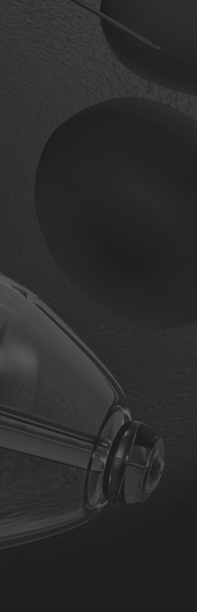
Making Stuff: Smarter
Explore a new generation of ingenious materials, from clothes that monitor your mood to real-life invisibility cloaks. Airing August 28, 2013 at 9 pm on PBS Aired August 28, 2013 on PBS
- Originally aired 02.09.11
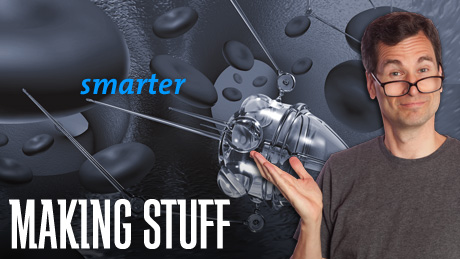
Program Description
Transcript
Making Stuff: Smarter
PBS Airdate: February 9, 2011
DAVID POGUE: Imagine a world with buildings that can ride out earthquakes; bacteria that make gasoline; tiny devices that repair individual cells, even DNA; gossamer threads strong enough to hold up a bridge; or an elevator to the stars.
These visions of the future are based in the discoveries of today, as a new science of materials emerges from the elemental building blocks of the universe, promising a future in which we can create virtually anything we want, atom by atom.
I'm David Pogue...
This wasn't in the contract!
...and I'm searching for the world's smartest materials, materials that sense and respond in ever more complex ways, giving us fantastic new abilities: an adhesive that lets you scamper up the side of a building;...
Could I not make myself a gecko costume that would let me climb walls?
...a plastic that heals itself like skin,...
These are bullet holes? Where's the bullets?
...and a new kind of material that makes objects invisible.
How far can we go in Making Stuff Smarter? Right now, on NOVA.
As the host of Making Stuff, I'm on a quest for the world's smartest materials. Lucky for me, that leads to Grand Bahama Island. But I soon learn this assignment isn't going to be "a day at the beach." NOVA wants me to take a swim with sharks.
Sharks are one of nature's greatest success stories, with ancestors reaching back to before the dinosaurs. When it comes to survival, it's easy to focus on their teeth, but their skin has led to a new material that can fight disease; an example of science taking ideas from the world's biggest materials lab, planet Earth.
For billions of years, Mother Nature's been experimenting, and that's given living things amazing abilities, like healing, flight and camouflage.
What can we learn from nature's ingenuity? Today, our teachers are the sharks, so I need to go where they live.
Should I be worried at all that I'm the only one on this crew who is not getting a suit of chainmail?
Tell my kids I love them.
As I approach the sharks, I can't help wondering: Was the crew just being friendly when they called me "old chum?"
But I'm here to examine the shark's skin, and to do that, I need to get even closer.
Diver Cristina Zenato has a plan. First, she attracts these Caribbean reef sharks using food and then reaches out to stroke one shark's nose.
For reasons that remain a scientific mystery, that puts the shark into a trance-like state called tonic immobility.
Cristina carries the shark over to me. Now, if I can just keep my hands away from those teeth, I can finally get a good look at one of the secrets of the shark's success, its skin.
Sharks are covered with scales called dermal denticles. Made from a tooth-like material, they're the reason the skin feels smooth in one direction, but like sandpaper in the other.
The denticles decrease drag and create less turbulence over the shark as it swims, a killer advantage.
Is there some evolutionary purpose to that?
CRISTINA ZENATO (Shark Expert):The shark being able to glide through the water, be silent, efficient and fast, all at the same time, without the prey really realizing it...to me, they're beautiful.
DAVID POGUE: But sharkskin denticles do more than enable a silent killer. They seem to prevent the growth of algae on the shark, and stealing that idea may save us from a lethal threat.
The overuse of antibiotics in medicine and farming has given rise to drug-resistant forms of common bacteria.
In some years, deadly superbugs, like M.R.S.A., mer´-sa, have killed more Americans than AIDS.
SHRAVANTHI REDDY (Chemical Engineer): The medical community, for so long, has been focused on killing as much of the bacteria as they can. Now, the interesting thing about bacteria is that you can't kill them all. You can kill 99 percent of them, but that one percent that you leave alive is the strongest one percent. And then you end up with resistant strains that can't be killed by traditional antibiotics.
DAVID POGUE: Shravanthi Reddy is the director of research for a company that makes this non-toxic plastic film called Sharklet™. Too tiny to see with the naked eye, its surface is covered in a repeating pattern of channels and pillars, each about a 20th the size of a human hair. It's called Sharklet because the pattern is modeled after the denticles of sharkskin, though it's far smaller.
Shravanthi has invited me to see what makes this seemingly ordinary piece of plastic a powerful medical weapon in our battle against bacteria.
SHRAVANTHI REDDY: We'll take our Sharklet film, which, you know, has the Sharklet pattern on it, and we've cut it into little small pieces. And we also cut up some smooth film that does not have the Sharklet pattern on it so we can compare.
DAVID POGUE: Next she adds bacteria to the dish and places it in an incubator for
...twenty four hours?
Finally, the results are in.
SHRAVANTHI REDDY: So, here's the really good comparison of the Sharklet surface and the smooth surface.
DAVID POGUE: So this, these are two samples treated the same way, same degree of magnification?
SHRAVANTHI REDDY: Yeah, yeah.
DAVID POGUE: On the smooth plastic, the bacteria have made themselves right at home, building a hefty colony.
And over here the Sharklet surface...
SHRAVANTHI REDDY: On the Sharklet surface you might see one or two cells inside the channels, but you don't see that big clumping the way you see it on the smooth surface. And it's really interesting, because there is no chemical difference between the two surfaces. It's the same material, no difference, other than this physical shape, alone.
DAVID POGUE: Sharklet is the brainchild of Tony Brennan, a biomaterials engineer at the University of Florida, in Gainesville. He studies how small creatures, like bacteria or algae, decide which surface to call home. He's tested other patterns, but, so far, only the denticle-inspired Sharklet has been effective.
TONY BRENNAN (Biomaterials Engineer): So it inhibits the bacteria. It doesn't kill them, to the best of our knowledge, but it, it just prevents them or slows them down substantially from establishing their colony. And bacteria love to be in colonies.
DAVID POGUE: Sharklet is already being tested in hospitals. It's been applied to doors, bedside rails, and other frequently touched surfaces. It may even be used on medical devices. If it's successful, it's an entirely new strategy for keeping bacteria at bay.
TONY BRENNAN: If we can slow the bacteria down, like all of our studies indicate, it's huge, because hospital-acquired infections represent one of the biggest costs we're dealing with in health care today.
DAVID POGUE: We think of sharks as the ultimate predators, but if the bacteria-evading principles of Sharklet hold, we may soon owe them our lives.
Sharklet contains a key lesson for scientists making stuff smarter.
Like chefs in a kitchen, we tend to think of materials in terms of their ingredients, but Sharklet's secret isn't what it's made of, it's the shape of its surface. In fact, some of nature's most ingenious tricks depend on surface structures built on a really tiny scale, far smaller than a human hair.
The iridescent color of this butterfly comes from the way light scatters across the textured surface of its wing, not because of any pigment.
This lotus leaf is self-cleaning, thanks to tiny needle-like protrusions that repel water. The droplets roll off the leaf taking the dirt with them.
And this desert beetle has tiny bumps on its back that collect moisture from the air, until just the right breeze blows the droplets down to its mouth.
In each case, nature has come up with something new just by manipulating the surface of a material on a very small scale. Now, scientists are trying to do the same thing, to create new powers, maybe even super powers, like Spiderman's.
Now, in case you aren't that familiar with Spidey, he depends on tiny structures, little hooks on the tips of his fingers that let him climb walls. Can we create a material, a smart adhesive, that will let us do the same?
Turns out the best bet for that doesn't come from a spider, but from another natural wonder, the gecko. It has a nearly limitless ability to climb. The weird part is that gecko feet don't feel sticky to the touch at all, yet somehow they stick and then unstick with ease, up to 15 times a second.
Now imagine if a human could to that.
But first we need to figure out the gecko's secret.
Kellar Autumn, from Lewis and Clark College, in Portland Oregon, did just that. He found the answer in the sheer number and design of the hairs on the gecko's feet.
KELLAR AUTUMN (Biologist): Geckos have millions of microscopic hairs on their toes. Of course we can't see this with our naked eye, because each hair is only one-tenth the size of a human hair, and each of those hairs branched down to billions of little split ends. And they can make such close contact with the surface that weak intermolecular forces can begin to add up to something really strong.
DAVID POGUE: Turns out geckos exploit something called the Van der Waals force.
If you think of an atom as a dancing couple, when you bring two atoms into very close contact, part of one atom can get attracted to part of the other. That very weak bond is the Van der Waals force, and it sticks atoms together. Proximity is the key, but bringing two materials that near each other is harder than you'd think.
KELLAR AUTUMN: When I put my hand on this table, I have an apparent contact area, which is just the surface area of my hand. But the true contact area is probably a ten-thousandth of that.
The surface of my hand is like a molecular mountain range coming down on a desert landscape. So only the tips of your molecules ever interact with the surface.
DAVID POGUE: But when a gecko places its foot against a wall, all those branching hairs are like a forest pressed against a desert. And when the gecko climbs, it drags its foot down, bringing not just the tips but the sides of all those hairs against the surface.
With up to half the area of the gecko's foot in close contact with the wall, the Van Der Waals forces really add up.
And we can measure just how powerful all that gecko hair can be.
KELLAR AUTUMN: What we measured really surprised us because the force was so large that a gecko's worth of hair, stuck at once, could lift about 250 pounds.
DAVID POGUE: That's a lot of stick in a very little package.
But it unsticks just as easily, when the gecko peels its toes off the surface.
KELLAR AUTUMN: This is an adhesive that's sticky when and where the gecko wants it to be, but it's actually not sticky the rest of the time: a smart adhesive.
DAVID POGUE: You know what? It just asked me if I want to save 15 percent or more on my car insurance.
So now that we understand gecko adhesion, can scientists match it?
I head over to Stanford, in Palo Alto, California, to visit Mark Cutkosky, who's building a climbing robot based on gecko principles.
MARK CUTKOSKY (Mechanical Engineer): Our motivation is that we want robots to go anywhere. So, we've had robots that can run along the ground for some time; the unmet challenge was to get robots that could go on vertical services, especially smooth ones.
DAVID POGUE: Imagine a world where robots could climb anywhere. Everything, from everyday tasks, like window washing, to specialized ones, like emergency rescue or surveillance, would change.
The key gecko feature on this robot is the material used for the pads on its feet. They're made from silicone rubber. Tiny wedges on the upper surface of the pad use the same gecko principle of directional adhesion, adhering when dragged down because of the close contact, but the rest of the time not sticky.
MARK CUTKOSKY: This is one pad on a little suspension with the weight about 200 grams below. If you just touch it to the surface it's not sticky at all, but if...
DAVID POGUE: Not at all.
MARK CUTKOSKY: ...if you let the weight hold it,...
DAVID POGUE: Oh, man!
MARK CUTKOSKY:...it sticks perfectly.
DAVID POGUE: So when the weight is pulling down, that's the directional thing you were talking about?
MARK CUTKOSKY: Exactly. And then, to get it off, you actually have to remove the weight, and then it will lift right off.
DAVID POGUE: So it's quite firm now but if I lift up, oh, my gosh, it's like the electricity was turned off.
MARK CUTKOSKY: That's directional adhesion.
DAVID POGUE: And that's what the real gecko does?
MARK CUTKOSKY: And that's what the gecko does. And, in fact, if you've ever seen a gecko going headfirst down a wall, you'll see that it's turned its rear feet backwards. And it has to, otherwise it wouldn't stick.
DAVID POGUE: Time to see the gecko in action: the lab's most recent creation, Stickybot III.
MARK CUTKOSKY: This is a ground granite slab, like a kitchen countertop.
DAVID POGUE: Okay.
MARK CUTKOSKY: So, it's too smooth to use something like little hooks or spines, so we really have to rely on the adhesion.
DAVID POGUE: Start the gecko!
Pretty impressive; and especially when they show me a piece that supports 45 pounds.
I start having my own ideas.
If had gloves made of this stuff, plus socks, could I not make myself a gecko costume that would let me climb walls?
MARK CUTKOSKY: You're not designed to be a gecko, you'll get tired, but, but you should stick.
DAVID POGUE: They say gecko adhesives would be useful anywhere you need extra grippiness, you know: tires or surgical bandages or sports equipment. But, come on, we all know the real reason to develop gecko adhesives. So you can do this!
Okay, I'm busted. Nobody has gecko gloves this good, at least nobody who's talking (military) but they're coming. Mark my words.
Until then, Hollywood's Spiderman has got the job.
Gecko adhesives and Sharklet mimic actual structures found in nature, but can we make stuff even smarter by building into materials life-like reactions, such as healing?
Even if I just cut myself while shaving—ow!—my body initiates an emergency response. Immediately, it constricts broken blood vessels to lessen the bleeding. Platelets clump together to plug up the wound.
That's just the beginning of a miraculous cascade of actions to repair the damage.
Can we design materials that can do that? Heal themselves?
Iraq, 2004: the U.S. military faced a new and devastating threat in its battle with insurgents.
CHAD KNOWLES (Iraq War Veteran): The fuel tankers in theater were actually being shot at by the insurgents, creating holes that would actually leak a lot of the fuel out, creating a problem of safety for the soldiers.
DAVID POGUE: The tankers didn't explode like they do in the movies, but with fuel spilling out, setting them on fire didn't take much.
The Pentagon urgently sought a solution. A company in Salem, Oregon, High Impact Technology, offered up a new smart material that takes its cues from biology. I'm here to see how it works.
Here's a standard fuel tank that would be used on a military truck.
And here's one with High Impact Technology's unique coating called "Battle Jacket."
RUSS MONK (Director of Operations, High Impact Technology): This is a self-healing, self-sealing coating that was developed for ballistic events in theater.
DAVID POGUE: Is that military-ese for bullet holes?
RUSS MONK: Exactly.
DAVID POGUE: The gun used for the test is the weapon of choice in Iraq, the AK-47.
[Sound of gunshots.]
Oh, yeah!
[Sound of gunshots.]
Target terminated.
The threat is obvious. Just one bullet hole will spill 150 gallons an hour, but what happens next is so surprising, it's hard to believe.
Let's take a look. Exhibit A: three nasty bullet holes leaking fuel, ready for the enemy to light with a match and blow up the truck.
TOM OHNSTAD (Director of Engineering, High Impact Technology): Yes, sir.
DAVID POGUE: Exhibit B: Oh, he missed! Oh, is this what we're talking about?
TOM OHNSTAD: That is it.
DAVID POGUE: These are bullet holes?
RUSS MONK: That's actually the black powder off the bullet that actually made the mark.
DAVID POGUE: No!
TOM OHNSTAD: That is a telltale sign of a round going through the, uh...coating is now, it immediately started to self-seal.
DAVID POGUE: Where's the bullets?
RUSS MONK: They're in the tank.
DAVID POGUE: They're inside?
RUSS MONK: They actually just drop to the bottom, and you pick them up with the filters.
DAVID POGUE: Ingenious!
It all happens so fast that even with this high-speed camera, running at five thousand frames a second, you can barely see it.
There's the bullet; there's the hole, or what was one.
What kind of stuff does that?
Back at the lab, the Battle Jacket guys break it down for me.
If I had to guess, I'd say this contraption is spraying your magic coating onto the tanks in here.
RUSS MONK: Absolutely correct.
DAVID POGUE: It's like the world's biggest spray-tanning salon.
RUSS MONK: And when that is done, it looks like this.
DAVID POGUE: So this a cross-section of the tank wall, right?
RUSS MONK: And the three shots you did today, that's what it looks like inside the tank.
DAVID POGUE: Oh, man. So that would have leaked out big time.
RUSS MONK: That's correct.
DAVID POGUE: Battle Jacket goes on in three distinct layers.
The inner and outer layers are the same material, a specially formulated plastic that can stretch to more than double its size. When the bullet tears through the coating and the tank wall, the plastic stretches around it and then snaps shut, leaving a pinhole-sized leak.
The thin middle layer does the sealing. It contains tiny plastic beads that absorb the leaking fuel.
RUSS MONK: It absorbs it and starts swelling. It'll grow up to 20 times. It's like a cork that actually opens up, and it locks down that wound. So you get the self-healing from the coating, the self-sealing from the chemistry.
DAVID POGUE: There's one last key element: the physics of the fuel. I get to see that in a special test tank with a Plexiglas® side.
RUSS MONK: Okay, David, whenever you're ready.
[Sound of gunshot.]
DAVID POGUE: Here's the bullet entering. The impact creates a shockwave inside the tank that actually pushes some of the fuel out the bullet hole, starting the chemical reaction that seals it shut.
The arrival of Battle Jacket in Iraq, in 2005, changed the game there.
CHAD KNOWLES: The strategy of setting the tanks on fire has kind of gone away. I think, predominantly, because the insurgents really don't understand, they don't think they're hitting the tank. That's how successful it's been.
It's a very elegant solution.
DAVID POGUE: Battle Jacket is just the beginning.
Imagine a smarter world where cars repair their own dents, bridges repair their own rust or concrete repairs its own cracks. Self-healing is a powerful idea, invented by evolution, and now, thanks to materials science, shared with the world of stuff.
The only thing that's bothering me is that we only shot three pathetic bullets. Don't those guns hold more than that?
TOM OHNSTAD: They do.
DAVID POGUE: I mean, this is NOVA. Let's finish big.
TOM OHNSTAD: Let's finish big.
DAVID POGUE: Gentlemen, commence fire, please!
[Sound of gunshots.]
That's better!
Battle Jacket is a smart product, but what if you wanted an even smarter material, one with a more varied response? To find stuff like that, we're better off out of the lab and at the movies.
The T-1000 from Terminator 2 could have won an Oscar for "best adapting material," because this liquid guy can sense, respond and even self-heal. It's the material itself that does things. He's a life-like fluid that's very, very smart.
Okay, that's science fiction, but in the search for smarter materials, engineers have taken a hard look at some liquids with very strange behaviors. They're called non-Newtonian fluids.
I travel to North Carolina, to the Lord Corporation, which manufactures one, but when I arrive, I have a burning question for Engineer Lynn Yanyo.
Forget non-Newtonian, what's a Newtonian fluid? She offers to show me one.
LYNN YANYO (Polymer Engineer): This is a Newtonian fluid. Take a look at that.
DAVID POGUE: Turns out this Newtonian fluid is water.
What makes it Newtonian? I've never thought of it as Newtonian.
LYNN YANYO: It makes it Newtonian because Isaac Newton discovered that there's a relationship between how hard it is to move it and the viscosity.
DAVID POGUE: Viscosity meaning thickness?
LYNN YANYO: The thickness, resistance to flow.
DAVID POGUE: When you try to move something through water, the resistance is directly proportional to how fast you move it: twice as fast is twice as hard.
Now, that's kind of what you'd expect, but amazingly that's not true for lots of other fluids, the non-Newtonian ones, like ketchup. Ever wonder why it's so hard to get it out of a glass bottle?
That's because, unlike water, it thickens at rest, its molecules creating a weak structure that resists flowing.
Yes, I remember this from my hamburger days. Ladies and gentleman, it does not flow! Lynn is staking her scientific reputation and her hairdo on the non-flowingness of ketchup.
But if you can get it started, that structure breaks down, and the ketchup thins and flows.
Here's another non-Newtonian fluid, in fact, a lot of it.
Oh, here it comes, definitely a liquid.
This cornstarch and water mixture is known as Oobleck. The word comes from an old Doctor Seuss story. Oobleck dramatically changes its viscosity, or thickness, depending on how fast you try to move it.
Keep the action soft and it flows like a liquid, but hit it hard and it's solid enough that you can run across it.
This liquid, when I squeeze it tight, turns into a rock and then when I let go it turns back into a liquid, what is happening?
LYNN YANYO: We like to call this, the Three Stooges effect.
DAVID POGUE: That's not the scientific term! What do you mean the Three Stooges effect?
LYNN YANYO: Well, you know when the Three Stooges tried to get through the doorway and they couldn't? The corn-starch doesn't want to get out of its own way. So, when you push on it really hard, it can't move out of the way fast enough.
And if you hit it really slowly, you can go right through it like a liquid.
DAVID POGUE: So, it's a liquisolid. You know, it depends on the pressure, the speed or something.
LYNN YANYO: It depends on the speed at which you try to move anything through it.
DAVID POGUE: Oobleck's a lot of fun. Be sure to fill your neighbor's pool with it.
Oh, it's got me!
But non-Newtonian fluids designed into the right system can save your life. Imagine a material that can adjust its thickness to absorb the seismic shakes of earthquakes or dampen the vibrations caused by wind that can pull a bridge apart.
That's what the non-Newtonian fluid Lynn has in her hand can do.
LYNN YANYO: So, the interesting thing about this is that it's very responsive to a magnetic field, and it's a lot like Oobleck. Take this spoon and scrape around in there.
DAVID POGUE: Okay. Oh, man, that is unbelievable, it's cement! It's...
LYNN YANYO: So now, scoop some of that up, and just take it out of the magnetic field by lifting it up.
DAVID POGUE: Mmm, it's...oh, no way!
This is like X-Men stuff.
So, it's a magnetic liquid.
LYNN YANYO: Mm-hmm, we call this magneto-rheological fluid.
DAVID POGUE: Do you got a shorter nickname?
LYNN YANYO: M.R.
DAVID POGUE: M.R. fluid, can I call it Mr. Fluid?
LYNN YANYO: No.
DAVID POGUE: A typical M.R. fluid consists of tiny iron particles suspended in a fluid like oil.
Without a magnetic field, the liquid flows freely, but add a magnetic field, and the metal particles line up, increasing the fluid's thickness.
Lord puts that variable viscosity to work in devices like shock absorbers.
LYNN YANYO: And then there's another suspension that's larger, and that's for really heavy-duty vehicles.
DAVID POGUE: Heavy-duty vehicles like Humvees. For the military, a smooth ride isn't about luxury.
How well a vehicle handles bumps determines how fast it can safely travel, as well as how fatigued its passengers become, both life and death issues on the battlefield.
Out here in the woods, I'm going to see just what kind of a difference using a smart material can make in a Humvee's performance.
Good heavens.
LYNN YANYO: Well, here you are. This is your ride, and for this first ride we have this military Humvee, and it is just retrofitted with the conventional shocks that you would have when this was used out in the field.
DAVID POGUE: A typical shock absorber is built around a piston filled with oil. When the piston moves down, it forces the oil from one chamber to another through small holes.
The thickness of the oil and the size of the holes determine how much force that takes. If neither varies, the shock is a one-size-fits-all dampening solution, no matter how bumpy the road is.
How do you make this seat recline anyway?
Jeez! Oh, my god! That was pretty bouncy. You should sell tickets to this thing.
For round two, the Humvee gets the smart shock absorbers. They also use a piston design, but they add M.R. fluid, full of iron particles, and an electromagnet where the fluid flows through the holes.
A computer controls the electromagnet in real time, varying the viscosity of the M.R. fluid. This system adjusts how much force is needed to move the piston in response to the bumpiness of the road.
That makes the shock absorber tunable. It can react nearly instantaneously to different size vibrations. And that's very smart.
Oh, this is nothing. How do I adjust the A.C.?
So, you're telling me that was the exact same speed?
DRIVER: Exact same speed.
DAVID POGUE: Well, I can tell you, if I were a soldier, I'd vote for these shock absorbers.
LYNN YANYO: Oh, yeah. You can see why that's a huge difference for those guys, if they have to travel 25 miles in that. And the vehicles will last longer.
Don't forget your seatbelt!
DAVID POGUE: Yeah, yeah.
The abilities of smart fluids scale far beyond Humvees. Engineers see a big future for them in bridge construction, to squelch vibrations caused by wind and bad weather. And even for use in buildings to counteract the awesome power of earthquakes, like a steadying hand.
Sophisticated smart materials can react to outside forces to protect bridges and buildings, but they can be even more lifelike, allowing us to realize one of humanity's oldest dreams?
The flying ability of birds has always captured the human imagination.
But when it comes to flying, birds have us beat on a bunch of levels.
Sure we can fly in a hang glider and gain some of the sense of how a bird soars. Or we can build jet fighters that can dive from the sky, the way a bird can tuck its wings in and shoot toward Earth. But a bird does all that and more thanks to an elegant feature that's the envy of aircraft designers: a flexible, shape-changing wing.
Ironically, heavier-than-air flight started out using a more bird-like wing than we use today. The Wright brothers employed a steering system of wires and pulleys that actually bent the wings of the Wright Flyer to control its direction, not unlike the way a bird steers by altering its wing shape. But as planes became bigger, designers needed stiffer materials and hinged parts for flight control. The legacy of that is the mechanical complexity of your average airliner wing.
It's got ailerons, flaps, slats and airbrakes. That's a lot of motors, hinges and moving parts, all of which disrupt airflow and add weight, a big loss in efficiency.
But imagine if all that shape-changing could be done the way a bird does it, just by bending the wings. That may sound way out, but for more than a decade at Virginia Tech, in Blacksburg, Virginia, Dan Inman has been exploring just that kind of shape-changing wing, using smart materials.
Today's the first test flight of this experimental remote control aircraft built by students in his lab.
DANIEL INMAN (Materials Scientist): We're trying to make a shape-changing wing, try to imitate, uh, more of what a bird would do, by having the wings bend, rather than having a discrete flap, like in a normal aircraft. And so this doesn't. It has a smooth surface.
DAVID POGUE: Inman can ditch the flaps and the various cables and motors to control them, by bending the wing using a smart material embedded in those plastic strips. It's called a piezoelectric ceramic.
That's a mouthful, but these materials change their shape in response to an electric charge. In this case, that's supplied by batteries on the plane and controlled electronically from the ground.
Now this is going to be the very first flight in this configuration, right?
DANIEL INMAN: Absolutely.
DAVID POGUE: Have you considered the fact that you're on a high definition national television broadcast and it could flop?
DANIEL INMAN: Absolutely.
DAVID POGUE: So this is it? The maiden flight?
And flop it does, due to a faulty wire.
But you can't keep the Virginia Tech Hokies down. One spare fuselage and an hour later, they're back for round two.
STUDENTS: One, two, three, Hokies!
DAVID POGUE: She flies, she flies!
Second time's the charm.
And chock up a big win for Birdman Inman and his team.
For the pilot, learning how to fly using the new wings is like learning how to a walk, but it's easy to see the bird in the plane's acrobatics.
With engineers putting more avian back into aviation, one day you may look out your airliner's window to see smart materials bending the trailing edge of the wing.
You might even see the entire shape of the wing altering in flight, thanks to some metals with great memories.
This wire NOVA logo is made from a nickel and titanium alloy. The metal was invented in the late fifties for use in missile nose cones, but then, by accident, it was discovered to have an astonishing quality.
If I stretch out this wire and then apply a little heat, it snaps back to its original size and shape. Scientists call materials like this "shape memory alloys," or S.M.A.s.
But they might as well call them artificial muscles. That's how they're being put to work here. This jellyfish robot from Virginia Tech swims without any kind of motor. In a design inspired by real jellyfish, it's propelled by the contractions of an artificial muscle, made of metal, embedded in its silicone bell. Electric current heats the material to trigger the action. Eventually a small battery will provide the power.
The goal of this work, paid for by the Navy, is a motion-detecting buoy that's inconspicuous.
DANIEL INMAN: If it looks like a jellyfish, then maybe someone will think it is a jellyfish and not bother it.
DAVID POGUE: Oh, I see. So we could actually spy on the bad guys.
"Wait! Who goes there? Oh, it's just a jellyfish."
Even beyond artificial muscle, shape-shifting metals and plastics may be the shape of things to come.
Imagine if your watch could morph into your cell phone, or your family sedan could turn into a roadster.
But today, shape memory alloys are saving lives. This is a stent. It's designed to keeps an artery open. Surgeons can shrink it down for insertion and then the heat of the body, like this hot water, expands it into place. Smart: just one example of how new materials have revolutionized the world of medicine.
That's a revolution that's been decades in the making. I head to Massachusetts to see a professor at M.I.T. who runs the largest bioengineering lab in the world.
For many, chemical engineer Bob Langer personifies the new role of material science in medicine.
Wow, this is your office?
ROBERT LANGER: Yeah, yes it is.
DAVID POGUE: Too bad nobody's recognized your work.
ROBERT LANGER: Well, I've been lucky, but it didn't start out that way. I mean, you know, when I started working, I think for the first 10 or 15 years, nobody cared about what we were doing, at all.
DAVID POGUE: After graduating from M.I.T. in the 70s, Bob entered an unlikely field, cancer research, an area with few, if any, chemical engineers.
At that time, medical advances depended on whatever was at hand.
ROBERT LANGER: What doctors would do is, they would go to their house, they'd find an object that kind of resembled say the organ or tissue that they were trying to fix, and then they'd use it in a patient.
DAVID POGUE: Doctors cobbled together solutions. Sausage casings became the basis for dialysis machines; squishy mattress stuffing was put inside breast implants; and the elastic in ladies' girdles was used for artificial hearts.
Instead of this scavenger hunt, Langer took an engineering approach.
ROBERT LANGER: Rather than pick something from your house, why can't you ask the design question, "What do you really want, from an engineering standpoint, chemistry standpoint, biology standpoint?" And then, "Could we synthesize it?"
DAVID POGUE: Over the years, Langer's approach has paid off.
Some of his biggest breakthroughs have been in drug delivery. He invented plastic implants that can release a drug at a steady rate for up to five years.
So how do you do that? How do you control the rate and the duration?
ROBERT LANGER: Well, there are several ways to do it. It could have what we call tortuosity in it, winding paths. When you make these winding paths in a piece of plastic, it'll take a long time for the molecules to get through.
DAVID POGUE: A drug molecule encased in Langer's plastic is like a car trying leave a city without a map.
In Manhattan, the grid system makes that fairly easy. Just going straight takes you to the outer edge. That's like a low tortuosity fast-release plastic.
But a high tortuosity delayed-release plastic is like Boston. With its winding streets, you might find yourself lost for days, months, maybe even years.
So are these smart materials you're working with?
ROBERT LANGER: They are. I'd say they're the first generation of smart materials, because they're really aimed to deliver at the right rate, to degrade at the right rate. So, yeah, I think they're pretty smart.
DAVID POGUE: Langer's second generation, still in the research phase, takes an even smarter approach.
Traditional intravenous chemotherapy "nukes" the body with toxic chemicals to kill cancer cells. The problem is that the required dose also harms a lot of healthy tissue.
Langer's brought a new weapon to the battle. Tiny drug particles, nano-sized—that's billionths of a meter—to be sent, special delivery, to just the cancer cells.
ROBERT LANGER: Targeted chemotherapy, where you could take the nuking material, so to speak, put it in the nanoparticle, and have the nanoparticle direct it right to the tumor, and not other places in the body.
DAVID POGUE: How does that work? How can it know what a cancer cell is?
ROBERT LANGER: It's actually very challenging. It's really developing a way to decorate the outside of it, with just the right combination of materials.
DAVID POGUE: He starts with a nano-particle of anti-cancer drug. That gets encased in a plastic that releases the drug over time. That, in turn, gets a special wrapping that disguises the package as a water molecule to fool the body's immune system.
And last, but not least, the address where it should be delivered: a key that will only fit the lock of cancer cells.
This is just one slice of Langer's work at the intersection of materials and medicine. He's got 700 patents and counting, in drug delivery, tissue engineering and even hair products.
ROBERT LANGER: Robert Frost said it very well in his poem, you know? I ended up taking "the road not taken," and I think it's a path that now many more people are taking and I think it's a path where engineers and materials scientists can just do a lot of good for the world, and so I think it's a wonderful path.
DAVID POGUE: Forty years ago smart materials barely existed. Now not only can they mimic nature, they can move radically beyond it to accomplish what has always seemed impossible.
Take camouflage. Nature is full of animals that have evolved to stay hidden. The lionfish has a fixed appearance that allows it to fade into a specific environment, but the octopus can change its coloring, to blend into different backgrounds.
Now, new discoveries in materials offer us an approach to hiding that nature's never found. Why not just cloak yourself in invisibility?
The road to just such a cloak begins with Sir John Pendry, a theoretical physicist and mathematician at Imperial College, London. He's come up with new metamaterials, "meta" meaning "beyond." This one is made of plastic, encasing tiny copper rings. It's an experimental model, but someday, metamaterials like it may influence visible light in mind-blowing ways.
JOHN PENDRY (Theoretical Physicist): I produced the design and a formula for, for hiding something. We, we said "If you want to completely...make something completely invisible, then this is what you do."
It started off a huge research program.
DAVID POGUE: I travel to Duke University, in North Carolina, to talk with one of Pendry's collaborators on the invisibility cloak and the first to actually build one.
Thanks to the movies, like H.G. Well's Invisible Man, I thought I knew what to expect.
You're the guy developing the invisibility cloak?
DAVID SMITH (Electrical Engineer): That's right.
DAVID POGUE: I have to say, it works amazingly well. I can't even see you.
DAVID SMITH: Well, actually, I'm over here.
DAVID POGUE: Oh, sorry.
Maybe David Smith has something more like that Harry Potter movie.
DANIEL RADCLIFFE (As Harry Potter/Harry Potter and the Sorcerer's Stone/Film Clip): My body's gone!
RUPERT GRINT (As Ron Weasley/Harry Potter and the Sorcerer's Stone/Film Clip): I know what that is. That's an invisibility cloak!
DAVID POGUE: Heck! Even I can get into that act.
As a television professional, I use a little something we like to call the green screen.
Woooo! I'm beheaded.
All this techno-trickery does make one thing clear: making something invisible is really about trying to make what's behind an object visible, bringing the reflected light of the background around the object, like water flowing around a rock in a stream.
DAVID SMITH: So, this should probably strike you, just from the geometry, as to what its function is. So, the hidden region is right here. A wave comes in.
DAVID POGUE: Anywhere in here?
DAVID SMITH: Anywhere in there, that's right.
DAVID POGUE: Oh, we're talking big stuff. I could put a piece of cheese...
DAVID SMITH: Right.
DAVID POGUE: ...or a marble...
DAVID SMITH: Right.
DAVID POGUE: Oh, wow.
DAVID SMITH: And, uh, you're waves could come in and this effected material causes them to get moved like this and then restored on the other side.
DAVID POGUE: There is a catch. Visible light waves, from red to blue, are just a narrow slice of the electromagnetic spectrum. Smith is working in a different slice, where the wavelengths are longer, in the microwave region.
That's why his invisibility cloak is, well, visible.
It's not working yet, though, I can see right through it.
DAVID SMITH: You're looking with the wrong wavelengths.
DAVID POGUE: Oh right! Don't think about visible waves, think about...okay.
DAVID SMITH: Microwaves.
DAVID POGUE: Time to test the cloak in this—basically a giant microwave oven—and I get to choose what to hide.
You know what? This is in the spirit of that fabled lady, when microwave ovens first came out, she washed her poodle and put it in the microwave to dry it. Yeah, except, uh, actually, in this case it would have protected the poodle, right?
DAVID SMITH: Would've protected the poodle.
DAVID POGUE: The microwaves would have gone right around it, and the poodle would not have been cooked.
DAVID SMITH: That's right.
DAVID POGUE: With the frog in place, Smith starts the test.
Here's a graphic display of what's going on in the tester, looking down from above. A microwave generator on the left sends out test waves. If there's no object in the tester, they cleanly pass from left to right. On the other hand, if my frog sat, uncloaked, in the middle, it would scatter the waves, disrupting the pattern.
Now, if my frog had a perfect cloak, the waves would pass around it, cleanly emitted on the other side, without any change.
Here's Smith's actual result of the test. It isn't perfect—you can see the waves aren't the same after hitting the cloak—but it's getting there.
So, it looks like it's actually, sort of, working.
DAVID SMITH: It's working. If you were sitting here, what you would see is no distortion, you'd see, basically, a reduction in intensity, but you wouldn't be able to make out what was being scattered in here.
DAVID POGUE: You wouldn't...
DAVID SMITH: So you wouldn't be able to see your frog.
DAVID POGUE: ...even though you're looking right at it?
DAVID SMITH: Right.
DAVID POGUE: With your microwave-sensitive eyes.
DAVID SMITH: That's right.
DAVID POGUE: Well now, what about the frog, can the frog see him?
DAVID SMITH: No, the frog can't see him.
JOHN PENDRY: If you're inside one of these invisibility spheres, you wouldn't be able to see outside, and if you looked at the walls, what you would see would be a reflection of yourself. From the inside, the appearance is, is as of a mirror.
DAVID POGUE: Of course, that's not a problem yet. Scientists haven't created a cloak that...
...works with visible light, though they're getting ever closer.
And invisibility is just one application. The promise of metamaterials is a revolution in our manipulation of light. We may see new powerful lenses, that can focus on something as small as a virus attacking a cell, or new technologies that scan for cancer or hidden explosives.
It's a new frontier and, like human imagination, it has no limits, yet. With all our technology and materials, it's easy to think we're the planet's best inventors, but life has been experimenting with the raw materials of earth for far longer.
Billions of years of evolution have created a vast array of plants and animals with amazing abilities of their own. As our understanding of biology and our materials deepens, a new world has opened up, one where nature's ingenuity and human ingenuity can combine.
And that's Making Stuff Smarter.
Broadcast Credits
Making Stuff: Smarter
- Host
- David Pogue
- Written, Produced and Directed By
- Daniel Mccabe
- Executive Producer
- Chris Schmidt
- Executive Producers
- For Powderhouse Productions
- Joel Olicker
Tug Yourgrau - Associate Producer
- Minna Kane
- Edited By
- Daniel Mccabe
Justin Vaida - Additional Editing By
- Brian Cassin
Jean Dunoyer - Directors of Photography
- Gary Henoch
Stephen Mccarthy - Additional Photography
- Dennis Boni
Robert Burns
Tim Cragg
Joe Livolsi - Underwater Camera
- Eddy Raphael
- Sound Recordists
- Frank Collins
Philip Perkins
David Wade
Greg Hinnen
Anna Rieke
Glen Abbey
John Cameron
Tyler B. Stephens
Adam Prescod
Geoff Gann
Kevin Cook
Glen Ackers
Mark Arees
Dave C. Manahan - Grips and Gaffers
- Jesse Hubbell
Ari Manin
Joshua Weinhaus
Brian Patriacca - Production Assistant
- Daniel V. Parsons
- Music
- Lunch Special Music
- Animation
- Edgeworx, Llc
- Additional Animation
- halfadeer, vfx
Pixeldust - Production Managers
- Alexandra Mchale
Diane Knox - Post Production Supervisors
- Kevin Young
Michael Fallon - Assistant Editors
- Eric P. Gulliver
Peter Hyzak
Jim Fetela - Online Editor / Colorist
- Julie Kahn
- Audio Mix
- Heart Punch Studio, Inc
- Interns
- Katie Duffy
Nicole Jaques
Travis Kelley
Michael Ryan
Zach Vitale - For Powderhouse Productions
- Post Production Manager
- Melissa Walter Richards
- Senior Production Coordinator
- Carlin Corrigan
- Vp of Production
- Daniel Miller
- Senior VP of Production and Post
- Robert Kirwan
- Senior VP of Sales and Development
- Seanbaker Carter
- Archival Material
- Daniel Zatz / Footage Search
Footage Provided By Thought Equity Motion
Getty Images
iStockphoto
NASA
Nature Publishing Group
Photolibrary
Pond5
Streamline Films, Inc. - Special Thanks
- Producers Gratefully Acknowledge the Cooperation of the Materials Research Society.
- Richard A. Souza
Amy Moll
Kristin Bennett
Jerry Floro
Megan Frary
Kevin Jones
Tommie Kelley
Alex King
Aditi Risbud
Stephen Streiffer
Rick Vinci
Sandra Devincent Wolf - Special Thanks
- Wallaby Ranch
Florida Museum of Naturalhistory
Professor Stephen Sass, Cornell University - NOVA Series Graphics
- yU + Co.
- NOVA Theme Music
- Walter Werzowa
John Luker
Musikvergnuegen, Inc. - Additional NOVA Theme Music
- Ray Loring
Rob Morsberger - Post Production Online Editor
- Michael H. Amundson
- Closed Captioning
- the Caption Center
- Publicity
- Eileen Campion
Victoria Louie
Karen Laverty - Marketing
- Steve Sears
- Researcher
- Kate Becker
- Novaadministrator
- Kristen Sommerhalter
- Production Coordinator
- Linda Callahan
- Paralegal
- Sarah Erlandson
- Talent Relations
- Scott Kardel, Esq.
Janice Flood - Legal Counsel
- Susan Rosen
- Associate Producer Post Production
- Patrick Carey
- Post Production Supervisor
- Regina O'Toole
- Post Production Editor
- Rebecca Nieto
- Post Production Manager
- Nathan Gunner
- Compliance Manager
- Linzy Emery
- Development Producer
- Pamela Rosenstein
David Condon - Supervising Producer
- Stephen Sweigart
- Business and Production Manager
- Jonathan Loewald
- Senior Producer and Project Director, Margret &Amp; Hans Rey / Curious George Producer
- Lisa Mirowitz
- Coordinating Producer
- Laurie Cahalane
- Senior Science Editor
- Evan Hadingham
- Senior Series Producer
- Melanie Wallace
- Executive Producer
- Howard Swartz
- Managing Director
- Alan Ritsko
- Senior Executive Producer
- Paula S. Apsell
Produced by Powderhouse Productions
A NOVA Production by Powderhouse Productions for WGBH
© 2011 WGBH Educational Foundation
All Rights Reserved
Image
- (David Pogue)
- ©WGBH/Mark Ostow, ©iStockphoto.com/Guillermo Lobo
Participants
- Kellar Autumn
- Biologist
- Tony Brennan
- Biomaterials Engineer
- Mark Cutkosky
- Mechanical Engineer
- Daniel Inman
- Materials Scientist
- Chad Knowles
- Iraq War Veteran
- Bob Langer
- Chemical Engineer
- Russ Monk
- Dir. of Operations, H.I.T.
- Tom Ohnstad
- Dir. of Engineering, H.I.T.
- John Pendry
- Theoretical Physicist
- David Pogue
- New York Times Tech Columnist
- Shravanthi Reddy
- Chemical Engineer
- David Smith
- Electrical Engineer
- Lynn Yanyo
- Polymer Engineer
- Cristina Zenato
- Shark Expert
Education and Outreach Resources
Preview
Full Program | 53:24
Full program available for streaming through
Watch Online
Full program available
Soon