long masterpiece. Its rarity is a testament to the sheer difficulty in harvesting this material. But that may soon change, thanks to this guy.
Randy Lewis (Molecular Biologist, University of Wyoming): So here's where we keep our spiders. Um, we have special little cages for them, in this room.
DAVID POGUE: Spider central, huh? Whoa, not funny. Not funny!
Randy Lewis: You're now an official Spiderman affiliate!
DAVID POGUE: This is Randy Lewis, a biologist at the University of Wyoming, who's stuck on spider silk.
Wow.
Randy Lewis: This is a golden orb weaver.
DAVID POGUE: Golden orb weaver?
RANDY LEWIS: Just cup your hand and get behind her.
DAVID POGUE: Why is she making a web right now?
RANDY LEWIS: Because she wants to make sure if she falls, she catches herself.
DAVID POGUE: Oh, so she's constantly spinning out that dragline.
RANDY LEWIS: Whenever they move, they leave the dragline behind. That's kind of where it got its name.
DAVID POGUE: Randy has been fascinated by the amazing properties of dragline silk for fifteen years.
And he knows all too well the difficulty of extracting silk from spiders. So he set out find a way to mass produce the stuff, in hopes of revolutionizing the world of strong materials.
Wyoming is ranch country, so when Randy began to consider how to solve the problem, his thoughts turned to livestock. He figured maybe he could combine a little old-fashioned animal husbandry with the emerging science of genetic engineering.
Now, thanks to Randy, these goats have just a little bit of spider in them.
"Transgenic," that's the word for what these goats are.
RANDY LEWIS: Right. It means that they have a gene from another organism that's been put into their chromosomes.
DAVID POGUE: Genes are sections of D.N.A. that contain the encoded instructions for making proteins.
Scientists identified the two genes in spider D.N.A. that make silk. They copied one of the genes and spliced it into the D.N.A. of goats so that they would make spider silk protein in their milk.
I'm a little worried about what we're going to find in here—eight-legged goats, giant dripping webs?
Randy Lewis: You won't be able to tell the normal goats from the transgenic goats, 'cause they're all exactly the same.
DAVID POGUE: Aww, I had a dog like you once.
It's impossible, just by looking, to tell these goats from their non-spidey brethren, but, scientifically, they're very valuable.
Yeah, you're special. You've been genetically modified. How does it feel to be genetically modified? Huh?
Only 50 percent of Randy's goats will inherit the necessary gene, and the females that are born with it will go on to produce spider silk protein in their milk.
And that's what I've come all this way to see for myself.
Can I... try it?
Randy Lewis: You're certainly welcome to. We normally use the electric, just because it's a whole lot faster, but, um, you're welcome to
DAVID POGUE: Faster? But you've never seen me milk a goat.
Randy Lewis: All right, well, you're about to find out here.
DAVID POGUE: So this one's skim and this is two percent?
RANDY LEWIS: Well, in this case, they're both spider silk. You can choose either one you want.
DAVID POGUE: Okay, so I just grab and tug, just like...?
Randy Lewis: Right, just squeeze down, and just use your fingers, and just...
DAVID POGUE: Wow.
What percent of this milk is spider-silk stuff?
RANDY LEWIS: For most of these, it's relatively low, so we're talking about... um... maybe one to two percent.
DAVID POGUE: Gives two percent milk a whole new meaning.
Randy Lewis: That's right, two percent, um yeah. We'd love, we'd love to see 10 percent, but we'll take two percent, at this point in time.
DAVID POGUE: Next begins the painstaking process of coaxing the silk protein out of the milk.
Randy Lewis: So we take the milk that we collected out at the farm, we pump that onto this column, which has a whole bunch of very small tubes in it.
DAVID POGUE: Right.
Randy Lewis: Tubes have holes in it, so that the spider silk protein and the milk proteins come out of the tubes, and it keeps the fat inside.
DAVID POGUE: So what's left is basically goat skim milk?
Randy Lewis: Exactly.
DAVID POGUE: Eventually, Randy comes away with a vial of highly concentrated silk protein.
How much milk went into making this tiny drop of solution?
RANDY LEWIS: Um, from our best goats that would be about a quart of milk.
DAVID POGUE: Wow. And then, what...how much silk can you get out of this?
Randy Lewis: We can get at least two to three meters.
DAVID POGUE: Wow! Alright let's have a look.
The final step is the most delicate. Randy's team takes the protein liquid and slowly injects it into an alcohol bath, which causes the liquid protein to solidify into a strand of actual spider silk.
So this is it? So this is your manmade spider silk?
Randy Lewis: This is manmade spider silk.
DAVID POGUE: Now, to prove its mettle, Randy loads the strand into a machine that measures tensile strength.
Randy Lewis: Look, you can start to see it moving.
DAVID POGUE: It is, it's straightening out.
The silk stretches as it resists being pulled until...
It just broke. I'm sorry, Randy.
Randy Lewis: It just broke.
DAVID POGUE: But there's nothing to be sorry about. A computer measures the force it takes to break the sample, telling them its tensile strength. Remember, the tensile strength of steel, its resistance to being pulled, is what kept my plane from plunging into the ocean.
The tensile strength of spider silk appears to be greater than steel or even Kevlar. Not as strong as carbon nanotubes, but more flexible, easier to make in long strands, and certainly not toxic.
Randy Lewis: We are stronger than Kevlar, we're stronger than steel, but we're not stronger than the natural silk.
DAVID POGUE: The spider silk protein demonstrates nature's ingenuity. Its ingenious structure is comprised of three distinct sections.
Randy compares one of those sections to children's building blocks.
Randy Lewis: If you look at a molecular model, what you see is that they have little pins and little holes, just like LEGOs. So if you take and put them together and stack them up, like this, and try to pull them apart...
DAVID POGUE: These are, these are the proteins here?
RANDY LEWIS: These are the proteins. And that's part of the protein we try to pull apart. It doesn't pull apart.
DAVID POGUE: Okay, so if I'm pulling this way and this way, and this is the dragline, and it's not coming apart...
Randy Lewis: Yeah, that's right. So that's one part of the dragline.
DAVID POGUE: Proteins: good for you. Okay.
Randy Lewis: So four hundred million years, spiders've been playing with LEGOs.
DAVID POGUE: The second section of the protein is stretchy.
Randy Lewis: For elasticity, they have something that literally looks like a molecular spring. When you pull on the ends...
DAVID POGUE: Right.
RANDY LEWIS: ...it stretches.
DAVID POGUE: Okay, so...
Randy Lewis: And, and, and that the elasticity...
DAVID POGUE: This would be a different protein?
RANDY LEWIS: No, it's the same protein. It has different parts.
DAVID POGUE: Okay.
Randy Lewis: So we have, in the same protein, we have LEGOs, ...
DAVID POGUE: Right.
Randy Lewis: ...we have springs,...
DAVID POGUE: Okay.
Randy Lewis: And then, in order to put them together, we have zippers.
Zippers hold things together very well, but they have some flexibility, so you have a way of being able to put this together. With a spring, might be too tight to do that, so you put a zipper in between: now you have dragline silk.
DAVID POGUE: These basic building blocks repeat over and over again, trillions of them in each strand of silk.
The complex structure is evolution's way of enhancing the strength of the common raw materials found everywhere in nature.
Before I leave, Randy suggests one last experiment for us would-be Spidermen.
You getting anything?
RANDY LEWIS: I don't feel a thing.
DAVID POGUE: Nothing.
So it seems that the next chapter in the story of strong materials is already upon us.
For thousands of years, we've experimented with our planet's raw materials to make metals and ceramics. Then, through chemistry, we created synthetics and built materials atom by atom. Now scientists are learning to combine the engineering tricks found in the living world with the incredible strength of our own inventions. With these new tools and materials, there's no telling what we'll be able to accomplish, once again propelling human civilization across a new frontier, as has happened again and again, over millennia, every time we learn more about making stuff stronger.
Broadcast Credits
Making Stuff: Stronger
- Host
- David Pogue
- Written, Produced and Directed by
- Chris Schmidt
- Executive Producers
- for Powderhouse Productions
- Joel Olicker
Tug Yourgrau - Co-Producer
- Alexandra McHale
- Field Producer
- Doug Gordon
- Edited by
- Brian Cassin
- Additional Editing
- Justin Vaida
Daniel McCabe
Kristine Gaffney - Director of Photography
- Gary Henoch
- Additional Photography
- Joe Livolsi
Jason Longo
Mike Marshall
Joe Friedman
Tom Kaufman - Sound Recordists
- Glen Ackers
Mark Arees
Lyle Bibler
Jeff Boedeker
Mike Boyle
Kabe Cornell
Gregg Hinnen
Mike Italiano
Dave Manahan
Bill Wander
Warren Wolfe - Grips and Gaffers
- Ken Perham
Greg Price
Grady Smith
Darrell Tawney
Josh Weinhaus - Production Assistant
- Daniel V. Parsons
- Music
- Lunch Special Music
- Animation
- Edgeworx, LLC
- Additional Animation
- Wlan Waldo
Jenny Olson - Production Manager
- Diane Knox
- Post Production Supervisor
- Kevin Young
Michael Fallon - Assistant Editors
- Eric P. Gulliver
Peter Hyzak
Bryce Patingre - Assistant Online Editor
- Erin Gallagher
- Online Editor / Colorist
- Julie Kahn
- Audio Mix
- Heart Punch Studio, Inc
- Research
- Sonia Weinhaus
- For Powderhouse Productions
- Post Production Manager
- Melissa Walter Richards
- Senior Production Coordinator
- Carlin Corrigan
- VP of Production
- Daniel Miller
- Senior VP of Production and Post
- Robert Kirwan
- Archival Material
- AP Archive
Getty Images
Footage courtesy of Discovery FootageSource
Footage Courtesy MIT Museum
Footage Provided by Thought Equity Motion
iStockphoto
Palmpress, Inc. - Special Thanks
- Producers gratefully acknowledge the cooperation of the Materials Research Society.
- Richard A. Souza
Amy Moll
Kristin Bennett
Jerry Floro
Megan Frary
Kevin Jones
Tommie Kelley
Alex King
Aditi Risbud
Stephen Streiffer
Rick Vinci
Sandra DeVincent Wolf - Special Thanks
- American Museum of Natural History in New York City
United States Navy
Otis Elevator Company
Professor Stephen Sass, Cornell University - NOVA Series Graphics
- yU + co.
- NOVA Theme Music
- Walter Werzowa
John Luker
Musikvergnuegen, Inc. - Additional NOVA Theme Music
- Ray Loring
Rob Morsberger - Post Production Online Editor
- Michael H. Amundson
- Closed Captioning
- The Caption Center
- Publicity
- Eileen Campion
Victoria Louie
Karen Laverty - Marketing
- Steve Sears
- Researcher
- Kate Becker
- NOVA Administrator
- Kristen Sommerhalter
- Production Coordinator
- Linda Callahan
- Paralegal
- Sarah Erlandson
- Talent Relations
- Scott Kardel, Esq.
Janice Flood - Legal Counsel
- Susan Rosen
- Post Production Assistant
- Darcy Forlenza
- Associate Producer Post Production
- Patrick Carey
- Post Production Supervisor
- Regina O'Toole
- Post Production Editor
- Rebecca Nieto
- Post Production Manager
- Nathan Gunner
- Compliance Manager
- Linzy Emery
- Development Producer
- Pamela Rosenstein
- Supervising Producer
- Stephen Sweigart
- Business and Production Manager
- Jonathan Loewald
- Senior Producer and Project Director, Margret & Hans Rey / Curious George Producer
- Lisa Mirowitz
- Coordinating Producer
- Laurie Cahalane
- Senior Science Editor
- Evan Hadingham
- Senior Series Producer
- Melanie Wallace
- Executive Producer
- Howard Swartz
- Managing Director
- Alan Ritsko
- Senior Executive Producer
- Paula S. Apsell
Produced by Powderhouse Productions
A NOVA Production by Powderhouse Productions for WGBH
© 2011 WGBH Educational Foundation
All rights reserved
Image
- (David Pogue)
- ©WGBH/Mark Ostow, ©iStockphoto.com/OGphoto
Participants
- C Lewis Azad
- NanoTech Institute, UTD
- Jim Bales
- Edgerton Center, MIT
- Ray Baughman
- The University of Texas at Dallas www.nanotech.utdallas.edu/personnel/staff/baughman.html
- Mark Eberhart
- Author, Why Things Break
- Joan Embery
- Embery Wildlife Conservation
- Nicholas Godley
- Fashion Designer
- Randy Lewis
- Molecular Biologist, UW
- Marcio Dias Lima
- NanoTech Institute, UTD
- Mark Meyers
- Materials Scientist, UCSD
- Tucker Norton
- Ballistics Scientist
- John Paules
- GM, Ellwood Technologies
- Scot Vannorman
- United States Navy
- Danny Womack
- Owner, Outlaw Motor Speedway
Education and Outreach Resources
Preview
Notice: Undefined index: preview_video_length in /home/nova/zend/application/templates/resources/multi-ep-pro.phtml on line 497
Full Program | 53:54
Full program available for streaming through ...
Watch Online
Full program available
Soon
Making Stuff: Smaller
Future technologies will depend on tiny stuff—from silicon chips to micro-robots that probe the human body. Airing August 21, 2013 at 9 pm on PBS Aired August 21, 2013 on PBS
- Originally aired 01.26.11
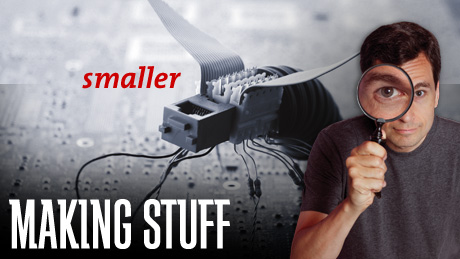
Program Description
Transcript
Making Stuff: Smaller
PBS Airdate: January 26, 2011
DAVID POGUE: Imagine a world with buildings that can ride out earthquakes; bacteria that make gasoline; tiny devices that can repair individual cells, or even D.N.A.; gossamer threads, strong enough to hold up a bridge; or an elevator to the stars. These visions of the future are based in the discoveries of today, as a new science of materials emerges from the elemental building blocks of the universe, promising a future in which we can create virtually anything we want, atom by atom.
I'm David Pogue, and I'm on a quest to discover how the world's smallest materials are changing our lives: swarms of nano-machines that combat cancer on the cellular level with bee venom;...
Bee venom is a cancer drug?
Samuel Wickline (Cardiologist, Washington University): Yeah, it's an excellent cancer drug.
DAVID POGUE: ...computer chips, one-atom-thick and up to a thousand times faster than silicon chips today;...
Come on; now you're hurting my brain.
Daniel S. Mishkin (Gastroenterologist, Boston University): This capsule is acquiring images at a rate of two frames per second.
DAVID POGUE: ...and high definition cameras, an inch long, monitoring our bodies from within.
Oh man, I think I just banged the top of the eyeball.
How far can we go...
What? That's a robot?
Bradley Nelson (Institute of Robotics, ETH Zurich): That's a robot.
DAVID POGUE: ...in Making Stuff Smaller? Right now, on Nova.
As tech columnist for the New York Times, I'm always on the hunt for the next killer gadget.
Wow, so I can play my records straight into the iPhone?
Adam Cohen (Consumer Electronics Show participant): That's right.
DAVID POGUE: That's very cool.
Each year, my beat brings me to the Consumer Electronics Show, in Las Vegas, to investigate the latest trends in new tech.
Summer Douglass (Consumer Electronics Show participant): It's a watch that is also a cellular phone, an Mp3 player, a camera, a video camera.
DAVID POGUE: Somehow, the electronics world has found that the key to making stuff better is making it smaller.
David Albers (Consumer Electronics Show participant): So, that's the new flagship L.E.D.
DAVID POGUE: Wow.
Take the T.V. Ten years ago, the first flat screens cost as much as $12,000. They had thick glass panels and weighed a whopping 85 pounds, but now?
DAVID ALBERS: This T.V. is point-three inches deep.
DAVID POGUE: Are you kidding? So, the nice thing is when they FedEx it to you, they can just slip it under the door?
DAVID ALBERS: Exactly.
DAVID POGUE: I'm on a quest to discover why size matters, why getting smaller leads to such gigantic benefits.
Amy Koppman (Consumer Electronics Show participant): Performance on it is phenomenal in the light. You have an f2.8 lens, 24-millimeter wide. It's just a great piece.
DAVID POGUE: It's crazy. If everything we own had improved over the last 25 years as much as electronics have, the average family car would travel four times faster than the space shuttle; houses would cost 200 bucks. What's the secret behind electronics stunning advances?
How many times have I reviewed these and wondered exactly what's inside there?
Do you mind if I have a look?
AMY KOPPMAN: No, not at all. Go ahead.
DAVID POGUE: I'd like to have a look inside.
AMY KOPPMAN: Yeah, please do.
DAVID POGUE: Where I come from, you want to know how something works, you cut it open. Sony versus saw; here we go.
You guys standing far enough back? Because I don't want anyone to get hurt. What do you think we'll find? Elves? Butterflies?
And now, let's see what really is on the inside of a digital camera. Not much really, and no moving parts at all! This digital camera...
AMY KOPPMAN: This is the brains.
DAVID POGUE: ...runs on a half-inch-wide microchip.
So it seems like this is really the heart of the camera. A lot of it just exists so that I can handle it with my big human hands.
AMY KOPPMAN: Correct, 'cause that's not exactly the most comfortable form factor you want to be using right there.
DAVID POGUE: I know.
Honey, smile. Come on, let me see you smile. Come on.
This tiny wafer contains a highly sophisticated machine. What's it made of?
A computer chip is like a densely packed city: a solid slab of silicon, sprinkled with other elements like boron and arsenic, topped by layers of metals and ceramics. They are laid out like tiny functional neighborhoods.
Over here is memory.
Fifty years ago, you'd have needed a whole building full of vacuum tubes to store just a fraction of what fits in here.
Over here is where data comes in and out of the chip.
Fifty years ago, the fastest computer on Earth could process, maybe, a few hundred punch cards a minute. Today, data goes in and out billions of times faster.
And here is the processor.
Fifty years ago, a computer could add a few thousand of numbers in a second. In the same amount of time, this tiny chip can perform billions of calculations.
Scientists have discovered that the secret to cheap computing power is size. When we find the right materials, and make them small, they change the world.
The race to miniaturize began 500 years ago, with an invention that, in its day, was the first personal computer. I'm talking about the watch.
How did they go from big wall-mounted grandfather clocks to something you could wear on your wrist?
Pierre Gygax (Chief Operating Officer, Ulysse Nardin): The miniaturization, more functions in a smaller space.
DAVID POGUE: Pierre Gygax is a watchmaker, in Switzerland. Some of his watches have more than 400 components.
And how small are some of the parts?
PIERRE GYGAX: There are parts, which are point-zero-zero-six millimeters. So that means a half the thickness of a hair.
DAVID POGUE: Wow. Hundreds of precision metal pieces all driven by a simple mechanism that all clocks have in one form or another: the oscillator, the beating heart of the machine. It's the piece that puts the tick and the tock in time.
PIERRE GYGAX: You know the time is flowing. And it's always difficult to measure something flowing. So, what we do is we, we cut the time in slices. And the oscillator is counting the slices.
DAVID POGUE: The original oscillator was the pendulum, slicing like a knife through time, with each swing counted by the movement of circular gears.
But pendulum clocks work only if they are upright in a fixed position. So, in the Middle Ages, clocks were confined to immovable structures like towers or furniture. But in the 15th century, the invention of the mainspring changed everything.
It was essentially the first battery, a metal coil that could store mechanical energy. As it unwound, the mainspring powered a compact wheel. It was a major breakthrough. Suddenly, gravity and the pendulum were no longer necessary.
The new spring-driven mechanism made it possible to shrink the clock to fit into a hand or a pocket, and the pocket watch was born.
PIERRE GYGAX: This watch is absolutely amazing. It shows the exact position of the sun and the moon, all around the earth, from the top of the North Pole.
DAVID POGUE: Oh, man, that's really cool. And how much does this watch go for?
PIERRE GYGAX: Between $80- and $90,000.
DAVID POGUE: But no need to spend 90 grand to find out what time it is. Nowadays, super accurate watches are disposable, thanks to another great clock revolution, which began in the 1960s.
Out went the spring and mechanical oscillator, replaced by a tiny sliver of solid mineral quartz.
Slice a piece of quartz small enough, send an electric current through it, and it vibrates fast. A quartz-driven clock can accurately chop time into millionths of a second, but the biggest selling point for quartz is that it's cheap.
That's because quartz is actually silicon, commonplace sand, the second most abundant element on Earth.
For the first time, a material replaced a machine, opening the door to a new era of miniaturization. But silicon can do more than just mark time. It's a member of a strange class of elements called semiconductors, found on the table of the elements.
As the name implies, they occupy a middle zone between metals, which conduct electric current, and insulators, like rubber and plastic, which don't.
Think of water flowing through a pipe, an insulator is like a pipe that's frozen: electrons can't get through. Semiconductors are materials that change from free-flowing conductor to a frozen insulator and back again, simply by zapping them with an electric current.
Switches made out of semiconductors are called transistors, and their amazing on-again, off-again switching ability made the computer revolution possible.
But how did they get to be so small?
One great place to look for answers is Intel, a pioneer in squeezing tiny transistors onto computer chips.
I've met a lot of scientists who talk about switches and semiconductors, and somehow they are fulfilling the same function, but, but what is it?
Stephen L. Smith (Vice President, Intel Corporation): What we're trying to build with a semiconductor is a switch. This is one from the, the wall, something you'd use to turn on a light and turn off. And, in fact, when we push the switch up, we give an input and the light is an output.
DAVID POGUE: So, in science fair terms, a switch then, lets electricity go through or stops it.
Stephen Smith: Exactly. Based on the input, we change the flow of electricity.
DAVID POGUE: Electricity on or off. It's the only language computers understand. When the switch is off, the computer reads a zero. When the switch is on, the computer reads a one. String a bunch of switches together and you can create a code. With just eight switches, you can represent any symbol on a keyboard. For a page, you need about 25,000 switches. One-point-four million will get you a second of music. Photos need tens of millions. And videos? We're talking about tens of billions. The more switches, the more power.
The story of the computer revolution is the story of the shrinking switch. Early computers used mechanical relays and vacuum tubes as switches. Building a machine with just a few thousand took up rooms of space. But the silicon transistor changed all that. Because it's a material, not a machine, it's easy to shrink.
STEPHEN SMITH: The exciting part about silicon transistors is we're actually using the atomic properties of the silicon. So rather than actually having to craft something, to build a switch, to build the pieces, to build a spring, I actually, by doing some smart engineering, can get the electrons to flow by using the properties of the atom. And we brought some material to illustrate that. What we have here...
DAVID POGUE: We happen to have a hunk of cheese lying around the lab?
STEPHEN SMITH: A hunk of cheese, a hunk of cheese.
So think of this as the silicon material. I can actually take a slice of that silicon, and I can use the atomic properties of this slice to build those transistors.
DAVID POGUE: Ladies and gentlemen, the Pentium-cheesium-five. Um, I understand that it works really well with the computer mouse. (You can use that.)
All right, so you're saying that one beauty of silicon is that you can cut it in half and it's still silicon?
STEPHEN SMITH: Exactly.
DAVID POGUE: And you can slice it again, smaller and smaller and smaller, but it still does just as good a job at passing along the ones and zeros.
STEPHEN SMITH: Absolutely. And I can use those material properties until I get down to the size of only a few atoms of silicon.
DAVID POGUE: Wow. Which is not something you could do to make mechanical switches smaller, right? Like, if I wanted to make this smaller, you know, I can't just go like this.
STEPHEN SMITH: Wow!
DAVID POGUE: And you can have a smaller one. Clearly, this is not going to be a smaller, good switch.
STEPHEN SMITH: Right.
Uh, but this is silicon. It is a purified element that one mines.
DAVID POGUE: All right, so what does it look like in the computer, then?
STEPHEN SMITH: Well, by the time it gets to the computer, it actually is one of these devices. So, this shiny surface is a piece of refined silicon. It has transistors built into it. We've actually flipped it over so that the transistors are on the other side, and what you see is the back of that piece of silicon.
DAVID POGUE: And this is how many of those little on-off switches?
STEPHEN SMITH: This is almost a billion transistors.
DAVID POGUE: Wow. A billion switches on a one-inch chip.
What's even more astonishing is that one of the founders of Intel saw this coming. In the '60s, Gordon Moore predicted that the size of transistors would shrink by half every two years, each time, doubling the number that could be squeezed onto a single chip.
This idea is known as Moore's Law, and it has proved to be incredibly accurate. But now, 50 years later, Moore's Law may finally be running out of steam. The transistors that power our stuff are about as small as they can get, unless scientists can come up with a new way of packing them ever-more tightly together.
To see one of those possible solutions, I've crossed the country to visit the IBM Research and Development..."kitchen?"
So this is Moore's Law of Italian cooking?
Frances Ross (IBM Research Division): That's right. What we're going to do is explain why it's so important to get the transistors smaller and smaller.
DAVID POGUE: Frances has a pretty appetizing way of visualizing this law and its limitations. Like pepperoni slices, the transistors on a silicon chip are flat.
Okay, so here's our...
Frances Ross: Silicon wafer.
DAVID POGUE: ...silicon wafer.
Frances Ross: Now, these are the old-fashioned transistors. They're much larger, and you can see that you can't put that many onto each wafer.
DAVID POGUE: So this would be a 1960 iPod?
Frances Ross: I think so, yes. This would be a '60s type of thing.
So, let's take off these old transistors and replace them with some new transistors.
DAVID POGUE: Oh, these are much smaller!
Frances Ross: Yes, these new transistors are much smaller.
DAVID POGUE: Technology has marched on.
Frances Ross: That's right. It's Moore's Law, in action.
DAVID POGUE: So, in other words, all we have to do is make the transistors smaller every year, forever, and our gadgets will always be more powerful and more compact.
Frances Ross: That would be wonderful, but we can't make our pepperoni slices much smaller than this. And these transistors are now packed together about as close as we can get them.
DAVID POGUE: The pizza party can't go on forever. There's a limit to how small you can shrink the transistors. If you reduce the surface area of a transistor too much and place it too close to its neighbor, electricity starts to leak, causing a short circuit. Not good.
Frances Ross: We've run out of area, so there's only one way to go, and that's upwards.
DAVID POGUE: Slim Jims?
Frances Ross: That's right. This is a vertical transistor. Instead of having flatter, smaller transistors we go in the other direction.
DAVID POGUE: Excuse me, vertical transistors?
Frances Ross: Vertical transistors.
DAVID POGUE: With little toothpicks on the bottom?
Frances Ross: That's just for demonstration purposes.
DAVID POGUE: Oh, okay.
By building vertical transistors, called nanowires, Frances can increase surface area, without bringing the transistors closer together, so no short circuit.
Ingenious. So this is what you're doing at IBM? You are making these?
FRANCES ROSS: That's right. They're called nanowires, and the real thing is about a million times smaller than this.
DAVID POGUE: A million times smaller?
FRANCES ROSS: That's right.
DAVID POGUE: Well, that would be hard to see!
They're hard to see. But this is not a nanowire. This is a silicon sliver Francis uses as a surface to grow them.
FRANCES ROSS: We get tens of millions of wires on each of these specimens.
DAVID POGUE: Come on!
FRANCES ROSS: Yes.
DAVID POGUE: Now you're hurting my brain.
FRANCES ROSS: Oh.
DAVID POGUE: She carefully loads the wafer into a molybdenum clip and slides it into a custom-built oven, where she'll bake it at 1,100 degrees Fahrenheit.
You know, I was just thinking, Frances. I don't think you have enough aluminum foil on this oven.
FRANCES ROSS: Yes, it's the question that everyone asks. It holds the heat better.
DAVID POGUE: Aluminum foil?
FRANCES ROSS: That's what, that's what we use.
DAVID POGUE: Isn't that a little low tech?
FRANCES ROSS: That's right; whatever works.
DAVID POGUE: Oh, my gosh. So those little spires...?
FRANCES ROSS: Those are the nanowires.
DAVID POGUE: So, you bake those up?
FRANCES ROSS: Just grew these, yes.
DAVID POGUE: We can see them, because this oven doubles as an electron microscope.
All right, so these are them, huh?
FRANCES ROSS: This is 30,000 times magnified.
DAVID POGUE: Thirty-thousand times?
FRANCES ROSS: That's right. So here's the column of silicon that's the nanowire, and here's the gold droplet, on the end, that actually makes it grow.
DAVID POGUE: It's weird. It looks like matchsticks or weird mushrooms.
FRANCES ROSS: They do...mushrooms, that's right. They look to me like mushrooms.
DAVID POGUE: That's amazing.
FRANCES ROSS: So we're trying different catalysts, different recipes, but this here is the future of transistors
DAVID POGUE: Wow.
While scientists like Frances try to find ways to push silicon to its limit, others are pinning their hopes on a new material that lets electrons flow a thousand times faster than they can in silicon. And it's called "graphene."
Pablo Jarillo-Herrero (Physicist, Massachusetts Institute of Technology): When graphene happened, I just couldn't stop myself from going into it. It was so beautiful, I just couldn't stop. I immediately jumped onto it.
DAVID POGUE: This is Dr. Pablo Jarillo-Herrero, a professor at M.I.T. and graphene guru.
PABLO JARILLO-HERRERO: So, here I have graphene. Graphene is the thinnest material that exists. This is just one-atom-thick, okay, sheet of graphene and you can see that it is perfectly visible. So, it's part of the magic of graphene. You can just see it, even with your eyes.
DAVID POGUE: You heard that right. This grey square of graphene is just a single atom thick. Although graphene was discovered only recently, it's been hiding in plain sight for ages, in a material you probably have on your desk: graphite, also known as pencil lead.
PABLO JARILLO-HERRERO: You can write with a pencil because graphite is a layered material. And as you write, you are leaving traces of these layers on your piece of paper. So graphene is really just one sheet of this graphite material, a one-atom-thick sheet.
DAVID POGUE: That makes graphene an ideal conductor. At only one atom thick, there's nothing to restrict free electrons, which flow across the surface of the material, like water across flat ice.
PABLO JARILLO-HERRERO: Graphene is a very special conductor...is the best conductor, and we're now studying those properties and learning how fantastic this material is.
DAVID POGUE: And scientists have also figured out how to make transistors out of graphene, giving it the ability to speak the language that electronics and computers understand.
PABLO JARILLO-HERRERO: So, I'm excited. It's beautiful. Here you have a material that will enable high-speed, ultra-high-speed electronics at very low power.
DAVID POGUE: But it gets even better. Turns out, the only tool you need to make graphene is a piece of tape.
PABLO JARILLO-HERRERO: It is so simple, any high school student can indeed make one atom-thick devices with this. It's really amazing. That scotch tape is going to be folded into two, and then, when we separate that tape, this graphite naturally exfoliates in two pieces. Then we're going to fold it again. It will split into four pieces. Then eight. Do it again and again, making the piece of graphite thinner and thinner and thinner. Basically until we cover the entire tape with graphite.
We're then going to take a silicon chip, deposit it on top of the tape. And what we're hoping is that the graphite pieces which are on the tape are going to get in intimate contact with the silicon. So when you remove the chip and you look then with an optical microscope, you can see the one-atom-thick material. And that's graphene.
DAVID POGUE: Graphene promises to make the impossible possible, letting electrons move across its surface at virtually the speed of light and generating almost no heat. In fact, graphene is such a revolutionary material that in 2010, a mere six years after its discovery, the two Russian scientists who first made it received the Nobel Prize in Physics.
The computer chips of tomorrow could be a quantum leap forward: computers with nearly limitless processing power; every book ever written, stored on a tiny chip; a highway system so smart it could control millions of cars without a single accident. And it's not just about our gadgets, it's about us.
While the electronics story continues to unfold in amazing ways, the story is beginning all over again with a materials revolution in medicine.
It's not a new idea. Remember this?
Audio Clip (Fantastic Voyage, Film Clip) Phase One calls for miniaturizing a submarine and injecting it into the carotid artery.
DAVID POGUE: Fantastic Voyage, it was the sci-fi smash of 1966.
Audio Clip (Fantastic Voyage): Phase One, Phase One.
DAVID POGUE: Scientists shrink a team of doctors and send them into a sick man's body, on a mission to cure him.
Audio Clip (Fantastic Voyage): Stand by for injection. All stations stand by. Tracking post. Inject.
DAVID POGUE: Today, as our devices get smaller and smaller, Fantastic Voyage is beginning to look like prophecy, the kind of thing that can change lives.
DANIEL MISHKIN: Hi, Courtney.
Courtney DeSisto (Patient): Hi, Dr. Mishkin. How are you?
DANIEL MISHKIN: Good and yourself?
COURTNEY DESISTO: I am good. Thank you.
DAVID POGUE: Today, Courtney will be taking a pill, but it's not just any pill. It's a miniaturized camera.
DANIEL MISHKIN: This capsule is a miniaturized camera. Every time it blinks it's actually taking a picture. It's acquiring images at a rate of two-frames per second.
COURTNEY DESISTO: Okay.
DANIEL MISHKIN: And what I'm going to get you to do is actually to swallow the capsule.
COURTNEY DESISTO: Okay.
DANIEL MISHKIN: And as the capsule goes through the G.I. tract it's going to be taking pictures of what's going on inside.
COURTNEY DESISTO: Wow.
DAVID POGUE: It's called the PillCam, and it travels through the body just like a piece of food, taking 55,000 pictures, over the course of eight hours.
DANIEL MISHKIN: Why don't we actually put it inside your hand?
DAVID POGUE: Pictures that can provide a diagnosis that once would have required surgery.
DANIEL MISHKIN: All right, so as you move it around, we can actually see the folds of your hands, with excellent magnification. So once we actually go ahead and ingest the capsule, it's going to give us that same magnification of what's going on inside.
COURTNEY DESISTO: Wow, that's really cool.
DANIEL MISHKIN: It actually has a wireless transmitter, that's going to transmit the images to the data recorder that you'll be wearing over the course of the day, and I'm going to download the images and be able to look at them and analyze exactly what's going on.
COURTNEY DESISTO: Okay.
DAVID POGUE: The PillCam is made of an inert plastic that doesn't create a toxic response in the body. Inside, is a mini-catalog of the electronics industry: a tiny video camera and flash, a radio transmitter, a battery, and, of course, a computer chip to drive it all. Twenty-five years ago, all of those components would have taken up a cubic yard of space. Today, it all fits inside a one-inch capsule that weighs only a fraction of an ounce.
DANIEL MISHKIN: So let's go ahead and ingest it.
COURTNEY DESISTO: Okay.
DANIEL MISHKIN: Ready? Into your mouth. I'll give you a glass of water. Now I see your teeth. And, go ahead, down the hatch. Okay, great. So that's it. That's the hardest part.
COURTNEY DESISTO: Okay.
DANIEL MISHKIN: Just remember, over the next two hours, do not drink anything.
COURTNEY DESISTO: Okay.
DAVID POGUE: As the PillCam moves through Courtney's digestive tract, it records what it sees, eventually giving Dr. Mishkin a front-row seat as he looks for abnormalities.
DANIEL MISHKIN: Right now, we're looking at the small intestine. It's able to see 360 degrees, such that it's like looking down a gun barrel.
The capsule is great at acquiring images, but I'm hoping that as the next generations of the, this capsule develop that it's not only be able to take pictures, but it will eventually be able to biopsy—sample the tissue in that area—or even deliver a treatment, such as placing a clip on a bleeding site, or even deliver medications.
DAVID POGUE: The PillCam is the pocket watch of today, a super-miniaturized machine that liberates the patient. It took centuries to make the leap from mechanical watches to computers, but in the world of microscopic medicine, the story of smaller is unfolding on a vastly accelerated timeframe.
In fact, scientists are on the verge of realizing a 21st century version of the Fantastic Voyage story. They are developing microscopically small robots that travel into the body's deepest reaches to diagnose, treat, and even destroy deadly illnesses.
This is your lab?
BRAD NELSON: This is my lab.
DAVID POGUE: This is where you build your robots?
BRAD NELSON: This is where we build the robots.
DAVID POGUE: This is Brad Nelson. He's created a robot that could help cure blindness.
Oh, nice, it's incredibly lifelike.
BRAD NELSON: Yeah, that's a mannequin.
DAVID POGUE: Oh, sorry.
BRAD NELSON: These are the ones we build.
DAVID POGUE: What? That's a robot?
BRAD NELSON: That's a robot.
DAVID POGUE: Looks like a splinter.
BRAD NELSON: Well, this is a microrobot. We use them to help perform surgeries on the eye or inside of the eye.
DAVID POGUE: The device is only a hundredth of an inch wide, small enough to fit into the needle of a syringe, like the tiny sub in Fantastic Voyage. But the similarity ends there.
This unmanned device is designed to treat a type of blindness caused by blocked blood vessels in the retina, the tissue where images are formed. The robot delivers an extremely small dose of medicine to restore blood flow and vision.
That makes me think that this little tiny thing has batteries and little propellers and some kind of knowledge to know where to go in the eye. I have a hard time believing that.
BRAD NELSON: That's right. The way we energize is we use externally generated electromagnetic fields. So, basically, it's a magnet.
DAVID POGUE: To make the device small enough, Brad had to abandon the idea that robots have to be mechanical. Instead, he focused on finding a material that would let him eliminate bulky moving parts.
He chose two elements, samarium and cobalt. Combined, they form a material highly sensitive to magnetic fields, which means that Brad can direct the movement of the robot without touching it.
Once again, a material replaces a machine and the device gets smaller.
BRAD NELSON: So then, besides just the robot, what we also have is this system here, of electromagnets, and so what each of these copper coils do, is they generate magnetic fields.
DAVID POGUE: Oh, man. Yeah, you got a bunch of them in every direction.
BRAD NELSON: So we have eight of these here. That's why we call this the OctoMag.
DAVID POGUE: OctoMag?
BRAD NELSON: That's right.
DAVID POGUE: The OctoMag. By adjusting the strength of these eight electromagnets, the surgeon can move the microrobot any direction along the x, y and z-axes, pushing or pulling it through the eye. But landing it on the tiny section of retina used for seeing in sharp detail takes lots of practice.
And you've been practicing with dummy eyeballs, so far?
BRAD NELSON: We use that, but we also use animal eyes as well. We get pigs eyes from our local butcher.
DAVID POGUE: You buy eyeballs from the butcher, from cadavers?
BRAD NELSON: That's right, Christos, one of my PH.D. students...Christos goes in the morning, early in the morning, to the butcher and asks for eyeballs.
DAVID POGUE: Christos. How are you?
Christos Bergeles (Student, Institute of Robotics, ETH Zurich): Fine.
DAVID POGUE: Oh, my. These are the pig eyes?
Christos Bergeles: Exactly. Twenty pig eyes fresh from the butcher, ready to be prepared for experiments.
DAVID POGUE: You must be a big hit around Halloween.
And what about this guy, what's this all about?
Christos Bergeles: Ah, we call him Mr. Pig Eye Guy.
DAVID POGUE: Mr. Pig Eye Guy?
Christos Bergeles: Well, you have to give them a name. Then we put the eyes in this hole here.
DAVID POGUE: Once the eyeball is secured inside the socket, we insert a light probe.
Christos Bergeles: That's the light there.
DAVID POGUE: Oh, okay. I can actually see the light in there, very cool.
This tiny L.E.D. lets us see what we're doing when we drive the robot.
So, this is the robot right here?
Christos Bergeles: Mm hmm.
DAVID POGUE: Okay. And this isn't fake? We're really seeing this live from the microscope, right now, right?
Christos Bergeles: Yes. Right now. You can move this guy around.
DAVID POGUE: Okay. Sure enough, I push right, he goes right; left, he goes left. Let's see when I go down over here.
Christos Bergeles: And then you can pull up and you can see it.
DAVID POGUE: Oh, it's getting bigger.
Christos Bergeles: Exactly. This means that it's moving higher, away from the retina.
DAVID POGUE: Closer to the surface of, oh man! I think I just banged the top of the cornea or whatever you call it.
Christos Bergeles: Exactly. So that's the very top, and this is where the liquid ends. So you see this, this effect.
DAVID POGUE: Now let me push down.
Christos Bergeles: When you push down, it starts slowly going into the retina.
DAVID POGUE: It's sinking, sinking! Wow, that's really cool.
Christos Bergeles: So, now you've reached the bottom; you're touching the retina.
DAVID POGUE: Yeah, it's quite responsive. I can go right up here.
Eventually, Brad hopes that there will be a commercial version of his device installed in doctors' offices. The magnets will be arranged in a housing that surrounds the patient's head while the doctor peers through a microscope to guide the drug-filled robot.
Brad's initial success combining materials and magnetic fields to make tiny devices has encouraged him to be even more ambitious. His goal is to build a robot that can swim through blood vessels.
But, along the way, he's discovered that the smaller you go, the stranger the world becomes.
Oh, dear, looks like the grad students have left their things out again.
And the harder it is to get around.
BRAD NELSON: So what we've seen, so far, are the microrobots for the eye. We're interested in going even smaller and trying to make smaller robots. So I set up an experiment here to, kind of, show you what some of the problems are when we try to make small things swim, and why it's so different from how big things, like fish or the toys like this, swim in water.
DAVID POGUE: Okay.
BRAD NELSON: So what we've got here are two tanks. One is just regular water, out of the tap. This other one is glycerin. It's much thicker, like oil or corn syrup, something thick like that. So let's look at how something like this toy goldfish is going to swim in water.
DAVID POGUE: Wind her up?
BRAD NELSON: Wind her up. There you go.
DAVID POGUE: Okay, the tail goes back and forth.
BRAD NELSON: Just the way you expect.
DAVID POGUE: I'd say that swimming is fairly effective.
BRAD NELSON: Okay, he's got a twin over there. Let's see how he does in the glycerin.
DAVID POGUE: And this one is going to go in the goop. He wags his tail and doesn't move at all.
BRAD NELSON: This helps us illustrate how water feels when you get small. If you made yourself 10,000 times smaller and you jumped in this pool of water, it would actually feel more like you were swimming in glycerin here, or goopy stuff, like honey, or something thick like that.
DAVID POGUE: Right. A swimmer the size of a bacterium would never be able to get around using flippers or the breaststroke, because, at that size, the friction from the water molecules becomes a major drag.
For a long time, scientists couldn't figure out how bacteria were able to swim, but, eventually, they discovered the secret. The tail, or flagellum, seems to move back and forth, but viewed from another angle, it's clear that it moves in a totally different way.
Corkscrew tail?
BRAD NELSON: A corkscrew tail.
DAVID POGUE: Brad and his team have developed corkscrew robots that mimic bacteria.
BRAD NELSON: Bacteria like E. coli and salmonella have developed these flagella that twist like...
DAVID POGUE: This part is the flagella?
BRAD NELSON: These flagella twists through the liquid, just like a corkscrew going into a bottle of wine. So instead of propelling itself or using its inertia, it's actually, kind of, cutting through the fluid.
DAVID POGUE: It's almost pulling itself, instead of pushing itself.
BRAD NELSON: It's pulling itself, in a sense, like a screw going into wood or something like that. It's a completely different material interaction.
DAVID POGUE: Very cool.
They use the same samarium-cobalt material and magnetic fields to set them in motion.
So, it's literally, like, drilling its way through that?
BRAD NELSON: Drilling its way up.
DAVID POGUE: Wow.
This is the biggest one. The smallest one is only 30 microns long. That's 30 millionths of a meter, about a third the width of a human hair.
BRAD NELSON: So, now, just in the last few years, we've been able to build small things, of a similar size and shape to real bacteria, that swim just like they do, potentially, deep inside a person's body.
DAVID POGUE: The magnet-driven robots in Brad's lab: the eye bot, the flagella bot, and even a soccer-playing robot that his students created, are each no bigger than a dust speck.
Brad's learned to modify his robots to overcome the physical obstacles in the microscopic realm, but he's only scratched the surface of the strange properties in that infinitesimal world.
Chad Mirkin (Chemist, Northwestern University): An atom is actually a fraction of a nanometer.
DAVID POGUE: Chad Mirkin is an explorer and pioneer in this weird realm: the nano world.
You keep saying you're building things on the nanometer scale. I don't even know what a nanometer is. So, this is a meter, this is a centimeter, this is a millimeter, is this a nanometer? What's a nanometer?
CHAD MIRKIN: Let me try to illustrate it for you. If we shrink you by a factor of two, you're about the size of a small child. We continue to shrink you by a factor of two, so, four more times, you're about the size of a golf ball. We go to ten, you're now the size of an ant. We keep going another seven times, and now you're about the diameter of a human hair. That's roughly what we can see with the naked eye.
DAVID POGUE: Even after so much shrinking, I'm not even close to the nano scale. Cut me in half five more times and I'm the size of a red blood cell. Five more times, I'm a virus. Seven more times, and I'm finally one nanometer in size, one billionth of a meter. That's less than half than the width of D.N.A.
It seems unimaginable that we might harness materials this small, but, in fact, it's not all that new.
CHAD MIRKIN: People have been using nanotechnology almost unknowingly for centuries. For example, back in the Middle Ages, when stained glass windows were made, they were using tiny little particles to get the beautiful colors. You simply need to go to Canterbury Cathedral and you can see the effects of nanotechnology in the beautiful glass windows.
DAVID POGUE: Canterbury Cathedral: some of the stained glass in here is nearly a thousand years old. With so much history under one roof, it's no surprise that the Cathedral needs a fulltime staff of glass preservationists.
So this is the paint station. This is like my local Home Depot, with different swatches, right?
Leonie Seliger (Head of Cathedral Studios): It's a little bit like that, yes.
DAVID POGUE: This is Leonie Seliger, the head restorer at the Cathedral.
I've come in search of ancient nanotech secrets.
LEONIE SELIGER: Um, what we're looking at here are stains. The stain gets fired. It's like pottery glaze; it's fused onto the surface of the glass.
DAVID POGUE: Okay.
LEONIE SELIGER: The trouble is that you don't just paint a yellow color on glass and you know how deep and how rich it is. You have to use a chemical process. So to make yellow, you mix silver with clay. Silver, under heat, actually produces a yellow glass.
DAVID POGUE: Wow!
She's using silver chloride, which in its natural form looks like small, silvery crystals. Leonie mixes a tiny amount with red clay.
LEONIE SELIGER: It's a silver salt that's mixed with this clay. You can't see it, what you see is the clay.
DAVID POGUE: Okay, okay.
LEONIE SELIGER: You would then paint that on. I've made a little series here, where I've now applied this clay, and after it's fired, if I then wipe that off...presto.
DAVID POGUE: Oh, look at that. From silver clay comes a golden color. There's some kind of voodoo chemistry going on there for sure.
LEONIE SELIGER: That's the mystery.
DAVID POGUE: Somehow this is nanotechnology at work. In the heating process, the silver crystals break down into tiny nanoparticles and turn yellow.
LEONIE SELIGER: But it only works on this glass.
DAVID POGUE: And that's not all. Leonie assures me there are several metals used in stained glass where nanotech creates surprising color results.
LEONIE SELIGER: Copper will give you...
DAVID POGUE: Brown?
LEONIE SELIGER: Or red.
DAVID POGUE: Red?
LEONIE SELIGER: Or green.
DAVID POGUE: That's just bizarre.
LEONIE SELIGER: Gold gives you beautiful rich pink glass, even rich ruby glass.
DAVID POGUE: And why is that? Why is something we think of as gold, why does it come out red?
LEONIE SELIGER: Ask a chemist.
DAVID POGUE: It's magic; it's religion.
LEONIE SELIGER: It is a bit. In the Middle Ages, of course, it was always a closely guarded secret on what makes what color at which temperature.
DAVID POGUE: When artists first learned how to change the colors of metals, it must have seemed like alchemy, but, in fact, it had something to do with changes at the smallest possible scale.
I want to get to the bottom of that mystery.
So this is your inventory here?
Mike Tuffey (Owner, English Antique Glass): This is our stock.
DAVID POGUE: So, I'm digging a little deeper at the English Antique Glass company, which makes the colored glass used to repair Canterbury's windows.
MIKE TUFFEY: There's cobalt blues.
DAVID POGUE: Wow. These sheets are crafted by hand, still using the same techniques that were developed in the 12th century.
How many establishments are there?
MIKE TUFFEY: Making this?
DAVID POGUE: Yeah.
MIKE TUFFEY: One. We're the only makers of flat glass, traditional methods, in the U.K. and Ireland.
DAVID POGUE: Wow.
This is Mike Tuffey, the head of production here. He and his team of glassblowers are able to achieve the same rich colors found in the cathedral, but they start with clear glass, which is made from a mix of sand, limestone, sodium carbonate and other minerals.
Oh, my gosh, that's it?
MIKE TUFFEY: That's it.
DAVID POGUE: That's the next great cathedral window right here?
MIKE TUFFEY: That's the next great cathedral window right there.
DAVID POGUE: It looks like kitty litter; it doesn't even look like glass.
MIKE TUFFEY: We just put that in the furnace. This is a rod we use for the different colors.
DAVID POGUE: The rods contain concentrated amounts of the metals that create color when added to the clear glass and fired at 1,200 degrees Fahrenheit.
So what does it look like when it comes out? Is it a sheet? Is it a blob?
MIKE TUFFEY: It's a blob.
DAVID POGUE: The journey from molten blob to colored glass is an intricate process of shaping, blowing and re-firing, resulting in a glass cylinder called a muff.
It's this heating and cooling process that creates the final color, thanks to the action of the metal nanoparticles.
You slit it, and then you have a flattening machine that uncurls it?
MIKE TUFFEY: That's right, that's it.
That's a gold, pink muff.
DAVID POGUE: There's gold dust in there?
MIKE TUFFEY: Yes.
DAVID POGUE: But it doesn't look gold, it looks pink.
MIKE TUFFEY: No, gold gives you pink.
DAVID POGUE: Gold gives you pink?
MIKE TUFFEY: Gold gives you pink.
DAVID POGUE: Why would that be?
MIKE TUFFEY: Ah, you would need to talk to a chemist on that one.
DAVID POGUE: I plan to do that.
Same answer. I'm 0-for-2 with the stained glass people.
So I went to Canterbury Cathedral, and I actually spoke to the guy who makes the glass, and the lady who does the repairs on those windows, and they said sure enough, they add gold to the glass to make it red. It doesn't make any sense, and you know what they told me? "We have no clue." But you're the scientis, man, you should, you should be able to explain why gold makes red.
CHAD MIRKIN: Well, it turns out that if you can control the size of a gold particle, if you can shrink it to this nanometer-length scale, you have completely different optical properties. Gold is no longer gold when taken to the 13-nanometer size, it's ruby red in color.
DAVID POGUE: When light rays hit a colored material, some colors are absorbed and some are reflected. That's why roses are red and violets are blue. Many metals, like gold and silver, reflect most of the colors in visible light, which is why they can be polished to shine like mirrors. But when a particle of gold is made very small, below 100 nanometers, 100 billionths of a meter, the particle begins to absorb shorter wavelengths of light, toward the blue end of the spectrum. The smaller the particle, the more blue is absorbed and the redder it appears.
But it gets even stranger, because not only size matters, shape does too.
Each of these vials contains water with silver nanoparticles dissolved in it. The only difference between them is the shape of the particles. In this test, silver rods give you yellow; silver triangles, green; silver prisms give you blue.
If metals behaved like this in our big world, then just changing the size or the shape of your car would alter its color.
Chad sees tremendous potential in this weird nano-phenomenon.
CHAD MIRKIN: With almost an infinite number of possibilities, you no longer have to take what nature gives you. You can adjust color simply by becoming a nano-architect.
DAVID POGUE: Scientists call this strange property of small materials "structural color." The living world figured this out millions of years ago. Structural color on the nano-scale creates the iridescent pigments in butterfly wings, beetle shells and peacock feathers.
Well, why do we care? I mean cool, little tiny gold particles are really red. I mean how does that help mankind?
CHAD MIRKIN: Well, the reason we care is that once you discover new properties, those new properties almost always lead to new applications.
DAVID POGUE: There are already a number of medical applications. Chad Mirkin has developed a technology that harnesses the unique properties of gold and silver nanoparticles to test the genetic variations in patients.
Sequencing D.N.A. is expensive and time-consuming, but Chad's revolutionary test takes less than two hours.
I offered to bleed for science, to see how it works.
Roy Pritchard (Technician): And your name is?
DAVID POGUE: David.
Roy Pritchard: Okay, so we're doing a low blood draw today. You can relax.
DAVID POGUE: Is this the extraction bench?
Tram Truong (Technician): Yes, this is.
DAVID POGUE: First, a technician extracts pure D.N.A. from my blood sample.
This is my DNA?
Chris Riley-Portugues (Technician): This is your D.N.A.
DAVID POGUE: He then loads it into a small, disposable cartridge and inserts it into the machine for testing.
This test can actually read the letters of my D.N.A. And, using gold nanoparticles, it flags variations that might make me unusually sensitive to particular drugs, or even mutations that signal heightened risk for disease.
Less than two hours after drawing my blood, the results are in. It turns out that the test has some interesting news for me about my sensitivity to a blood-thinning drug called warfarin, or Coumadin. It's commonly prescribed to stroke and cardiac patients.
It's a potentially lifesaving drug, but if the dosage is wrong, it can cause fatal bleeding.
So what's my warfarin dosage?
Jean Lopategui (Cedars-Sinai Medical Center, Molecular Pathology): What they call a double hit, I'm sorry to say.
DAVID POGUE: A double hit?
JEAN LOPATEGUI: You're a double hit, so you have two genes that are mutated, and therefore you're very sensitive to warfarin. Your calculated dose is 2.7 milligrams.
DAVID POGUE: See, I knew it! My mother always said it would be like 2.6 or 2.5, but I always said, "No, Mom, mine's 2.7."
JEAN LOPATEGUI: You should always listen to your mom, David.
DAVID POGUE: The nanosphere test gave me some crucial information...
Chris Riley-Portugues: This is the mutation.
DAVID POGUE: Ahh.
...quickly enough to save my life, if I'd been ill.
It's a diagnostic tool. The next goal is to fight illness in the body, at the same tiny scale.
SAM WICKLINE: Okay, so, when we inject this, it will go in the bloodstream and find the cancer. Like a rocket-guided system.
DAVID POGUE: Sam Wickline has invented a nano-device that's smaller than a virus. Engineered atom by atom, his hunter-killer robots are designed to travel by the billions in the bloodstream. They're pre-programmed, by a doctor, to seek out specific types of cancer cells and then destroy them. With none of the side effects associated with current drug therapies. It's the ultimate Fantastic Voyage dream. And it's borrowing a page from these little guys.
Wow.
TED JANSEN (Beekeeper): See, here, now.
DAVID POGUE: Whoa.
Ted Jansen: This is full of honey. See? There's probably 35 pounds of honey in there.
DAVID POGUE: Oh, my gosh.
TED JANSEN: In fact, I'll take it out and show you.
DAVID POGUE: He's brought me to meet beekeeper Ted Jansen, to get a close-up look at the inspiration behind the science.
TED JANSEN: Now, see? Here's one that's already stung me, see?
DAVID POGUE: What, what? But, aren't you going to say "ow" or something? Oh, my gosh.
TED JANSEN: No, that...see that's the little venom sac that they leave. But it's not the stinger that hurts you, it's the venom going in you.
DAVID POGUE: A bee sting may seem like a minor irritation, but actually the venom is extremely toxic to cells.
TED JANSEN: Immediately, when you get it out of there the, the pain stops.
DAVID POGUE: So why would it have been bad for you to just pluck it out?
TED JANSEN: Because you squeeze the sack and squeeze all the venom in.
DAVID POGUE: Oh, I see, I see.
So Sam, you're not here to see how they make honey?
SAM WICKLINE: No. We like the bees because they make a toxin. The toxin is melittin, and we use it to, specifically, to treat cancers.
DAVID POGUE: Bee venom is a cancer drug?
SAM WICKLINE: Yes, bee venom is an excellent cancer drug. It's been known for quite some time, but the problem is how to deliver it.
DAVID POGUE: Melittin is not being used yet to fight cancer, because it will destroy any cell it bumps into, including healthy ones. But, realizing its potential, Sam set out to engineer a nano-scale robot to carry the toxin safely through the body and release it only when it finds its target.
Not surprisingly, he calls his invention nanobees.
Each nanobee has three parts.
SAM WICKLINE: So, what we've got here is a model.
DAVID POGUE: Sam explains, with a simple demonstration, how they fit together.
SAM WICKLINE: This basically is a sphere of carbon and fluorine atoms that forms the carrier for that melittin.
DAVID POGUE: The center of the nanobee is a nanoparticle constructed out of several thousand of carbon and fluorine atoms arranged in a spherical cluster less than 300 nanometers in diameter.
SAM WICKLINE: And then we have a coating on that, which is a fatty kind of a coating. And this fatty coating allows us to insert the melittin toxin into this particle here.
DAVID POGUE: They would be all over this thing.
SAM WICKLINE: Exactly.
DAVID POGUE: This outer layer holds the deadly bee poison in place. It's like a holster that keeps a gun safe, until it's drawn.
Every tumor cell has a distinct chemical makeup. The outer layer of the nanobee is programmed to selectively lock onto only those cells that need to be destroyed.
SAM WICKLINE: So, if you take this balloon as a cancer cell. This nanoparticle will come up next to the cancer cell and basically merge with it. The coating will come off, and the melittin itself forms a hole in the cancer cell and pops it.
DAVID POGUE: Like its namesake, a nanobee can only sting once. So swarms of them are required for any treatment. Sam's lab has decoded the chemical makeup of the bee venom, so he can manufacture it in large quantities for his nanobee swarms.
I say goodbye to our beekeeping hosts, in order to pay a visit to Sam's lab at Washington University, to see how the nanobees work in the body.
SAM WICKLINE: So here we are in the magnetic resonance imaging suite. I'm going to show you what it's like to be a patient, as if we were looking for nanobees inside of you.
DAVID POGUE: And may I just say what a boost this gives my dignity to wear a sundress and slide into a giant bagel.
SAM WICKLINE: Well, let's go toast you.
DAVID POGUE: An M.R.I. uses strong magnetic fields and radio waves to detect certain molecules in the body. This machine has been tuned to detect fluorine, which are part of the nanobee molecules but are otherwise very rare in the body.
SAM WICKLINE: Okay, you having fun there yet? We're rolling.
DAVID POGUE: I think I remember this ride. I think I did it at Six Flags.
If Sam had actually injected nanobees into me, and if I had the cancer that they had been trained to fight, they would travel in my bloodstream and stick to any target tissue they encounter. The images that the technicians see would show bright yellow areas where the individual nanobees were finding and killing the diseased cells.
And best of all, there would be no toxic side effects, as with traditional chemotherapy.
So how far away are we from using nanobees in everyday human cancer patients?
SAM WICKLINE: Well, now this material is being tested, uh, in what's called pre-clinical stage. And we hope that, within about a year or so, that we'll have approval to test this in humans.
DAVID POGUE: Well, thanks, Sam. I appreciate this experiment. So, typically, how long would you leave the patient, lying in this tube? Guys? Guys? Hello? Hello?
Like the nanoscale transistors that came before them, nanobees get power from their tiny size. But nanobees and other emerging nano technologies go even further.
SAM WICKLINE: So this is where melittin is made.
DAVID POGUE: Nanobees are part of a new breed of small materials that self-assemble; no need for big complicated machinery to make nanobees. Put the right ingredients together, in the right conditions, and they make themselves.
This revolution in medicine, working at the tiniest of scales, would never have been possible without the revolution in electronics that preceded it. Both are transforming our world and our lives at an astonishing speed.
As we see the power in this new ability to design and build, atom by atom, there may be no more important goal in the science of materials than mastering the art of making stuff smaller.
IMAGE: (David Pogue) ©WGBH/Mark Ostow, ©iStockphoto.com/Luca di FilippoBroadcast Credits
Making Stuff: Smaller
- Host
- David Pogue
- Written, Produced and Directed by
- Chris Schmidt
- Executive Producers
- For Powderhouse Productions
- Joel Olicker
Tug Yourgrau - Co-Producer
- Alexandra McHale
- Field Producer
- Doug Gordon
- Story Producer
- Andy Howard
- Edited by
- Brian Funck
- Additional Editing by
- Kristine Gaffney
- Director of Photography
- Gary Henoch
- Additional Photography
- Tim Cragg
Ken Nilsson
Jesse Phinney - Sound Recordists
- Mark Arees
Steve Bores
Govanni Di Simone
Dan Gleich
Mike Italiano
Mike Keenen
Michael Kranicke
Adam Prescod
Chuck Stanton
James Thompson
Scott Wildfong - Grips and Gaffers
- Ari Manin
Phil Contursi
George Zorich - Production Assistant
- Daniel V. Parsons
- Music
- Lunch Special Music
- Animation
- Edgeworx, LLC
- Additional Animation
- Alan Waldo
Jenny Olson - Production Manager
- Diane Knox
- Post Production Supervisors
- Kevin Young
Michael Fallon - Assistant Editors
- Eric P. Gulliver
Peter Hyzak
Jim Fetela
Bryce Patingre - Online Editor / Colorist
- Julie Kahn
- Audio Mix
- Heart Punch Studio, Inc
- Research
- Sonia Weinhaus
Jessie Lynn Ward - Interns
- Katie Duffy
Nicole Jaques
Travis Kelley
Michael Ryan
Zach Vitale - For Powderhouse Productions
- Post Production Manager
- Melissa Walter Richards
- Senior Production Coordinator
- Carlin Corrigan
- VP of Production
- Daniel Miller
- Senior VP of Production and Post
- Robert Kirwan
- Senior VP of Sales and Development
- Seanbaker Carter
- Archival Material
- AP Archive
Getty Images
Footage Provided by Thought Equity Motion
iStockphoto
Museum of Science Strategic Projects Group
Nathan Baker
Sunjoo Lee
Periodictable.com - Special Thanks
- Producers gratefully acknowledge the cooperation of the Materials Research Society.
- Richard A. Souza
Amy Moll
Kristin Bennett
Jerry Floro
Megan Frary
Kevin Jones
Tommie Kelley
Alex King
Aditi Risbud
Stephen Streiffer
Rick Vinci
Sandra DeVincent Wolf - Special Thanks
- Mimotec
Ulysse Nardin
Professor Stephen Sass, Cornell University - NOVA Series Graphics
- yU + co.
- NOVA Theme Music
- Walter Werzowa
John Luker
Musikvergnuegen, Inc. - Additional NOVA Theme Music
- Ray Loring
Rob Morsberger - Post Production Online Editor
- Michael H. Amundson
- Closed Captioning
- The Caption Center
- Publicity
- Eileen Campion
Victoria Louie
Karen Laverty - Marketing
- Steve Sears
- Researcher
- Kate Becker
- NOVA Administrator
- Kristen Sommerhalter
- Production Coordinator
- Linda Callahan
- Paralegal
- Sarah Erlandson
- Talent Relations
- Scott Kardel, Esq.
Janice Flood - Legal Counsel
- Susan Rosen
- Post Production Assistant
- Darcy Forlenza
- Associate Producer Post Production
- Patrick Carey
- Post Production Supervisor
- Regina O'Toole
- Post Production Editor
- Rebecca Nieto
- Post Production Manager
- Nathan Gunner
- Compliance Manager
- Linzy Emery
- Development Producer
- Pamela Rosenstein
- Supervising Producer
- Stephen Sweigart
- Business and Production Manager
- Jonathan Loewald
- Senior Producer and Project Director, Margret & Hans Rey / Curious George Producer
- Lisa Mirowitz
- Coordinating Producer
- Laurie Cahalane
- Senior Science Editor
- Evan Hadingham
- Senior Series Producer
- Melanie Wallace
- Executive Producer
- Howard Swartz
- Managing Director
- Alan Ritsko
- Senior Executive Producer
- Paula S. Apsell
Produced by Powderhouse Productions
A NOVA Production by Powderhouse Productions for WGBH
© 2011 WGBH Educational Foundation
All rights reserved
Participants
- Pierre Gygax
- COO, Ulysse Nardin
- Pablo Jarillo-Herrero
- Physicist, MIT
- Jean Lopategui
- Cedars-Sinai Molecular Pathology
- Chad Mirkin
- Institute of Robotics, ETH Zurich
- Daniel S. Mishkin
- Gastroenterologist, Boston University
- Bradley Nelson
- Institute of Robotics, ETH Zurich
- Frances Ross
- IBM Research Division
- Leonie Seliger
- Head of Cathedral Studios
- Stephen L. Smith
- Vice President, Intel
- Mike Tuffey
- Owner, English Antique Glass
- Samuel Wickline
- Cardiologist, Washington University
Education and Outreach Resources
Preview
Notice: Undefined index: preview_video_length in /home/nova/zend/application/templates/resources/multi-ep-pro.phtml on line 497
Full Program | 53:54
Full program available for streaming through ...
Watch Online
Full program available
Soon
Making Stuff: Cleaner
Can innovative materials help solve the energy crisis and lead to a sustainable future? David Pogue investigates. Airing August 28, 2013 at 9 pm on PBS Aired August 28, 2013 on PBS
- Originally aired 02.02.11
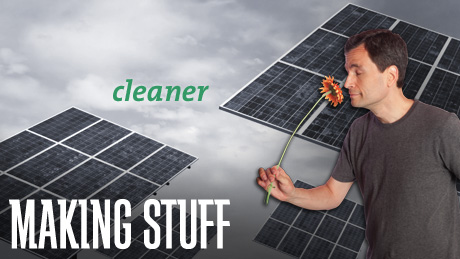
Program Description
Transcript
Making Stuff: Cleaner
PBS Airdate: February 2, 2011
DAVID POGUE: Imagine a world with buildings that can ride out earthquakes; bacteria that make gasoline; tiny devices that repair individual cells, even DNA; gossamer threads strong enough hold up a bridge; or an elevator to the stars.
These visions of the future are based in the discoveries of today, as a new science of materials emerges from the elemental building blocks of the universe, promising a future in which we can create virtually anything we want atom by atom.
I'm David Pogue...
Do you have trash around here?
PETER KENDRIGAN (Waste Management, Inc.): Yep, absolutely. You can throw it right in.
DAVID POGUE: ...and I'm on a quest to turn garbage into gold—okay, maybe not literally gold—more like turning trash into electricity...
Eighty-eight thousand homes are being fueled by their own trash?
...corn into cars;...
DEBORAH F. MIELEWSKI (Ford Motor Company): This is growing your own car parts.
DAVID POGUE: I think you've been smoking too many mushrooms.
...bags into batteries.
Chicken feathers in your gas tank.
No, no come back. Come back. I got you. I'm not going to hurt you. Stay calm. It's science.
Material Scientists are taking tips from Mother Nature...
Everybody clear the building. It's going to blow!
...to turn worthless waste into stuff we can use, stuff that disappears when we're done with it.
And everybody's getting in on the act.
JAY LENO (Talk Show Host and Car Collector): I think this is the car of the future. This is how we'll all be getting around: electric.
DAVID POGUE: This is the car of the future?
We're on the road to a zero-waste world, all part of Making Stuff Cleaner, right now, on NOVA.
I've got to confess, watching these powerful machines do their thing is a guilty pleasure.
I love the aluminum foil heat protector he puts on the windshield. Do you think he's got fuzzy dice too?
The engines in some of these cars put out 450 horsepower and can easily hit 200 miles an hour.
Apparently it's got great pickup and the least storage in its class.
I'm David Pogue. I write about technology for the New York Times. Usually I stick to gadgets like laptops and cameras but these meet my most fundamental journalistic criteria: I want one!
Cars represent power and freedom but also waste.
While they're up and running, these monsters eat up gasoline and spit out carbon, which heats up our atmosphere, all the while just going around in circles. And when they crash, like most cars, they turn into broken down heaps. Many of their parts wind up permanently parked in landfills.
That's because much of the stuff that goes into cars is plastic.
Both waste problems—petroleum and plastic—converge on cars. And both break Mother Nature's Golden Rule: we can have what we want, as long as we clean up after ourselves.
For example, my plant and I are in perfect harmony. I breathe in oxygen and breathe out carbon dioxide.
She takes in carbon dioxide and puts out oxygen. Together we make a beautifully efficient circle of life.
Imagine if all the stuff we use could be paired in such perfect harmony. That's called a zero-waste world.
My mission is to uncover some cool stuff to get us there, starting with cars.
I decided to consult with one of the foremost experts, well, at least one of the funniest, Jay Leno. Most people don't know it, but this is Jay's day job: restoring antique automobiles.
His collection of nearly 200 cars spans 100 years of history, from a humble 1941 fire engine to a ritzy 1925 Doble steam-powered convertible, once owned by Howard Hughes,...
It's like a giant furnace on wheels.
JAY LENO: This is 2,000,000 BTUs of heat.
DAVID POGUE: ...from classic American muscle cars, to a jet-powered sports car. Every car here is street-legal, and Jay likes to drive a different piece of history home each night.
JAY LENO: When you're in show business, you have drugs, women or find something else to do. This is something else to do.
DAVID POGUE: While doing his something else, Jay has become a guru of auto technology, and he's got some insider info on the car of tomorrow.
JAY LENO: I think this is the car of the future. This is how we'll all be getting around: electric.
DAVID POGUE: This is the car of the future?
JAY LENO: Well this is a 1909 Baker electric. Uh, there's no pollution. This was high tech back in the day.
DAVID POGUE: Talk about back to the future. The 1909 Baker runs on energy stored in batteries.
Wow.
JAY LENO: You have six batteries in front.
DAVID POGUE: As with today's electric cars, you charge the batteries by plugging the car in.
I'm going to stop exactly at 10 bucks.
But in those days, electric cars were commonplace. There were charging stations all over New York City.
JAY LENO: This is one of the original charging stations. Sort of like Frankenstein, you'd throw these levers, and electricity would surge through.
DAVID POGUE: Did, would you have to laugh like that to get it to work?
JAY LENO: Yeah, you had to laugh. You had to do that every time. See that's one other reason that it died. People just hated doing "ha ha ha..." doing that every, every single time. That got to be very annoying.
DAVID POGUE: Everybody's a comedian.
JAY LENO: You want to go for a ride and see what it's like?
DAVID POGUE: Yeah! This runs? You don't take it on...
JAY LENO: Of course it runs. You seem so stunned by...
DAVID POGUE: I like this. You've got the user's manual on the seat. That's a good, good sign.
JAY LENO: Yeah, but I'll show you how, sort of, maintenance-free these are. All you do is turn the key, and you are, uh...
DAVID POGUE: That's the wheel?
JAY LENO: ...ready to go.
DAVID POGUE: Oh, my god. No way.
It's a great ride, really quiet because there's no roaring engine, just the hum of an electric motor.
So in this car, I see a meter down there. That's your, your fuel gauge so to speak?
JAY LENO: Volts and amperage, yeah.
DAVID POGUE: What's your top speed in the Baker?
JAY LENO: Twenty-two.
DAVID POGUE: Twenty-two?
JAY LENO: About 22.
DAVID POGUE: Just right for L.A. traffic jams.
JAY LENO: Don't forget, though, when this car was built, the speed limit was 12. I mean that's what it was. There was no paved roads. I mean you had cobblestones, so...
DAVID POGUE: A fully charged battery is good for 60 to a hundred miles, more than enough for an excursion around early 1900s Manhattan.
JAY LENO: Nobody really went much out of Manhattan. Only rich people had these; and taxicabs. They'd run for three or four hours, go back to the, uh, charging station, take another car while that was being charged. So, it worked out quite well.
DAVID POGUE: Well, at least until you wanted to drive anywhere outside of New York, because for providing power on the go, batteries just can't beat gasoline.
JAY LENO: Gasoline is almost the perfect fuel. A gallon of gas gives you so much power, even though you need this much battery to get the power of this much gasoline.
DAVID POGUE: If the electric cars of the 21st century are to avoid the fate of the 1909 Baker Electric, they'll need a better battery.
JAY LENO: This seems to be the future, but you know, electricity is like sex: people have no compulsion about lying about it. You know?
I mean every electric vehicle that I get, "Oh, this will go a hundred miles." Well 48 miles later, I, I'm stuck by the side of the road.
DAVID POGUE: But it's no lie that more juice and a longer lasting charge are essential in a battery.
In all batteries, electricity is created by a chemical reaction. There are two metals, called electrodes, that want to exchange electrons. But between them is a third material, called an electrolyte, that keeps the electron transfer in check.
But, if we give those electrons an easier path from one electrode to the other, like through a circuit, say the bulb in your flashlight or the electronics in your phone, the flow begins, creating an electric current.
In a car battery the electrodes are made of lead and lead dioxide, and the electrolyte is sulfuric acid. That's enough juice to spark ignition and to power forklifts and golf carts, but not the engine of a car. They just don't hold or put out enough power.
JAY LENO: Electricity is like an animal. You put it in a jar and it either escapes or it dies. You take a battery that's fully charged and you put it on the shelf, you come back in three weeks, the electricity went away. Where did it go?
DAVID POGUE: But now scientists are mixing up materials to get more bang out of batteries, like zero to 60 in less than a second,...
...packing the power of 150 car batteries onto this small frame.
The wobble you see in the picture is our TV camera's way of saying "Woooooo!"
With over 500 horsepower, this bike is one of the fastest electric motorcycles in the world. Its battery pack could easily power an electric car. And I know where this baby comes from!
The facility we're about to visit has been considered by some the global headquarters for the future of electric vehicles in America. I just hope I can make it through security.
The juice we're looking for may be here, in suburban Denver, hidden behind this garage door.
Here it is.
Looks like you guys are into bikes or something.
BILL DUBE (KillaCycle): Yeah, we like electric ones, that's for sure.
DAVID POGUE: Bill Dube and Eva Hakansson are C.E.O.s, V.P.s of R. and D., actually everything from A to Z, at an electric motorcycle company called KillaCycle.
Not the normal motorcycle.
BILL DUBE: No.
DAVID POGUE: I know that my hog looks very different from this.
BILL DUBE: Does it?
DAVID POGUE: Yeah.
Bill has agreed to share the top secret technology responsible for Killacycle's world speed record.
BILL DUBE: It's just a giant cordless drill with wheels.
DAVID POGUE: You're a colorful man, Bill.
BILL DUBE: It is! It's that simple.
DAVID POGUE: A giant cordless drill, okay.
BILL DUBE: It's that simple. It has a battery, which we can take out of here, right? It has a motor. And it has a throttle, right? Okay? This has the battery down here, right? It has the motors, right here. And it has a throttle.
DAVID POGUE: Okay, but what makes the Killacycle faster than an electric drill is the battery. More than a thousand of them live underneath this panel. Bill and Eva make them fit underneath by welding individual cells together.
They get the batteries from a company called A123 Systems. And the reason A123 can pack so much punch into these little cells is because of the stuff they make them with. Instead of the lead used in traditional car batteries, they use lithium. Lithium is a great choice because its atoms are so small. It's the third smallest element on the Table of the Elements.
Smaller atoms means more flowing electrons and more electricity that can be generated by the battery, but what makes these A123 batteries even better is the internal structure of the electrodes.
There are so many nano-scaled nooks and crannies, they provide more pathways for electrons to move through the battery and into the wires. That means more power, faster charging and a longer lifespan.
Bill has a different explanation. He calls it "the Slurpee® and the straw."
BILL DUBE: With a Slurpee, you have a certain amount of juice in the cup. That's the specific energy.
DAVID POGUE: Okay.
BILL DUBE: The energy it holds is how much juice there is in the cup. Then, the power is the size of the straw.
DAVID POGUE: So the battery's storage capacity is like a super-concentrated Slurpee, and its high power output is like shooting the juice with a lot of pressure through a really wide straw, all in a small compact container.
BILL DUBE: It's unbelievable. Cells this big around putting out more power than these big cells, it's...
DAVID POGUE: No wonder you're cackling like a madman.
And no wonder these Killacycles are some of the fastest electric bikes in the world. But there is one last question that I have been dying for them to ask.
EVA HAKANSSON (KillaCycle): So, do you want to take one of our electric bikes for a ride?
DAVID POGUE: Yeah.
EVA HAKANSSON: Okay, let's go out here.
DAVID POGUE: Not this one?
EVA HAKANSSON: No, not that one.
BILL DUBE: Let's get it out of the race trailer for you.
DAVID POGUE: It's in here?
BILL DUBE: Oh, yeah.
DAVID POGUE: Oh, oh, oh.
My motorcycle is in the trailer behind that Exercycle?
BILL DUBE: No, this is the one we're going to have you ride. You've got to start somewhere.
DAVID POGUE: Everyone's a comedian.
Bill assures me that you just pedal it to get started.
It's not quite the same thing.
Okay, here we go.
Vroom, vroom! You have to supply the noises with your mouth.
'Bye, guys. I'm off to the market.
This is not electric. Oh, my god. Whoa! Oh, my god! You want to tell me how it works? Jeez!
You didn't really explain how you stop it.
Clearly, I'm not ready for the big bikes.
With that much power stored in such a small space, could these supercharged lithium batteries supply the juice we need for electric cars?
The batteries do have a few drawbacks. They are still expensive, and like petroleum, lithium is a limited resource. But A123 is opening the largest lithium automotive battery factory in the U.S. right outside the motor city, Detroit. So if electric vehicles catch on, these little guys could be the next big thing.
But there could be an even more radical solution to the power problem, using one of the most abundant materials in the universe: hydrogen.
General Motors has about a hundred of these hydrogen-powered SUV's out on the road. They're being test driven by ordinary folks, ordinary folks aaaaand Jay Leno!
JAY LENO: I've been driving this for two years, and it's fantastic! It is zero emissions, not point one per billion, zero!
DAVID POGUE: And when Jay says "zero," he means zero!
JAY LENO: I mean, if you went into the garage, shut the garage door, sealed it, turned on the engine, and sat in this car, you would starve to death before anything else happened to you.
DAVID POGUE: Jay offers to show me where the magic happens.
Oh, man!
JAY LENO: Not a lot to look at.
DAVID POGUE: Not going in here with your screwdriver.
JAY LENO: No, but as you can see, there's a lot of technology here. And it's American technology, which I like.
DAVID POGUE: The technology he's talking about is called a fuel cell. Like a battery, a fuel cell creates electricity through a chemical reaction. The fuel, in this case, is hydrogen, which the fuel cell combines with oxygen from the air. The result? Electricity to run a motor. Nothing comes out the tailpipe but a little water vapor.
Those are the kind of emissions we could live with.
STEPHANIE WHITE (Project Driveway Participant): All right, come on, let's go.
DAVID POGUE: And for people who drive a lot, like Stephanie White, no pollution is great, and great mileage is even better.
STEPHANIE WHITE: So this is my old car: about 30 miles to the gallon...
Come here. Hop in. Good boy.
...and the Chevy Fuel Cell Hydrogen vehicle: about 55 miles to the gallon.
DAVID POGUE: The hope is that someday hydrogen won't cost any more than gasoline does today, and your mileage will double.
That clean, economical future is one reason why Stephanie applied to be a test consumer in General Motors' Project Driveway, a program that puts hydrogen fuel cell cars into real world conditions.
But there are a few problems.
Getting hydrogen into a usable form takes energy, and right now there's only a handful of places to fill up.
While the process looks familiar, it requires very different equipment since the hydrogen has to be pumped into the tank under pressure.
STEPHANIE WHITE: The system pressurizes the tank to a certain level, and then it switches to another tank that's at higher pressure. So it goes about four times, and that brings it up to 10,000 P.S.I.
DAVID POGUE: Speaking of hydrogen under pressure, remember the Hindenburg? That was the German hydrogen blimp that exploded with 97 people on board.
Hydrogen may not have had anything to do with the fire; it may have been the skin of the blimp that fueled the flames, but hydrogen still makes people nervous.
A more realistic problem is how far the hydrogen car will go on a tankful. Right now, it's only about 250 miles, which is not as far as a tankful of gas will take you, but materials scientists may have a solution to that problem.
Here it is folks. The future of American hydrogen storage: chickens! Or, more specifically, their feathers.
You see, there's this scientist in Delaware...
RICHARD WOOL (University of Delaware): Here we go. A little hydrogen lift here.
DAVID POGUE: ... who says if we cook the feathers at just the right temperature, we can turn them into high-tech hydrogen storage devices.
This is, uh, how your students get around town?
RICHARD WOOL: They're riding on pure hydrogen, zero waste output.
DAVID POGUE: And zero waste output is exactly what Professor Richard Wool is after. He gave me a quick primer on hydrogen and chicken feathers.
RICHARD WOOL: Hydrogen is a gas that likes to be free. It likes to occupy a lot of space. And so, to compress it into a small space, like the size of your gas tank, you know, 20 gallons, requires enormous pressure.
DAVID POGUE: Take a look at the hydrogen tank on top of this bus. It's almost as big as the bus itself!
So how can we get more hydrogen into less space without a lot more pressure? That's where the chicken feathers come in.
RICHARD WOOL: So the chicken feathers are like a sponge and draws the hydrogen gas closer, and that drops the pressure in the tank.
DAVID POGUE: So Richard took me to the nerve center of his research to show me how his feathered friends are helping him with the solution to the storage issue.
RICHARD WOOL: Well, this is my plant. This is where I grow the materials for, uh...
DAVID POGUE: Your plant?
RICHARD WOOL: Hi, guys, we're back.
DAVID POGUE: Before we can catch the hydrogen, we've got to catch the chicken.
Uh, I've never caught a chicken, but it can't be all that hard.
RICHARD WOOL: It's very easy. I'll show you. You need to walk over very slowly.
DAVID POGUE: Slowly, okay. Oh, no, no. Come back, come back. I've got you. I'm not going to hurt you. I'm not going to hurt you! Everybody stay calm. It's, it's science. Arghhh! You, right there, right there. Stay.
I almost had it.
RICHARD WOOL: So this is a feather. You see the quill and then you see the hairs. And the hairs are hollow.
DAVID POGUE: And when you heat up the hollow hairs, they become nanoporous. That means they have lots of really, really small pores that provide more places to store hydrogen atoms with less pressure.
But there's a more basic question.
But why chickens? I mean, surely there are bigger bird breeds with better feathers.
RICHARD WOOL: We could do this with any bird; it's just a question of the volume of raw materials. The chicken is the largest processed bird in the U.S.A., and there's about six billion pounds of waste material.
DAVID POGUE: Wait, wait. They throw away the feathers?
RICHARD WOOL: They throw away the feathers.
DAVID POGUE: I know; it's upsetting to me too.
Richard figures he can recycle these wasted feathers into a storage material for hydrogen fuel.
Can you say hydrogen? Hydrogen?
He took me along to his lab to show me how they do it.
First, they remove the quills. They are left with the fluffy feather fiber.
RICHARD WOOL: So what we do here is we take this feather fiber and then we heat them up to this much higher temperature, and that's when we get an enormous increase in surface area. And so, this black carbonized chicken feather fiber then becomes this sponge, to soak up hydrogen.
DAVID POGUE: When you heat them to 750 degrees Fahrenheit, the chicken feathers become over 200 times more absorbent, because trillions of tiny little caves developed in the fiber. You got it: nanopores. They give the hydrogen atoms a place to nestle.
In theory, this material could fit enough hydrogen into a normal-sized gas tank to allow 300 miles of travel between fill ups and almost no pressure.
But cooking chicken feathers?
It seems like a lot of trouble and steps to go from the chickens to the stuff we're putting in our hydrogen cars. Isn't there some manmade synthetic way that would be faster, just as good?
RICHARD WOOL: Oh, you can. You can absolutely make these using things like carbon nanotubes and other materials. The difference is that this process is almost for free, whereas the carbon nanotubes and other such materials would cost you the equivalent of about a million dollars for your gas tank.
DAVID POGUE: Yeah, that would put a small damper on car sales in this country.
RICHARD WOOL: So these are cheap, cheap, cheap.
DAVID POGUE: If we want to make hydrogen a viable fuel, Richard Wool and his fine-feathered friends may have found a cleaner way, and all for the cost of chicken feed.
Cars with electric motors, fueled either by hydrogen or super-charged batteries, could cut the cord to gasoline. But once upon a time, gas-fueled cars were seen as a way out of another environmental hazard: horse pollution. And if you don't believe me, you can hear it straight from the freakishly knowledgeable comedian's mouth.
JAY LENO: The car was seen as the great savior of the American horse because in, in the early 1900s you had thousands of tons of horse manure on the streets of New York every day. People dropping dead from dysentery and, and just the smell.
If the horse collapsed in the street, they just cut the reins, and they'd walk, and they'd leave a dead carcass. So, consequently, you had New York City garbage men and stuff going around, picking up hundreds of dead horses in New York City every day. The horses literally worked to death. So when the car came along, oh, my god, this was the, as I said, the great savior. Instead of horse manure you get a little puff of blue smoke occasionally, and that didn't seem so bad.
DAVID POGUE: Yeah, until millions of gas-powered cars started spewing blue smoke filled with lead, sulfur and other pollutants.
Over the last 50 years we've cleaned up a lot of these toxic pollutants. Today, we're mainly left with invisible carbon emissions that are a by-product of burning gasoline and a contributor to global warming. As Jay reminds me, this is not the fault of our cars and engines, the problem is the fuel.
JAY LENO: You know, there's nothing wrong with internal combustion engines. We just don't happen to like the fuel. Why throw away 150 years of proven technology? Internal combustion works; we just don't like the fuel or the byproduct. So, change the fuel and the byproduct.
DAVID POGUE: Wait, does Jay know something we don't? Is it possible to run our internal combustion cars with a fuel that doesn't come from oil?
Materials scientist Jay Keasling has created genetically modified bacteria that do just that: they eat plants and make gas.
JAY D. KEASLING (Joint BioEnergy Institute): These microbes are miniature chemical factories that take in something very inexpensive, like a sugar, and turn it into something really valuable, like a fuel.
DAVID POGUE: A fuel like gasoline.
My plant can explain. Her body, like all living things, is made from carbon. When her ancestors died, millions of years ago, they took the carbon in their bodies with them safely underground. Over the years, that carbon fossilized and became oil. When we burn this fossil fuel, we rapidly release millions of years of buried carbon back into the atmosphere, contributing to global warming.
But Jay's process is carbon-neutral. His microbes make liquid fuel from plants that are growing now, absorbing carbon from the atmosphere. It's called "biofuel," and, unlike ancient fuel, burning biofuel doesn't add any new carbon to the atmosphere.
It's got all the power of fossil fuel, without the fossils.
JAY D. KEASLING: So if you think about the infrastructure that we have in the U.S., if we can make fuels that are identical to the petroleum-based fuels, then we can use all of that infrastructure for this new fuel.
DAVID POGUE: Existing biofuels have been criticized because they're made from food crops, like corn. But Jay's microbes can eat stuff we can't, like switchgrass and wheat chaff. And the gas they make is good to go as diesel, right into our cars, trucks, trains. It doesn't have to be refined, which takes energy.
Okay, biofuel, better batteries and hydrogen: three cleaner alternatives to petroleum. But I'm the gadget guy, and even I don't know which one to choose. I defer to my car guru who says the innovation that takes us there, will be obvious only in hindsight, and won't catch on until we're ready.
JAY LENO: I remember when I was a kid, in 1964, we went in to buy a new Ford, and my Dad said to the salesman "Does this car have seatbelts?" And the salesman: "Seatbelts? Hey, Louie, we got a racecar driver here. He wants seatbelts. What are you going to crash? What are you a bad driver? We got a driver, what? You going to go 100 miles per hour?" Just humiliated my father. You know you can't, you can't sell something before its time.
DAVID POGUE: In time, clean technology will be like seatbelts, standard equipment. And solving the petroleum fuel problem in cars will drive us a long way down the road to a zero-waste world.
Petroleum makes a powerful fuel. There's a lot of energy stored in the strong atomic bonds between hydrogen and carbon.
For that reason it's also used to produce super strong material, starting where the rubber meets the road.
The stuff in our tires? We call it rubber, but it's really not. Real rubber comes from trees. This stuff is a synthetic material made with petroleum.
It's one of the hardest materials to break down. That's good for driving but bad in a zero-waste world. But my nose tells me there's something different about these babies.
I understand that these tires have something more than plain black rubber in them.
SAM KWA (Yokohama Tire Corporation): That is correct. They actually have orange oil, in them.
DAVID POGUE: Orange oil?
SAM KWA: Yes.
DAVID POGUE: Just to give them a zesty citrus aroma for the race?
SAM KWA: No, we haven't gone that far to provide an actual natural orange oil smelling tire. But what we've done is we've replaced petroleum oil with orange oil. So it reduces our petroleum footprint. So it's an eco-friendly racing tire.
DAVID POGUE: An eco-friendly tire, so, less, petroleum in these tires?
SAM KWA: That is correct.
DAVID POGUE: Regular tires use about a barrel of oil per tire. Mixing in orange oil reduces that petroleum use by 20 percent. And while reducing petroleum use is good, replacing it with bio-degradable orange oil is better. Best is when that replacement material was getting thrown away anyway.
So, pretty cool; you're rescuing orange peels from the landfill, and you're using them to replace petroleum in actual useful products. But that's a very high-tech use of oranges. You want to know what a good low-tech use of orange is?
SAM KWA: Sure.
DAVID POGUE: Breakfast.
SAM KWA: Great, thank you.
DAVID POGUE: Imagine if eco-friendly ingredients could replace more eco-enemy car parts, beyond tires. It's an idea almost green enough to eat.
Okay, so this is a, uh, attractive car. I can't say it looks any greener than any other car, but you're telling me there's something green about this car that last year's model didn't have.
DEBORAH F. MIELEWSKI: This is a 2011 Ford Fiesta, and we're just launching this vehicle. What I'm most proud of...it has the soy foam seats in it.
DAVID POGUE: It has sea foam?
DEBORAH F. MIELEWSKI: Soybean foam. So, we replaced the petroleum materials with soybean oil. Give it a try. Let me know what you think.
DAVID POGUE: Professional cushion tester, David Pogue.
And in cars, the cushions are just the tip of the plastic iceberg.
Yeah it, it feels, like a carseat. It feels comfortable.
DEBORAH F. MIELEWSKI: Now, look around you. Do you see anything that's not plastic?
DAVID POGUE: Oh, my gosh. Plastic, plastic, plastic, plastic, plastic.
DEBORAH F. MIELEWSKI: Everywhere.
DAVID POGUE: Yeah.
About 300 pounds of plastic in an average American car. The problem with plastic as a material goes deep, like, to a molecular level.
Plastic is a polymer, chains of carbon, hydrogen and oxygen atoms that are so strong, it takes bacteria thousands of years to decompose them. Plastic achieves this unnatural invincibility because, a) it's made from petroleum and b) it just ain't natural. It's a manmade molecule, the first stuff in the history of the world that is totally synthetic.
Materials scientist Leo Bakeland invented it in 1907. He became a very rich man.
Originally called Bakelite, the name didn't last as long as the material.
First, Bakelite found a foothold in industry as wire insulation, high precision gears, and even machine guns. Eventually, it caught on with consumers as jewelry, rotary dial telephones, radios, and, yes, car parts.
Today its descendants are everywhere, but that may change. Ford is already replacing 10 percent of that petroleum-based plastic with stuff that's much easier to digest: food.
I look at this and I don't say to myself "car seat." How, how does something like this get to be plastic?
DEBORAH F. MIELEWSKI: We take the soybeans and we press them, and you get soybean oil.
DAVID POGUE: So, instead of using hard-to-decompose petroleum-based plastic, Ford is substituting soy and other vegetable oils to make bioplastic.
Fifty grams, all right.
PATRICA C. TIBBENHAM: Going to mix it for 30 seconds.
DAVID POGUE: And after we're done with this can I have a blueberry smoothie?
Other than the ingredients, there's not much difference in the process.
Oh, my god. Everybody clear the building! It's going to blow! The soy foam is taking over!
Ford is using bioplastic not only in soft foam seats, but also for hard plastic surfaces like the dashboard. And they're making other car parts from stuff that's left over from harvesting wheat.
Eighty percent of all plastic car parts are made using an injection mold process. The difference here is the wheat.
It seems like a scene from Willy Wonka. Whahahaha!
The machine takes a wheat-straw-plastic mixture, melts it, and pushes it into a mold. The mold cools and pops out a plastic part.
So we've gone from this to this, in 400 easy steps.
This is just a test strip, but this bin for the Ford Flex is made of wheat grass. It decomposes, it's carbon-neutral, and it's already saving tons of petroleum a year.
DEBORAH F. MIELEWSKI: Even this small part on only the Flex conserves about 30,000 pounds of petroleum each and every year.
DAVID POGUE: And there's actually more than one way to mold car parts. They can actually be grown.
DEBORAH F. MIELEWSKI: This is mushroom mycelium, so, the root of a mushroom plant.
DAVID POGUE: Wait, wait, this stuff is made from mushrooms?
DEBORAH F. MIELEWSKI: Yes, so what happens...
DAVID POGUE: Come on.
DEBORAH F. MIELEWSKI: This is really cool.
DAVID POGUE: Ford mixes a little mushroom mycelium together with some other plant matter, like the wheat straw, and they put the mixture into a mold shaped like a car part. They close the mold and the mushroom mycelium grows because it's feeding on the plant matter.
After about a week, it's filled the mold, they take it out, and it's in the shape of a car part. Just cover it with a little bioplastic and it's ready to go.
DEBORAH F. MIELEWSKI: This is growing your own car parts.
DAVID POGUE: Okay, now, I think you've been smoking too many mushrooms.
Growing cars from plants is the ultimate green auto technology, but the proof of the pudding is in the driving.
Shall we see what she's got? Going to be some bumps. Whoa! And yes, folks, the soy-based seat cushions are performing well at 40 miles an hour.
On the road to cleaner stuff, reducing the use of a limited resource and replacing it with stuff that can be replenished, makes a lot of sense. And it could have a surprising added benefit.
There's a handy bonus if you're ever, like, crashed on a desert island, and there's nothing to eat, you can always go for a little soybean.
DEBORAH F. MIELEWSKI: I don't think so.
DAVID POGUE: Mixing plant-based ingredients into plastics is a tasty idea, especially to Mother Nature. She's got an appetite for decomposing organic things, like plants and animals, you know? Ashes to ashes, dust to dust. But, we're never going to eat our way through the world's plastic waste.
We produce more than 300 million tons of plastic every year. Of this smorgasbord, only a third can be replaced with bioplastics. The rest of our plastic buffet is artificially flavored with, polyethylene, polypropylene and polystyrene. These materials are called thermoplastic, the flimsy petroleum-based stuff that's so cheap we throw it away: milk bottles, plastic bags, cups, bottles, knives, forks, and packing peanuts.
But some materials scientists are dreaming of transforming cheap plastic bags into valuable stuff. That kind of alchemy is what's cooking here. Chief wizard in charge is Vilas Pol.
What are you some kind of James Bond villain?
VILAS POL (Argonne National Laboratory): Uh, do you want to cook your plastic?
DAVID POGUE: Oh, boy, do I! All day I've been saying I want to cook my plastic.
VILAS POL: So let's do that.
DAVID POGUE: Now, my mom always told me you don't put plastic bags in the fire because it releases poisonous chemicals, and that's true. If you just heated the plastic on the stove, carbon-based chemicals like benzene could get into the air, creating a cancer risk.
But Vilas has created a thermoplastic reactor, a closed system that uses extreme heat to break down the chemical bonds and transform the resulting carbon into a valuable material.
The recipe is simple: cut many plastic bags of any color into small pieces,...
Okay, I feel like the environmental Martha Stewart here.
...put the pieces into the reactor, add a pinch of cobalt acetate.
You, you want to try not to spill.
Set the temperature to 1,400 degrees Fahrenheit, insert the reactor, throw the switch, and cook for three hours.
Okay, so three hours have elapsed, and we're going to take a look at what you've cooked up.
VILAS POL: Okay.
DAVID POGUE: It looks a lot like black powder, but Vilas has another name for it: carbon nanotubes. Nanotubes are 1/50,000 the thickness of a human hair, conduct electricity 10 times more readily than many metals, and store five times as much energy. That led Villas to find a really practical application for his plastic-bag-formulated nanotubes: batteries.
He coats very thin slices of copper with the former plastic bag material, adds lithium and layers them with plastic spacers.
My experience with this is limited to, like, ham, Swiss and turkey. You'll have to forgive me.
He squeezes it all into a little case, and when we test it...
Okay. I touch it, and look at that! Two dollars and eighty-nine cents.
VILAS POL: No, that is a voltage.
DAVID POGUE: That's the voltage, okay.
But Vilas isn't stopping here with these little power cells. He's already producing rechargeable lithium batteries for cell phones.
He calls this process—transforming wasteful plastic bags into valuable batteries—"upcycling." He could be ready within the next year to go into large-scale production. Not only could upcycling help solve the plastic waste problem; it could also make someone a fortune.
Won't you be the guy who becomes the billionaire?
VILAS POL: Uh, hopefully me and you.
DAVID POGUE: We'll talk about the investments later.
But while upcycling may be a giant mind-shift toward cleaner stuff, it's just one small step toward a zero-waste world.
In fact, if we could eliminate all plastic and all carbon emissions from all the cars in the world, we would still be only a third of the way there.
By far, the biggest contributor to our energy problem comes from very close to home. In fact, it is our homes and the places we work. Every time you turn on a light, you draw electricity from the "grid" —a complex network that delivers electricity to homes, offices and factories. And when the fuel that makes that electricity is coal, oil or even natural gas, more of those planet-warming carbons pour into our atmosphere.
Here in Peekskill, New York, the Wheelabrator plant burns trash instead of fossil fuel to make electricity.
Hey.
PETER KENDRIGAN: Hi, Dave. How you doing?
DAVID POGUE: Okay, how you doing?
PETER KENDRIGAN: Nice to meet you.
DAVID POGUE: Do you have a trash around here?
PETER KENDRIGAN: Yep, absolutely, you can throw it right in.
This is our fuel. The main purpose is to change the energy from trash into energy.
DAVID POGUE: What about all the nasty emissions you get from burning garbage?
Well, Wheelabrator has figured out that if you burn garbage hot enough, long enough, in a nearly closed system, then almost no carbon or pollutants are released into the atmosphere.
PETER KENDRIGAN: The furnace is designed to burn around 2,000 to 2,500 degrees. That's going to ensure complete combustion, and that way, there, the emissions that come out of it will be minimal to begin with.
DAVID POGUE: So you burn it. You're burning trash here?
PETER KENDRIGAN: Absolutely, yeah.
DAVID POGUE: But doesn't that release nasty toxic stuff into the air?
PETER KENDRIGAN: Uh, no. The specific design of our boilers prevents that.
DAVID POGUE: The technology is new but the principle is as old as a 19th century locomotive. And the process is quite simple.
Trucks unload household garbage; giant cranes toss it, ten tons at a time, like a giant mixed salad, ensuring that an even mixture is combusted in the 2,000 degree furnace.
PETER KENDRIGAN: Take a peek inside. You can see the whole process happening, right in front of your eyes.
DAVID POGUE: Oh, my god! It's the gates of hell, fueled by pizza boxes.
The heat rises, boils water in a network of thousands of tubes, and creates steam that turns a turbine that generates electricity.
And this is the real payoff, right?
PETER KENDRIGAN: Absolutely. This is our clean, green energy going right off of the grid.
DAVID POGUE: Electricity that you are selling back to the electric company.
PETER KENDRIGAN: Correct.
DAVID POGUE: The electricity is cleaner than coal-burning plants.
There are already over 400 of these waste-to-energy plants in Europe and about 100 in the United States. And just this one, here, in Peekskill, New York, burns enough trash to fuel the electricity needs of 88,000 homes.
Eighty-eight-thousand homes are being fueled by their own trash?
PETER KENDRIGAN: Absolutely.
DAVID POGUE: But even if we burned all our trash, we still wouldn't generate all the electricity we need. And one of the biggest problems with our grid is that we have to keep fueling power plants, even when we're not using the energy, so a lot of electricity goes to waste.
But what if we could store that electricity in really big batteries? And what if we could make those giant batteries dirt cheap?
DONALD SADOWAY (Massachusetts Institute of Technology): And the only way I know to make something dirt cheap is to make it from dirt. And so that's the approach I'm taking with my group.
DAVID POGUE: Make it from dirt?
DONALD SADOWAY: Make it from dirt, from American dirt.
DAVID POGUE: The dirt Don Sadoway has in mind is aluminum, the most abundant metal in the Earth's crust.
He's rethinking the old-fashioned aluminum smelter, the giant boiling cauldron used to extract molten metal from rocks.
DONALD SADOWAY: ...aluminum smelter is just, basically, a large bath and two electrodes.
DAVID POGUE: The aluminum smelter is already two thirds of the way to being a regular battery. One electrode is the molten aluminum at the bottom, sitting in an electrolyte bath of salt. As the second electrode, Sadoway adds a lighter molten metal that floats on the top and has just the right chemistry to react with the aluminum and salt.
Three layers of cheap molten minerals forming an electric battery: just charge it up with the unused electricity we already generate during hours of low demand and Sadoway's battery will store that energy until it's needed.
DONALD SADOWAY: There are estimates that we can increase the effective generating capacity of this country by 15 percent without building one power plant.
DAVID POGUE: Giant batteries could also solve one of the biggest problems with sun and wind energy: what to do when the wind don't blow and the Sun don't shine. A giant aluminum battery could store the Sun and wind power and deliver it to the grid when we need it.
But the power plant and grid model is actually an incredibly wasteful way to supply electricity. Nobody wants a giant power plant or smelter in the backyard, so they have to be located far away. And by the time the power travels over wires to the cool gadgets in our homes, nearly half of it is wasted.
And a third of the people on the planet don't even have access to electricity because they're nowhere near a grid. So, imagine if all the people of the world could get clean electrical power without a grid. That's what one scientist, K.R. Sridhar, is trying to achieve.
He calls his invention a battery with a twist, but officially it's called a Bloom Box. It works on the same principle as a battery, but it's made with different stuff.
K.R. SRIDHAR (Bloom Energy): So this is the electrolyte. This is the quote-unquote "acid" in your battery.
DAVID POGUE: Yeah, I'd much rather have this sitting near my children.
K.R. SRIDHAR: I'd rather have this. I can't do this with a, I can't do this with lead acid, you know, sulfuric acid.
DAVID POGUE: You, you can, you would just be dead, yeah?
K.R. SRIDHAR: Right, exactly.
DAVID POGUE: As in a battery, the electricity is created by a chemical reaction.
But, as in a fuel cell, that reaction is created by two gases flowing in from the outside; in this case, natural gas and oxygen on opposite sides of the card.
The reaction pulls electrons from the oxygen atoms, which generates an electric current.
And how much electricity can this puny little playing card generate?
K.R. SRIDHAR: Today it produces 25 watts, enough for a big bright light in your house.
DAVID POGUE: This, this one thing?
K.R. SRIDHAR: This one thing.
DAVID POGUE: Well.
Bloom Energy piles these small fuel cells into stacks, which will have a big effect. Just two stacks are enough to power an average American house. They'd fill a box about the size of a window air conditioner.
Bloom Boxes the size of a parking space are already producing enough electricity to power offices and factories of some Big Fortune 50 companies like FedEx, eBay and Google.
K.R. SRIDHAR: It is generating enough juice for about a 20,000-square-foot office building.
DAVID POGUE: That's, like, a whole office building?
K.R. SRIDHAR: Whole office building.
DAVID POGUE: Or a small factory, right?
K.R. SRIDHAR: Or, or a small supermarket.
DAVID POGUE: Small supermarket.
K.R. SRIDHAR: Or four Starbucks.
DAVID POGUE: Four Starbucks or one of my house.
K.R. SRIDHAR: Right.
DAVID POGUE: I'm kind of a gadget freak.
Electricity from the Bloom Box costs 40 percent less than power from fossil fuel power plants, with only one-third the pollution. For now, the Bloom Box still has to be hooked up to a natural gas line. But K.R. has plans to tap into a source of unlimited power that comes with no strings attached: the Sun.
And chief materials scientist, Mother Nature, has already invented a way to harness that power: my plant. She converts sunlight into energy, which she stores as sugar in her cells. That's photosynthesis.
We tap into that energy by burning or eating plants.
Not you.
But what if we could imitate that process by making like a leaf?
That's what Nate Lewis is doing.
He's got a major grant from the United States Department of Energy to convert sunlight into chemical fuel. It's what he calls artificial photosynthesis, and he claims he can do it better than my plant.
NATE LEWIS (California Institute of Technology): We have systems already in the lab that do show that we can capture, convert and store the Sun's energy into chemical fuel, more than ten times more efficiently than the best plant on our planet.
DAVID POGUE: The power of the Sun is no secret.
More energy from the Sun hits the Earth in one hour than all the energy consumed on our planet in an entire year. We already have solar panels that convert sunlight to electricity, but they're fragile and expensive, because the silicon they're made of has to be very pure.
But Nate's got a cheaper, more durable way to make solar cells, modeled on the leaves of the Aspen tree.
His silicon is shaped like veins of a leaf, embedded in a conductive plastic film. The shape allows electrons to flow through the veins, even if the silicon has impurities. And Nate's silicon leaves are cheap to grow and flexible enough to be rolled out like a solar blanket.
All right, so this is the big moment. As I understand it, that is Nate's magic microwire: rollable, cheap, solar panel material.
NATE LEWIS: So this is making electricity just like the panels would make on your roof. There's no current when there's not much light, and then it sees the nice California sun, then we get more current.
DAVID POGUE: Now here's the artificial photosynthesis piece of the puzzle, the energy storage.
NATE LEWIS: The best way to store energy is in chemical bonds. That's what nature does in photosynthesis. That's why we call this artificial photosynthesis.
DAVID POGUE: Nate puts his silicon leaves into regular old water. The electric charge generated by these tiny solar panels splits the H20 into its component parts, hydrogen and oxygen.
NATE LEWIS: You can see, if you just flip the switch, and then we will see the bubbles coming off of that as it does that chemical process. So, be my guest.
DAVID POGUE: I'm going to turn on the Sun?
NATE LEWIS: Turn on the Sun.
DAVID POGUE: This always happens, people say, "Here comes David Pogue. It's like the Sun coming out." Okay.
Whoa! So, those are bubbles of?
NATE LEWIS: Hydrogen gas.
DAVID POGUE: By converting sunlight into storable energy, Nate has figured out how to imitate what plants have been doing for billions of years: photosynthesis.
If this scales up, the hydrogen produced could be useful in fuel cells to power our cars, homes and factories.
And now, my plant is happy and so am I.
She takes my carbon dioxide and uses it to grow, giving me oxygen in return, and scientists are learning to make energy and materials in the same sustainable way, inspired by the perfect circle of life, bringing us closer, step-by-step to the ultimate dream of Making Stuff Cleaner.
Broadcast Credits
Making Stuff: Cleaner
- Host
- David Pogue
- Written by
- Gary Glassman
- Directed by
- David Huntley
- Executive Producer
- Chris Schmidt
- Executive Producers
- for Powderhouse Productions
- Joel Olicker
Tug Yourgrau - Field Producer
- Doug Gordon
- Associate Producer
- Sonia Weinhaus
- Edited by
- Dickran H. Manoogian
- Additional Editing by
- Brian Cassin
Kristine Young Gaffney
Daniel McCabe - Director of Photography
- Gary Henoch
- Additional Photography
- Jason Longo
- Sound Recordists
- Bryan Apolinar
Jeff Archuleta
Mark Arees
Ed Chick
Giovanii Di Simone
Jim Meade
Phil Perkins
Juan Rodriguez
Steve Rykerd - Grips and Gaffers
- Ari Manin
Joshua Weinhaus - Production Assistant
- Daniel V. Parsons
- Music
- Lunch Special Music
- Animation
- Edgeworx, LLC
- Additional Animation
- Alan Waldo
halfadeer, vfx
Neoscape - Production Managers
- Diane Knox
Alexandra McHale - Post Production Supervisors
- Kevin Young
Michael Fallon - Assistant Editors
- Eric P. Gulliver
Peter Hyzak
Jim Fetela - Online Editor / Colorist
- Julie Kahn
- Audio Mix
- Heart Punch Studio, Inc
- Research
- Heather Scudellari
- Interns
- Katie Duffy
Nicole Jaques
Travis Kelley
Michael Ryan
Zach Vitale - For Powderhouse Productions
- Post Production Manager
- Melissa Walter Richards
- Senior Production Coordinator
- Carlin Corrigan
- VP of Production
- Daniel Miller
- Senior VP of Production and Post
- Robert Kirwan
- Senior VP of Sales and Development
- Seanbaker Carter
- Archival Material
- BlackLight Films / Footage Search
Corbis
Getty Images
Footage Provided by Thought Equity Motion
Footage courtesy The WPA Film Library
iStockphoto
Streamline Films, Inc. - Special Thanks
- Producers gratefully acknowledge the cooperation of the Materials Research Society.
- Richard A. Souza
Amy Moll
Kristin Bennett
Jerry Floro
Megan Frary
Kevin Jones
Tommie Kelley
Alex King
Aditi Risbud
Stephen Streiffer
Rick Vinci
Sandra DeVincent Wolf - Special Thanks
- U.S. Department of Energy's
Argonne National Laboratory
Big Dog Garage, LLC.
Ecovative Design
Waste Management, Inc.
Professor Stephen Sass, Cornell University - NOVA Series Graphics
- yU + co.
- NOVA Theme Music
- Walter Werzowa
John Luker
Musikvergnuegen, Inc. - Additional NOVA Theme Music
- Ray Loring
Rob Morsberger - Post Production Online Editor
- Michael H. Amundson
- Closed Captioning
- The Caption Center
- Publicity
- Eileen Campion
Victoria Louie
Karen Laverty - Marketing
- Steve Sears
- Researcher
- Kate Becker
- NOVA Administrator
- Kristen Sommerhalter
- Production Coordinator
- Linda Callahan
- Paralegal
- Sarah Erlandson
- Talent Relations
- Scott Kardel, Esq.
Janice Flood - Legal Counsel
- Susan Rosen
- Post Production Assistant
- Darcy Forlenza
- Associate Producer Post Production
- Patrick Carey
- Post Production Supervisor
- Regina O'Toole
- Post Production Editor
- Rebecca Nieto
- Post Production Manager
- Nathan Gunner
- Compliance Manager
- Linzy Emery
- Development Producer
- Pamela Rosenstein
- Supervising Producer
- Stephen Sweigart
- Business and Production Manager
- Jonathan Loewald
- Senior Producer and Project Director, Margret & Hans Rey / Curious George Producer
- Lisa Mirowitz
- Coordinating Producer
- Laurie Cahalane
- Senior Science Editor
- Evan Hadingham
- Senior Series Producer
- Melanie Wallace
- Executive Producer
- Howard Swartz
- Managing Director
- Alan Ritsko
- Senior Executive Producer
- Paula S. Apsell
Produced by Powderhouse Productions
A NOVA Production by Powderhouse Productions for WGBH
© 2011 WGBH Educational Foundation
All rights reserved
Image
- (David Pogue)
- ©WGBH/Mark Ostow, ©iStockphoto.com/Pinosub, Bottom right: ©iStockphoto.com
Participants
- Bill Dube
- Co-Owner of Killacycle
- Eva Hakansson
- Co-Owner of Killacycle
- Jay Keasling
- Joint BioEnergy Institute
- Peter Kendrigan
- Plant Manager, Waste Management
- Sam Kwa
- Technical Engineer, Yokohama
- Jay Leno
- Talk Show Host and Car Collector
- Nate Lewis
- Chemist, Caltech
- Deborah F. Mielewski
- Technical Leader, Ford
- David Pogue
- New York Times Tech Columnist
- Vilas Pol
- Argonne National Laboratory
- Don Sadoway
- Materials Scientist, MIT
- K R Sridhar
- Co-Founder and CEO, Bloom Energy
- Stephanie White
- Project Driveway Participant
- Richard Wool
- Chemical Engineer, University of Delaware
Education and Outreach Resources
Preview
Notice: Undefined index: preview_video_length in /home/nova/zend/application/templates/resources/multi-ep-pro.phtml on line 497
Full Program | 53:54
Full program available for streaming through ...
Watch Online
Full program available
Soon
Making Stuff: Smarter
Explore a new generation of ingenious materials, from clothes that monitor your mood to real-life invisibility cloaks. Airing August 28, 2013 at 9 pm on PBS Aired August 28, 2013 on PBS
- Originally aired 02.09.11
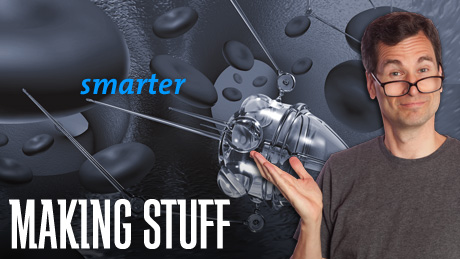
Program Description
Transcript
Making Stuff: Smarter
PBS Airdate: February 9, 2011
DAVID POGUE: Imagine a world with buildings that can ride out earthquakes; bacteria that make gasoline; tiny devices that repair individual cells, even DNA; gossamer threads strong enough to hold up a bridge; or an elevator to the stars.
These visions of the future are based in the discoveries of today, as a new science of materials emerges from the elemental building blocks of the universe, promising a future in which we can create virtually anything we want, atom by atom.
I'm David Pogue...
This wasn't in the contract!
...and I'm searching for the world's smartest materials, materials that sense and respond in ever more complex ways, giving us fantastic new abilities: an adhesive that lets you scamper up the side of a building;...
Could I not make myself a gecko costume that would let me climb walls?
...a plastic that heals itself like skin,...
These are bullet holes? Where's the bullets?
...and a new kind of material that makes objects invisible.
How far can we go in Making Stuff Smarter? Right now, on NOVA.
As the host of Making Stuff, I'm on a quest for the world's smartest materials. Lucky for me, that leads to Grand Bahama Island. But I soon learn this assignment isn't going to be "a day at the beach." NOVA wants me to take a swim with sharks.
Sharks are one of nature's greatest success stories, with ancestors reaching back to before the dinosaurs. When it comes to survival, it's easy to focus on their teeth, but their skin has led to a new material that can fight disease; an example of science taking ideas from the world's biggest materials lab, planet Earth.
For billions of years, Mother Nature's been experimenting, and that's given living things amazing abilities, like healing, flight and camouflage.
What can we learn from nature's ingenuity? Today, our teachers are the sharks, so I need to go where they live.
Should I be worried at all that I'm the only one on this crew who is not getting a suit of chainmail?
Tell my kids I love them.
As I approach the sharks, I can't help wondering: Was the crew just being friendly when they called me "old chum?"
But I'm here to examine the shark's skin, and to do that, I need to get even closer.
Diver Cristina Zenato has a plan. First, she attracts these Caribbean reef sharks using food and then reaches out to stroke one shark's nose.
For reasons that remain a scientific mystery, that puts the shark into a trance-like state called tonic immobility.
Cristina carries the shark over to me. Now, if I can just keep my hands away from those teeth, I can finally get a good look at one of the secrets of the shark's success, its skin.
Sharks are covered with scales called dermal denticles. Made from a tooth-like material, they're the reason the skin feels smooth in one direction, but like sandpaper in the other.
The denticles decrease drag and create less turbulence over the shark as it swims, a killer advantage.
Is there some evolutionary purpose to that?
CRISTINA ZENATO (Shark Expert):The shark being able to glide through the water, be silent, efficient and fast, all at the same time, without the prey really realizing it...to me, they're beautiful.
DAVID POGUE: But sharkskin denticles do more than enable a silent killer. They seem to prevent the growth of algae on the shark, and stealing that idea may save us from a lethal threat.
The overuse of antibiotics in medicine and farming has given rise to drug-resistant forms of common bacteria.
In some years, deadly superbugs, like M.R.S.A., mer´-sa, have killed more Americans than AIDS.
SHRAVANTHI REDDY (Chemical Engineer): The medical community, for so long, has been focused on killing as much of the bacteria as they can. Now, the interesting thing about bacteria is that you can't kill them all. You can kill 99 percent of them, but that one percent that you leave alive is the strongest one percent. And then you end up with resistant strains that can't be killed by traditional antibiotics.
DAVID POGUE: Shravanthi Reddy is the director of research for a company that makes this non-toxic plastic film called Sharklet™. Too tiny to see with the naked eye, its surface is covered in a repeating pattern of channels and pillars, each about a 20th the size of a human hair. It's called Sharklet because the pattern is modeled after the denticles of sharkskin, though it's far smaller.
Shravanthi has invited me to see what makes this seemingly ordinary piece of plastic a powerful medical weapon in our battle against bacteria.
SHRAVANTHI REDDY: We'll take our Sharklet film, which, you know, has the Sharklet pattern on it, and we've cut it into little small pieces. And we also cut up some smooth film that does not have the Sharklet pattern on it so we can compare.
DAVID POGUE: Next she adds bacteria to the dish and places it in an incubator for
...twenty four hours?
Finally, the results are in.
SHRAVANTHI REDDY: So, here's the really good comparison of the Sharklet surface and the smooth surface.
DAVID POGUE: So this, these are two samples treated the same way, same degree of magnification?
SHRAVANTHI REDDY: Yeah, yeah.
DAVID POGUE: On the smooth plastic, the bacteria have made themselves right at home, building a hefty colony.
And over here the Sharklet surface...
SHRAVANTHI REDDY: On the Sharklet surface you might see one or two cells inside the channels, but you don't see that big clumping the way you see it on the smooth surface. And it's really interesting, because there is no chemical difference between the two surfaces. It's the same material, no difference, other than this physical shape, alone.
DAVID POGUE: Sharklet is the brainchild of Tony Brennan, a biomaterials engineer at the University of Florida, in Gainesville. He studies how small creatures, like bacteria or algae, decide which surface to call home. He's tested other patterns, but, so far, only the denticle-inspired Sharklet has been effective.
TONY BRENNAN (Biomaterials Engineer): So it inhibits the bacteria. It doesn't kill them, to the best of our knowledge, but it, it just prevents them or slows them down substantially from establishing their colony. And bacteria love to be in colonies.
DAVID POGUE: Sharklet is already being tested in hospitals. It's been applied to doors, bedside rails, and other frequently touched surfaces. It may even be used on medical devices. If it's successful, it's an entirely new strategy for keeping bacteria at bay.
TONY BRENNAN: If we can slow the bacteria down, like all of our studies indicate, it's huge, because hospital-acquired infections represent one of the biggest costs we're dealing with in health care today.
DAVID POGUE: We think of sharks as the ultimate predators, but if the bacteria-evading principles of Sharklet hold, we may soon owe them our lives.
Sharklet contains a key lesson for scientists making stuff smarter.
Like chefs in a kitchen, we tend to think of materials in terms of their ingredients, but Sharklet's secret isn't what it's made of, it's the shape of its surface. In fact, some of nature's most ingenious tricks depend on surface structures built on a really tiny scale, far smaller than a human hair.
The iridescent color of this butterfly comes from the way light scatters across the textured surface of its wing, not because of any pigment.
This lotus leaf is self-cleaning, thanks to tiny needle-like protrusions that repel water. The droplets roll off the leaf taking the dirt with them.
And this desert beetle has tiny bumps on its back that collect moisture from the air, until just the right breeze blows the droplets down to its mouth.
In each case, nature has come up with something new just by manipulating the surface of a material on a very small scale. Now, scientists are trying to do the same thing, to create new powers, maybe even super powers, like Spiderman's.
Now, in case you aren't that familiar with Spidey, he depends on tiny structures, little hooks on the tips of his fingers that let him climb walls. Can we create a material, a smart adhesive, that will let us do the same?
Turns out the best bet for that doesn't come from a spider, but from another natural wonder, the gecko. It has a nearly limitless ability to climb. The weird part is that gecko feet don't feel sticky to the touch at all, yet somehow they stick and then unstick with ease, up to 15 times a second.
Now imagine if a human could to that.
But first we need to figure out the gecko's secret.
Kellar Autumn, from Lewis and Clark College, in Portland Oregon, did just that. He found the answer in the sheer number and design of the hairs on the gecko's feet.
KELLAR AUTUMN (Biologist): Geckos have millions of microscopic hairs on their toes. Of course we can't see this with our naked eye, because each hair is only one-tenth the size of a human hair, and each of those hairs branched down to billions of little split ends. And they can make such close contact with the surface that weak intermolecular forces can begin to add up to something really strong.
DAVID POGUE: Turns out geckos exploit something called the Van der Waals force.
If you think of an atom as a dancing couple, when you bring two atoms into very close contact, part of one atom can get attracted to part of the other. That very weak bond is the Van der Waals force, and it sticks atoms together. Proximity is the key, but bringing two materials that near each other is harder than you'd think.
KELLAR AUTUMN: When I put my hand on this table, I have an apparent contact area, which is just the surface area of my hand. But the true contact area is probably a ten-thousandth of that.
The surface of my hand is like a molecular mountain range coming down on a desert landscape. So only the tips of your molecules ever interact with the surface.
DAVID POGUE: But when a gecko places its foot against a wall, all those branching hairs are like a forest pressed against a desert. And when the gecko climbs, it drags its foot down, bringing not just the tips but the sides of all those hairs against the surface.
With up to half the area of the gecko's foot in close contact with the wall, the Van Der Waals forces really add up.
And we can measure just how powerful all that gecko hair can be.
KELLAR AUTUMN: What we measured really surprised us because the force was so large that a gecko's worth of hair, stuck at once, could lift about 250 pounds.
DAVID POGUE: That's a lot of stick in a very little package.
But it unsticks just as easily, when the gecko peels its toes off the surface.
KELLAR AUTUMN: This is an adhesive that's sticky when and where the gecko wants it to be, but it's actually not sticky the rest of the time: a smart adhesive.
DAVID POGUE: You know what? It just asked me if I want to save 15 percent or more on my car insurance.
So now that we understand gecko adhesion, can scientists match it?
I head over to Stanford, in Palo Alto, California, to visit Mark Cutkosky, who's building a climbing robot based on gecko principles.
MARK CUTKOSKY (Mechanical Engineer): Our motivation is that we want robots to go anywhere. So, we've had robots that can run along the ground for some time; the unmet challenge was to get robots that could go on vertical services, especially smooth ones.
DAVID POGUE: Imagine a world where robots could climb anywhere. Everything, from everyday tasks, like window washing, to specialized ones, like emergency rescue or surveillance, would change.
The key gecko feature on this robot is the material used for the pads on its feet. They're made from silicone rubber. Tiny wedges on the upper surface of the pad use the same gecko principle of directional adhesion, adhering when dragged down because of the close contact, but the rest of the time not sticky.
MARK CUTKOSKY: This is one pad on a little suspension with the weight about 200 grams below. If you just touch it to the surface it's not sticky at all, but if...
DAVID POGUE: Not at all.
MARK CUTKOSKY: ...if you let the weight hold it,...
DAVID POGUE: Oh, man!
MARK CUTKOSKY:...it sticks perfectly.
DAVID POGUE: So when the weight is pulling down, that's the directional thing you were talking about?
MARK CUTKOSKY: Exactly. And then, to get it off, you actually have to remove the weight, and then it will lift right off.
DAVID POGUE: So it's quite firm now but if I lift up, oh, my gosh, it's like the electricity was turned off.
MARK CUTKOSKY: That's directional adhesion.
DAVID POGUE: And that's what the real gecko does?
MARK CUTKOSKY: And that's what the gecko does. And, in fact, if you've ever seen a gecko going headfirst down a wall, you'll see that it's turned its rear feet backwards. And it has to, otherwise it wouldn't stick.
DAVID POGUE: Time to see the gecko in action: the lab's most recent creation, Stickybot III.
MARK CUTKOSKY: This is a ground granite slab, like a kitchen countertop.
DAVID POGUE: Okay.
MARK CUTKOSKY: So, it's too smooth to use something like little hooks or spines, so we really have to rely on the adhesion.
DAVID POGUE: Start the gecko!
Pretty impressive; and especially when they show me a piece that supports 45 pounds.
I start having my own ideas.
If had gloves made of this stuff, plus socks, could I not make myself a gecko costume that would let me climb walls?
MARK CUTKOSKY: You're not designed to be a gecko, you'll get tired, but, but you should stick.
DAVID POGUE: They say gecko adhesives would be useful anywhere you need extra grippiness, you know: tires or surgical bandages or sports equipment. But, come on, we all know the real reason to develop gecko adhesives. So you can do this!
Okay, I'm busted. Nobody has gecko gloves this good, at least nobody who's talking (military) but they're coming. Mark my words.
Until then, Hollywood's Spiderman has got the job.
Gecko adhesives and Sharklet mimic actual structures found in nature, but can we make stuff even smarter by building into materials life-like reactions, such as healing?
Even if I just cut myself while shaving—ow!—my body initiates an emergency response. Immediately, it constricts broken blood vessels to lessen the bleeding. Platelets clump together to plug up the wound.
That's just the beginning of a miraculous cascade of actions to repair the damage.
Can we design materials that can do that? Heal themselves?
Iraq, 2004: the U.S. military faced a new and devastating threat in its battle with insurgents.
CHAD KNOWLES (Iraq War Veteran): The fuel tankers in theater were actually being shot at by the insurgents, creating holes that would actually leak a lot of the fuel out, creating a problem of safety for the soldiers.
DAVID POGUE: The tankers didn't explode like they do in the movies, but with fuel spilling out, setting them on fire didn't take much.
The Pentagon urgently sought a solution. A company in Salem, Oregon, High Impact Technology, offered up a new smart material that takes its cues from biology. I'm here to see how it works.
Here's a standard fuel tank that would be used on a military truck.
And here's one with High Impact Technology's unique coating called "Battle Jacket."
RUSS MONK (Director of Operations, High Impact Technology): This is a self-healing, self-sealing coating that was developed for ballistic events in theater.
DAVID POGUE: Is that military-ese for bullet holes?
RUSS MONK: Exactly.
DAVID POGUE: The gun used for the test is the weapon of choice in Iraq, the AK-47.
[Sound of gunshots.]
Oh, yeah!
[Sound of gunshots.]
Target terminated.
The threat is obvious. Just one bullet hole will spill 150 gallons an hour, but what happens next is so surprising, it's hard to believe.
Let's take a look. Exhibit A: three nasty bullet holes leaking fuel, ready for the enemy to light with a match and blow up the truck.
TOM OHNSTAD (Director of Engineering, High Impact Technology): Yes, sir.
DAVID POGUE: Exhibit B: Oh, he missed! Oh, is this what we're talking about?
TOM OHNSTAD: That is it.
DAVID POGUE: These are bullet holes?
RUSS MONK: That's actually the black powder off the bullet that actually made the mark.
DAVID POGUE: No!
TOM OHNSTAD: That is a telltale sign of a round going through the, uh...coating is now, it immediately started to self-seal.
DAVID POGUE: Where's the bullets?
RUSS MONK: They're in the tank.
DAVID POGUE: They're inside?
RUSS MONK: They actually just drop to the bottom, and you pick them up with the filters.
DAVID POGUE: Ingenious!
It all happens so fast that even with this high-speed camera, running at five thousand frames a second, you can barely see it.
There's the bullet; there's the hole, or what was one.
What kind of stuff does that?
Back at the lab, the Battle Jacket guys break it down for me.
If I had to guess, I'd say this contraption is spraying your magic coating onto the tanks in here.
RUSS MONK: Absolutely correct.
DAVID POGUE: It's like the world's biggest spray-tanning salon.
RUSS MONK: And when that is done, it looks like this.
DAVID POGUE: So this a cross-section of the tank wall, right?
RUSS MONK: And the three shots you did today, that's what it looks like inside the tank.
DAVID POGUE: Oh, man. So that would have leaked out big time.
RUSS MONK: That's correct.
DAVID POGUE: Battle Jacket goes on in three distinct layers.
The inner and outer layers are the same material, a specially formulated plastic that can stretch to more than double its size. When the bullet tears through the coating and the tank wall, the plastic stretches around it and then snaps shut, leaving a pinhole-sized leak.
The thin middle layer does the sealing. It contains tiny plastic beads that absorb the leaking fuel.
RUSS MONK: It absorbs it and starts swelling. It'll grow up to 20 times. It's like a cork that actually opens up, and it locks down that wound. So you get the self-healing from the coating, the self-sealing from the chemistry.
DAVID POGUE: There's one last key element: the physics of the fuel. I get to see that in a special test tank with a Plexiglas® side.
RUSS MONK: Okay, David, whenever you're ready.
[Sound of gunshot.]
DAVID POGUE: Here's the bullet entering. The impact creates a shockwave inside the tank that actually pushes some of the fuel out the bullet hole, starting the chemical reaction that seals it shut.
The arrival of Battle Jacket in Iraq, in 2005, changed the game there.
CHAD KNOWLES: The strategy of setting the tanks on fire has kind of gone away. I think, predominantly, because the insurgents really don't understand, they don't think they're hitting the tank. That's how successful it's been.
It's a very elegant solution.
DAVID POGUE: Battle Jacket is just the beginning.
Imagine a smarter world where cars repair their own dents, bridges repair their own rust or concrete repairs its own cracks. Self-healing is a powerful idea, invented by evolution, and now, thanks to materials science, shared with the world of stuff.
The only thing that's bothering me is that we only shot three pathetic bullets. Don't those guns hold more than that?
TOM OHNSTAD: They do.
DAVID POGUE: I mean, this is NOVA. Let's finish big.
TOM OHNSTAD: Let's finish big.
DAVID POGUE: Gentlemen, commence fire, please!
[Sound of gunshots.]
That's better!
Battle Jacket is a smart product, but what if you wanted an even smarter material, one with a more varied response? To find stuff like that, we're better off out of the lab and at the movies.
The T-1000 from Terminator 2 could have won an Oscar for "best adapting material," because this liquid guy can sense, respond and even self-heal. It's the material itself that does things. He's a life-like fluid that's very, very smart.
Okay, that's science fiction, but in the search for smarter materials, engineers have taken a hard look at some liquids with very strange behaviors. They're called non-Newtonian fluids.
I travel to North Carolina, to the Lord Corporation, which manufactures one, but when I arrive, I have a burning question for Engineer Lynn Yanyo.
Forget non-Newtonian, what's a Newtonian fluid? She offers to show me one.
LYNN YANYO (Polymer Engineer): This is a Newtonian fluid. Take a look at that.
DAVID POGUE: Turns out this Newtonian fluid is water.
What makes it Newtonian? I've never thought of it as Newtonian.
LYNN YANYO: It makes it Newtonian because Isaac Newton discovered that there's a relationship between how hard it is to move it and the viscosity.
DAVID POGUE: Viscosity meaning thickness?
LYNN YANYO: The thickness, resistance to flow.
DAVID POGUE: When you try to move something through water, the resistance is directly proportional to how fast you move it: twice as fast is twice as hard.
Now, that's kind of what you'd expect, but amazingly that's not true for lots of other fluids, the non-Newtonian ones, like ketchup. Ever wonder why it's so hard to get it out of a glass bottle?
That's because, unlike water, it thickens at rest, its molecules creating a weak structure that resists flowing.
Yes, I remember this from my hamburger days. Ladies and gentleman, it does not flow! Lynn is staking her scientific reputation and her hairdo on the non-flowingness of ketchup.
But if you can get it started, that structure breaks down, and the ketchup thins and flows.
Here's another non-Newtonian fluid, in fact, a lot of it.
Oh, here it comes, definitely a liquid.
This cornstarch and water mixture is known as Oobleck. The word comes from an old Doctor Seuss story. Oobleck dramatically changes its viscosity, or thickness, depending on how fast you try to move it.
Keep the action soft and it flows like a liquid, but hit it hard and it's solid enough that you can run across it.
This liquid, when I squeeze it tight, turns into a rock and then when I let go it turns back into a liquid, what is happening?
LYNN YANYO: We like to call this, the Three Stooges effect.
DAVID POGUE: That's not the scientific term! What do you mean the Three Stooges effect?
LYNN YANYO: Well, you know when the Three Stooges tried to get through the doorway and they couldn't? The corn-starch doesn't want to get out of its own way. So, when you push on it really hard, it can't move out of the way fast enough.
And if you hit it really slowly, you can go right through it like a liquid.
DAVID POGUE: So, it's a liquisolid. You know, it depends on the pressure, the speed or something.
LYNN YANYO: It depends on the speed at which you try to move anything through it.
DAVID POGUE: Oobleck's a lot of fun. Be sure to fill your neighbor's pool with it.
Oh, it's got me!
But non-Newtonian fluids designed into the right system can save your life. Imagine a material that can adjust its thickness to absorb the seismic shakes of earthquakes or dampen the vibrations caused by wind that can pull a bridge apart.
That's what the non-Newtonian fluid Lynn has in her hand can do.
LYNN YANYO: So, the interesting thing about this is that it's very responsive to a magnetic field, and it's a lot like Oobleck. Take this spoon and scrape around in there.
DAVID POGUE: Okay. Oh, man, that is unbelievable, it's cement! It's...
LYNN YANYO: So now, scoop some of that up, and just take it out of the magnetic field by lifting it up.
DAVID POGUE: Mmm, it's...oh, no way!
This is like X-Men stuff.
So, it's a magnetic liquid.
LYNN YANYO: Mm-hmm, we call this magneto-rheological fluid.
DAVID POGUE: Do you got a shorter nickname?
LYNN YANYO: M.R.
DAVID POGUE: M.R. fluid, can I call it Mr. Fluid?
LYNN YANYO: No.
DAVID POGUE: A typical M.R. fluid consists of tiny iron particles suspended in a fluid like oil.
Without a magnetic field, the liquid flows freely, but add a magnetic field, and the metal particles line up, increasing the fluid's thickness.
Lord puts that variable viscosity to work in devices like shock absorbers.
LYNN YANYO: And then there's another suspension that's larger, and that's for really heavy-duty vehicles.
DAVID POGUE: Heavy-duty vehicles like Humvees. For the military, a smooth ride isn't about luxury.
How well a vehicle handles bumps determines how fast it can safely travel, as well as how fatigued its passengers become, both life and death issues on the battlefield.
Out here in the woods, I'm going to see just what kind of a difference using a smart material can make in a Humvee's performance.
Good heavens.
LYNN YANYO: Well, here you are. This is your ride, and for this first ride we have this military Humvee, and it is just retrofitted with the conventional shocks that you would have when this was used out in the field.
DAVID POGUE: A typical shock absorber is built around a piston filled with oil. When the piston moves down, it forces the oil from one chamber to another through small holes.
The thickness of the oil and the size of the holes determine how much force that takes. If neither varies, the shock is a one-size-fits-all dampening solution, no matter how bumpy the road is.
How do you make this seat recline anyway?
Jeez! Oh, my god! That was pretty bouncy. You should sell tickets to this thing.
For round two, the Humvee gets the smart shock absorbers. They also use a piston design, but they add M.R. fluid, full of iron particles, and an electromagnet where the fluid flows through the holes.
A computer controls the electromagnet in real time, varying the viscosity of the M.R. fluid. This system adjusts how much force is needed to move the piston in response to the bumpiness of the road.
That makes the shock absorber tunable. It can react nearly instantaneously to different size vibrations. And that's very smart.
Oh, this is nothing. How do I adjust the A.C.?
So, you're telling me that was the exact same speed?
DRIVER: Exact same speed.
DAVID POGUE: Well, I can tell you, if I were a soldier, I'd vote for these shock absorbers.
LYNN YANYO: Oh, yeah. You can see why that's a huge difference for those guys, if they have to travel 25 miles in that. And the vehicles will last longer.
Don't forget your seatbelt!
DAVID POGUE: Yeah, yeah.
The abilities of smart fluids scale far beyond Humvees. Engineers see a big future for them in bridge construction, to squelch vibrations caused by wind and bad weather. And even for use in buildings to counteract the awesome power of earthquakes, like a steadying hand.
Sophisticated smart materials can react to outside forces to protect bridges and buildings, but they can be even more lifelike, allowing us to realize one of humanity's oldest dreams?
The flying ability of birds has always captured the human imagination.
But when it comes to flying, birds have us beat on a bunch of levels.
Sure we can fly in a hang glider and gain some of the sense of how a bird soars. Or we can build jet fighters that can dive from the sky, the way a bird can tuck its wings in and shoot toward Earth. But a bird does all that and more thanks to an elegant feature that's the envy of aircraft designers: a flexible, shape-changing wing.
Ironically, heavier-than-air flight started out using a more bird-like wing than we use today. The Wright brothers employed a steering system of wires and pulleys that actually bent the wings of the Wright Flyer to control its direction, not unlike the way a bird steers by altering its wing shape. But as planes became bigger, designers needed stiffer materials and hinged parts for flight control. The legacy of that is the mechanical complexity of your average airliner wing.
It's got ailerons, flaps, slats and airbrakes. That's a lot of motors, hinges and moving parts, all of which disrupt airflow and add weight, a big loss in efficiency.
But imagine if all that shape-changing could be done the way a bird does it, just by bending the wings. That may sound way out, but for more than a decade at Virginia Tech, in Blacksburg, Virginia, Dan Inman has been exploring just that kind of shape-changing wing, using smart materials.
Today's the first test flight of this experimental remote control aircraft built by students in his lab.
DANIEL INMAN (Materials Scientist): We're trying to make a shape-changing wing, try to imitate, uh, more of what a bird would do, by having the wings bend, rather than having a discrete flap, like in a normal aircraft. And so this doesn't. It has a smooth surface.
DAVID POGUE: Inman can ditch the flaps and the various cables and motors to control them, by bending the wing using a smart material embedded in those plastic strips. It's called a piezoelectric ceramic.
That's a mouthful, but these materials change their shape in response to an electric charge. In this case, that's supplied by batteries on the plane and controlled electronically from the ground.
Now this is going to be the very first flight in this configuration, right?
DANIEL INMAN: Absolutely.
DAVID POGUE: Have you considered the fact that you're on a high definition national television broadcast and it could flop?
DANIEL INMAN: Absolutely.
DAVID POGUE: So this is it? The maiden flight?
And flop it does, due to a faulty wire.
But you can't keep the Virginia Tech Hokies down. One spare fuselage and an hour later, they're back for round two.
STUDENTS: One, two, three, Hokies!
DAVID POGUE: She flies, she flies!
Second time's the charm.
And chock up a big win for Birdman Inman and his team.
For the pilot, learning how to fly using the new wings is like learning how to a walk, but it's easy to see the bird in the plane's acrobatics.
With engineers putting more avian back into aviation, one day you may look out your airliner's window to see smart materials bending the trailing edge of the wing.
You might even see the entire shape of the wing altering in flight, thanks to some metals with great memories.
This wire NOVA logo is made from a nickel and titanium alloy. The metal was invented in the late fifties for use in missile nose cones, but then, by accident, it was discovered to have an astonishing quality.
If I stretch out this wire and then apply a little heat, it snaps back to its original size and shape. Scientists call materials like this "shape memory alloys," or S.M.A.s.
But they might as well call them artificial muscles. That's how they're being put to work here. This jellyfish robot from Virginia Tech swims without any kind of motor. In a design inspired by real jellyfish, it's propelled by the contractions of an artificial muscle, made of metal, embedded in its silicone bell. Electric current heats the material to trigger the action. Eventually a small battery will provide the power.
The goal of this work, paid for by the Navy, is a motion-detecting buoy that's inconspicuous.
DANIEL INMAN: If it looks like a jellyfish, then maybe someone will think it is a jellyfish and not bother it.
DAVID POGUE: Oh, I see. So we could actually spy on the bad guys.
"Wait! Who goes there? Oh, it's just a jellyfish."
Even beyond artificial muscle, shape-shifting metals and plastics may be the shape of things to come.
Imagine if your watch could morph into your cell phone, or your family sedan could turn into a roadster.
But today, shape memory alloys are saving lives. This is a stent. It's designed to keeps an artery open. Surgeons can shrink it down for insertion and then the heat of the body, like this hot water, expands it into place. Smart: just one example of how new materials have revolutionized the world of medicine.
That's a revolution that's been decades in the making. I head to Massachusetts to see a professor at M.I.T. who runs the largest bioengineering lab in the world.
For many, chemical engineer Bob Langer personifies the new role of material science in medicine.
Wow, this is your office?
ROBERT LANGER: Yeah, yes it is.
DAVID POGUE: Too bad nobody's recognized your work.
ROBERT LANGER: Well, I've been lucky, but it didn't start out that way. I mean, you know, when I started working, I think for the first 10 or 15 years, nobody cared about what we were doing, at all.
DAVID POGUE: After graduating from M.I.T. in the 70s, Bob entered an unlikely field, cancer research, an area with few, if any, chemical engineers.
At that time, medical advances depended on whatever was at hand.
ROBERT LANGER: What doctors would do is, they would go to their house, they'd find an object that kind of resembled say the organ or tissue that they were trying to fix, and then they'd use it in a patient.
DAVID POGUE: Doctors cobbled together solutions. Sausage casings became the basis for dialysis machines; squishy mattress stuffing was put inside breast implants; and the elastic in ladies' girdles was used for artificial hearts.
Instead of this scavenger hunt, Langer took an engineering approach.
ROBERT LANGER: Rather than pick something from your house, why can't you ask the design question, "What do you really want, from an engineering standpoint, chemistry standpoint, biology standpoint?" And then, "Could we synthesize it?"
DAVID POGUE: Over the years, Langer's approach has paid off.
Some of his biggest breakthroughs have been in drug delivery. He invented plastic implants that can release a drug at a steady rate for up to five years.
So how do you do that? How do you control the rate and the duration?
ROBERT LANGER: Well, there are several ways to do it. It could have what we call tortuosity in it, winding paths. When you make these winding paths in a piece of plastic, it'll take a long time for the molecules to get through.
DAVID POGUE: A drug molecule encased in Langer's plastic is like a car trying leave a city without a map.
In Manhattan, the grid system makes that fairly easy. Just going straight takes you to the outer edge. That's like a low tortuosity fast-release plastic.
But a high tortuosity delayed-release plastic is like Boston. With its winding streets, you might find yourself lost for days, months, maybe even years.
So are these smart materials you're working with?
ROBERT LANGER: They are. I'd say they're the first generation of smart materials, because they're really aimed to deliver at the right rate, to degrade at the right rate. So, yeah, I think they're pretty smart.
DAVID POGUE: Langer's second generation, still in the research phase, takes an even smarter approach.
Traditional intravenous chemotherapy "nukes" the body with toxic chemicals to kill cancer cells. The problem is that the required dose also harms a lot of healthy tissue.
Langer's brought a new weapon to the battle. Tiny drug particles, nano-sized—that's billionths of a meter—to be sent, special delivery, to just the cancer cells.
ROBERT LANGER: Targeted chemotherapy, where you could take the nuking material, so to speak, put it in the nanoparticle, and have the nanoparticle direct it right to the tumor, and not other places in the body.
DAVID POGUE: How does that work? How can it know what a cancer cell is?
ROBERT LANGER: It's actually very challenging. It's really developing a way to decorate the outside of it, with just the right combination of materials.
DAVID POGUE: He starts with a nano-particle of anti-cancer drug. That gets encased in a plastic that releases the drug over time. That, in turn, gets a special wrapping that disguises the package as a water molecule to fool the body's immune system.
And last, but not least, the address where it should be delivered: a key that will only fit the lock of cancer cells.
This is just one slice of Langer's work at the intersection of materials and medicine. He's got 700 patents and counting, in drug delivery, tissue engineering and even hair products.
ROBERT LANGER: Robert Frost said it very well in his poem, you know? I ended up taking "the road not taken," and I think it's a path that now many more people are taking and I think it's a path where engineers and materials scientists can just do a lot of good for the world, and so I think it's a wonderful path.
DAVID POGUE: Forty years ago smart materials barely existed. Now not only can they mimic nature, they can move radically beyond it to accomplish what has always seemed impossible.
Take camouflage. Nature is full of animals that have evolved to stay hidden. The lionfish has a fixed appearance that allows it to fade into a specific environment, but the octopus can change its coloring, to blend into different backgrounds.
Now, new discoveries in materials offer us an approach to hiding that nature's never found. Why not just cloak yourself in invisibility?
The road to just such a cloak begins with Sir John Pendry, a theoretical physicist and mathematician at Imperial College, London. He's come up with new metamaterials, "meta" meaning "beyond." This one is made of plastic, encasing tiny copper rings. It's an experimental model, but someday, metamaterials like it may influence visible light in mind-blowing ways.
JOHN PENDRY (Theoretical Physicist): I produced the design and a formula for, for hiding something. We, we said "If you want to completely...make something completely invisible, then this is what you do."
It started off a huge research program.
DAVID POGUE: I travel to Duke University, in North Carolina, to talk with one of Pendry's collaborators on the invisibility cloak and the first to actually build one.
Thanks to the movies, like H.G. Well's Invisible Man, I thought I knew what to expect.
You're the guy developing the invisibility cloak?
DAVID SMITH (Electrical Engineer): That's right.
DAVID POGUE: I have to say, it works amazingly well. I can't even see you.
DAVID SMITH: Well, actually, I'm over here.
DAVID POGUE: Oh, sorry.
Maybe David Smith has something more like that Harry Potter movie.
DANIEL RADCLIFFE (As Harry Potter/Harry Potter and the Sorcerer's Stone/Film Clip): My body's gone!
RUPERT GRINT (As Ron Weasley/Harry Potter and the Sorcerer's Stone/Film Clip): I know what that is. That's an invisibility cloak!
DAVID POGUE: Heck! Even I can get into that act.
As a television professional, I use a little something we like to call the green screen.
Woooo! I'm beheaded.
All this techno-trickery does make one thing clear: making something invisible is really about trying to make what's behind an object visible, bringing the reflected light of the background around the object, like water flowing around a rock in a stream.
DAVID SMITH: So, this should probably strike you, just from the geometry, as to what its function is. So, the hidden region is right here. A wave comes in.
DAVID POGUE: Anywhere in here?
DAVID SMITH: Anywhere in there, that's right.
DAVID POGUE: Oh, we're talking big stuff. I could put a piece of cheese...
DAVID SMITH: Right.
DAVID POGUE: ...or a marble...
DAVID SMITH: Right.
DAVID POGUE: Oh, wow.
DAVID SMITH: And, uh, you're waves could come in and this effected material causes them to get moved like this and then restored on the other side.
DAVID POGUE: There is a catch. Visible light waves, from red to blue, are just a narrow slice of the electromagnetic spectrum. Smith is working in a different slice, where the wavelengths are longer, in the microwave region.
That's why his invisibility cloak is, well, visible.
It's not working yet, though, I can see right through it.
DAVID SMITH: You're looking with the wrong wavelengths.
DAVID POGUE: Oh right! Don't think about visible waves, think about...okay.
DAVID SMITH: Microwaves.
DAVID POGUE: Time to test the cloak in this—basically a giant microwave oven—and I get to choose what to hide.
You know what? This is in the spirit of that fabled lady, when microwave ovens first came out, she washed her poodle and put it in the microwave to dry it. Yeah, except, uh, actually, in this case it would have protected the poodle, right?
DAVID SMITH: Would've protected the poodle.
DAVID POGUE: The microwaves would have gone right around it, and the poodle would not have been cooked.
DAVID SMITH: That's right.
DAVID POGUE: With the frog in place, Smith starts the test.
Here's a graphic display of what's going on in the tester, looking down from above. A microwave generator on the left sends out test waves. If there's no object in the tester, they cleanly pass from left to right. On the other hand, if my frog sat, uncloaked, in the middle, it would scatter the waves, disrupting the pattern.
Now, if my frog had a perfect cloak, the waves would pass around it, cleanly emitted on the other side, without any change.
Here's Smith's actual result of the test. It isn't perfect—you can see the waves aren't the same after hitting the cloak—but it's getting there.
So, it looks like it's actually, sort of, working.
DAVID SMITH: It's working. If you were sitting here, what you would see is no distortion, you'd see, basically, a reduction in intensity, but you wouldn't be able to make out what was being scattered in here.
DAVID POGUE: You wouldn't...
DAVID SMITH: So you wouldn't be able to see your frog.
DAVID POGUE: ...even though you're looking right at it?
DAVID SMITH: Right.
DAVID POGUE: With your microwave-sensitive eyes.
DAVID SMITH: That's right.
DAVID POGUE: Well now, what about the frog, can the frog see him?
DAVID SMITH: No, the frog can't see him.
JOHN PENDRY: If you're inside one of these invisibility spheres, you wouldn't be able to see outside, and if you looked at the walls, what you would see would be a reflection of yourself. From the inside, the appearance is, is as of a mirror.
DAVID POGUE: Of course, that's not a problem yet. Scientists haven't created a cloak that...
...works with visible light, though they're getting ever closer.
And invisibility is just one application. The promise of metamaterials is a revolution in our manipulation of light. We may see new powerful lenses, that can focus on something as small as a virus attacking a cell, or new technologies that scan for cancer or hidden explosives.
It's a new frontier and, like human imagination, it has no limits, yet. With all our technology and materials, it's easy to think we're the planet's best inventors, but life has been experimenting with the raw materials of earth for far longer.
Billions of years of evolution have created a vast array of plants and animals with amazing abilities of their own. As our understanding of biology and our materials deepens, a new world has opened up, one where nature's ingenuity and human ingenuity can combine.
And that's Making Stuff Smarter.
Broadcast Credits
Making Stuff: Smarter
- Host
- David Pogue
- Written, Produced and Directed By
- Daniel Mccabe
- Executive Producer
- Chris Schmidt
- Executive Producers
- For Powderhouse Productions
- Joel Olicker
Tug Yourgrau - Associate Producer
- Minna Kane
- Edited By
- Daniel Mccabe
Justin Vaida - Additional Editing By
- Brian Cassin
Jean Dunoyer - Directors of Photography
- Gary Henoch
Stephen Mccarthy - Additional Photography
- Dennis Boni
Robert Burns
Tim Cragg
Joe Livolsi - Underwater Camera
- Eddy Raphael
- Sound Recordists
- Frank Collins
Philip Perkins
David Wade
Greg Hinnen
Anna Rieke
Glen Abbey
John Cameron
Tyler B. Stephens
Adam Prescod
Geoff Gann
Kevin Cook
Glen Ackers
Mark Arees
Dave C. Manahan - Grips and Gaffers
- Jesse Hubbell
Ari Manin
Joshua Weinhaus
Brian Patriacca - Production Assistant
- Daniel V. Parsons
- Music
- Lunch Special Music
- Animation
- Edgeworx, Llc
- Additional Animation
- halfadeer, vfx
Pixeldust - Production Managers
- Alexandra Mchale
Diane Knox - Post Production Supervisors
- Kevin Young
Michael Fallon - Assistant Editors
- Eric P. Gulliver
Peter Hyzak
Jim Fetela - Online Editor / Colorist
- Julie Kahn
- Audio Mix
- Heart Punch Studio, Inc
- Interns
- Katie Duffy
Nicole Jaques
Travis Kelley
Michael Ryan
Zach Vitale - For Powderhouse Productions
- Post Production Manager
- Melissa Walter Richards
- Senior Production Coordinator
- Carlin Corrigan
- Vp of Production
- Daniel Miller
- Senior VP of Production and Post
- Robert Kirwan
- Senior VP of Sales and Development
- Seanbaker Carter
- Archival Material
- Daniel Zatz / Footage Search
Footage Provided By Thought Equity Motion
Getty Images
iStockphoto
NASA
Nature Publishing Group
Photolibrary
Pond5
Streamline Films, Inc. - Special Thanks
- Producers Gratefully Acknowledge the Cooperation of the Materials Research Society.
- Richard A. Souza
Amy Moll
Kristin Bennett
Jerry Floro
Megan Frary
Kevin Jones
Tommie Kelley
Alex King
Aditi Risbud
Stephen Streiffer
Rick Vinci
Sandra Devincent Wolf - Special Thanks
- Wallaby Ranch
Florida Museum of Naturalhistory
Professor Stephen Sass, Cornell University - NOVA Series Graphics
- yU + Co.
- NOVA Theme Music
- Walter Werzowa
John Luker
Musikvergnuegen, Inc. - Additional NOVA Theme Music
- Ray Loring
Rob Morsberger - Post Production Online Editor
- Michael H. Amundson
- Closed Captioning
- the Caption Center
- Publicity
- Eileen Campion
Victoria Louie
Karen Laverty - Marketing
- Steve Sears
- Researcher
- Kate Becker
- Novaadministrator
- Kristen Sommerhalter
- Production Coordinator
- Linda Callahan
- Paralegal
- Sarah Erlandson
- Talent Relations
- Scott Kardel, Esq.
Janice Flood - Legal Counsel
- Susan Rosen
- Associate Producer Post Production
- Patrick Carey
- Post Production Supervisor
- Regina O'Toole
- Post Production Editor
- Rebecca Nieto
- Post Production Manager
- Nathan Gunner
- Compliance Manager
- Linzy Emery
- Development Producer
- Pamela Rosenstein
David Condon - Supervising Producer
- Stephen Sweigart
- Business and Production Manager
- Jonathan Loewald
- Senior Producer and Project Director, Margret &Amp; Hans Rey / Curious George Producer
- Lisa Mirowitz
- Coordinating Producer
- Laurie Cahalane
- Senior Science Editor
- Evan Hadingham
- Senior Series Producer
- Melanie Wallace
- Executive Producer
- Howard Swartz
- Managing Director
- Alan Ritsko
- Senior Executive Producer
- Paula S. Apsell
Produced by Powderhouse Productions
A NOVA Production by Powderhouse Productions for WGBH
© 2011 WGBH Educational Foundation
All Rights Reserved
Image
- (David Pogue)
- ©WGBH/Mark Ostow, ©iStockphoto.com/Guillermo Lobo
Participants
- Kellar Autumn
- Biologist
- Tony Brennan
- Biomaterials Engineer
- Mark Cutkosky
- Mechanical Engineer
- Daniel Inman
- Materials Scientist
- Chad Knowles
- Iraq War Veteran
- Bob Langer
- Chemical Engineer
- Russ Monk
- Dir. of Operations, H.I.T.
- Tom Ohnstad
- Dir. of Engineering, H.I.T.
- John Pendry
- Theoretical Physicist
- David Pogue
- New York Times Tech Columnist
- Shravanthi Reddy
- Chemical Engineer
- David Smith
- Electrical Engineer
- Lynn Yanyo
- Polymer Engineer
- Cristina Zenato
- Shark Expert
Education and Outreach Resources
Preview
Notice: Undefined index: preview_video_length in /home/nova/zend/application/templates/resources/multi-ep-pro.phtml on line 497
Full Program | 53:24
Full program available for streaming through ...
Watch Online
Full program available
Soon